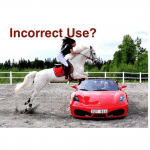
Mission profiles are fundamental to any reliability prediction being valid. Without clearly defined environmental and use profiles there will be a long chain of inaccuracy that accumulates into significant errors within a product.
This is what occurs at the following stages, or tools, if the mission profile or environment profile changes after its completion.
- DFMEA: Failure modes may be excluded. Critical failure modes may be ranked low for occurrence and not be addressed
- DOE: Stresses may not be included in the matrix. Resulting singular and interaction failure modes will not be discovered in advance.
- Design validation: Design will be approved for a base use case when in fact it can not handle nominal stress and requires significant redesign in late stages
- Accelerated Life Testing: Life projections are in accurate by orders of magnitude
- Stress Margin Testing: Actual operational margins are less than projected. Variability in actual use margins pass the threshold and failure rate increases
- Warranty Projection: It’s not possible to have an accurate warranty projection without being able to trust all of the above.
What is the process for creating a correct mission profile?
- Define all stresses ( forces, loads) in a nominal use case.
- Identify which will be highly variable and which are expected to stay static regardless of use.
- How many “levels” can the customer base uses profiles be divided into? Two? Three? Five?
- Test the product in field usage and/or simulations
- Characterize these results in the use case levels
What is the process for creating a correct environmental profile?
- Define what are important environmental factors for the product (UV, heat, humidity, water submersion?)
- Categorize anticipated environments by level (Mild, Nominal, Harsh)
- List the stress to failure mode relationships for the environmental based stresses?
With this level of resolution on environmental and use stress any of the listed exercises listed above (DFMEA, ALT, Warranty Projection) will have an established foundation to be created upon. This assists with ensuring that the outputs of these activities stay relevant to the program throughout all phases.
Take the time to define “Use Case” and “Environmental Conditions” with the development team early in the program. It is part of your program foundation, ensuring planned activities have maximum influence on creating a reliable design.
-Adam
Very good summary of the subject. Mission profile is so obviously needed that it sometimes gets difficult to explain why it is needed but I think you made a good job on that.
Thanks Bo, much appreciate he kind words. cheers, Fred
Thanks Bo,
It always surprises me how teams do not invest in this. The gains in having this established vs the small investmetn to create it is so clear.
Regards,
Adm
Hi,
we are currently working on an international standard for a mission profile data format.
Please feel free to check http://www.mpfo.org.
Regards,
Goeran
What is happening in the field of mission profiles lately?
The MPFo effort seems not so active and the question on what and how to share this type of information in the supply chain is not very clear.
I have not seen much about the use of advanced time series analysis to explore the different contributions for analysis of sensor data. I assume the later is a part of PHM work but should be useful also for traditional reliability estimations. Any input on what is going on?
From the failure mechanism side the damage accumulation models are still a problem and risk assessment is very uncertain in many cases forcing the use of margins instead of probability for failure. This is maybe a too complex issue for some short texts but it could be of interest to bring up some general progress.
Regards
Bo
Hi Bo,
Good comment/question.
Overall, not much is happening with our collective understanding of mission profiles.
The increased availability of sensors and remote telemetrics in some products and markets, yet it has been a long struggle with ROI – how much better do we need to understand the environment and use?
Plants and facility equipment has long been using condition-based maintenance – yet, that tends to focus on indicators for specific failure mechanisms. Other than engine hours or cycle counts little is typically gathered about temperature, pressures, etc.
PoF models do require good information about environment and use conditions, in many cases, yet they also focus on specific failure mechanisms.
On the other side of this work are the various standard bodies. Most are only setting a low commonly agreed upon value… For example, 10 random drops from 1 meter for a handheld unit. With a little work we have access to weather data by the hour for free from NOAA.
Use profiles for a specific product is much harder to get good data. Some organizations enlist customers and gather data on use rates, conditions, etc. Yet, as you might expect that is expensive.
The very hard part of all of this is the changing nature of how we use our products – as we become familiar and reliant on our tools, we expect more from them in harsher conditions.
The final element is this data, if collected, is held private – trade secret type info.
Not much of an answer, yet just my view.
cheers,
Fred