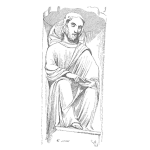
by Alan Ross
When you think about maintenance from a reliability perspective rather than an engineering perspective, it becomes clear that transformers are somewhat of a red-headed stepchild, even though they are the heart of the electrical system.
Why? Let’s take a closer look.
The reliability industry has grown out of the maintenance industry. At the very core of the maintenance industry is the Computerized Maintenance Management Systems (CMMS). These systems are designed to tell us what needs to be repaired or maintained and when. Planning for the right tool at the right time at the right place with the right person to keep an operation running is the job of the Maintenance and Reliability team, and the CMMS is vital to that function.
The CMMS, or Enterprise Asset Management (EAM) system, applies standards for maintaining a group of assets (be it motors, compressors, conveyor belts… any class of equipment). One critical component of the CMMS is the “Mean Time Between Failure,” or MTBF. Increasing the MTBF to avoid a failure is a major goal of the Maintenance and Repair (M&R) department since a component failure might shut down an entire productive line or even the entire plant.
Breakers, relays, switchgear, and transformers are absent from most CMMS systems, which puts them at risk.
And now we see the problem; transformers don’t fit into a pattern since the MTBF for many classes of power transformers is over 38 years. Partly because they are very specialized equipment, and partly because CMMS systems are based on design parameters for larger quantities of equipment, transformers have been “left out” of the M&R function.
If transformer maintenance is not part of the CMMS, then you don’t know when it’s going to fail or not fail. The same is true for all high voltage equipment. Relays, transformers, breakers, switchgear… these are the four largest components of a high voltage system and the main CMMSs do not support them. While test data may get stored in some CMMSs, it is simply data with no standardized maintenance based on that test data.
Filling that gap is not easy. Major utilities are developing proprietary systems to do just that given the unique nature of this equipment in their system, but high energy industrial users cannot justify the expense. Companies like SDMyers and On Now Digital have created systems that in many ways function like a CMMS for electrical systems or transformers specifically.
Systems such as SiteLine function like a CMMS or high voltage equipment.
Ask most electrical system maintenance professionals why they test their transformers and you will hear, “because the insurance company requires it.” Ask why they test their motors, conveyors or any other major piece of productive equipment and the answer is likely to be, “because it is part of the CMMS.”
Transformer failure can be catastrophic. Using a specialized CMMS for this special class of assets is critical to extend the life of these assets. We do it for all the other assets, why not this critical one?
When you think about maintenance from a reliability perspective rather than an engineering perspective, it becomes clear that transformers are somewhat of a red-headed stepchild, even though they are the heart of the electrical system.
Why? Let’s take a closer look.
The reliability industry has grown out of the maintenance industry. At the very core of the maintenance industry is the Computerized Maintenance Management Systems (CMMS). These systems are designed to tell us what needs to be repaired or maintained and when. Planning for the right tool at the right time at the right place with the right person to keep an operation running is the job of the Maintenance and Reliability team, and the CMMS is vital to that function.
The CMMS, or Enterprise Asset Management (EAM) system, applies standards for maintaining a group of assets (be it motors, compressors, conveyor belts… any class of equipment). One critical component of the CMMS is the “Mean Time Between Failure,” or MTBF. Increasing the MTBF to avoid a failure is a major goal of the Maintenance and Repair (M&R) department since a component failure might shut down an entire productive line or even the entire plant.
Breakers, relays, switchgear, and transformers are absent from most CMMS systems, which puts them at risk.
And now we see the problem; transformers don’t fit into a pattern since the MTBF for many classes of power transformers is over 38 years. Partly because they are very specialized equipment, and partly because CMMS systems are based on design parameters for larger quantities of equipment, transformers have been “left out” of the M&R function.
If transformer maintenance is not part of the CMMS, then you don’t know when it’s going to fail or not fail. The same is true for all high voltage equipment. Relays, transformers, breakers, switchgear… these are the four largest components of a high voltage system and the main CMMSs do not support them. While test data may get stored in some CMMSs, it is simply data with no standardized maintenance based on that test data.
Filling that gap is not easy. Major utilities are developing proprietary systems to do just that given the unique nature of this equipment in their system, but high energy industrial users cannot justify the expense. Companies like SDMyers and On Now Digital have created systems that in many ways function like a CMMS for electrical systems or transformers specifically.
SiteLine
Systems such as SiteLine function like a CMMS or high voltage equipment.
Ask most electrical system maintenance professionals why they test their transformers and you will hear, “because the insurance company requires it.” Ask why they test their motors, conveyors or any other major piece of productive equipment and the answer is likely to be, “because it is part of the CMMS.”
Transformer failure can be catastrophic. Using a specialized CMMS for this special class of assets is critical to extend the life of these assets. We do it for all the other assets, why not this critical one?
Alan Ross is the President of the Electric Power Reliability Alliance (EPRA). He is responsible for leading the alliance to build electric system reliability in the industrial and commercial marketplace. Formerly, Alan was the Vice President of Reliability at SD Myers.
Leave a Reply