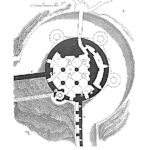
We can learn more from our failures than we can from our successes. This isn’t just a good rule for us to live by personally but is applicable to the products that we design and manufacture. In my experience, the all-important step that is short-changed in “learning from our failures” is “learning”—not just getting to the root cause in order to solve the problem but to understanding the gaps that exist in our current design and manufacturing requirements and practices that allowed the failure to spill into the field. Identifying these gaps is the key to future failure prevention. In this installment, I’m going to highlight how Weibull Analysis (a reliability tool when used in the time domain) of module field failures can be used to identify the holes in our design or manufacturing requirements or processes.
The first step toward this analysis is to break your system into modules and look at the Weibull associated with each of those modules. Of three key Weibull metrics that I use to understand these failures, the one I’ll highlight use in this article is the Weibull slope. By looking at the Weibull slope of the failures for a given module, we can know, in a general sense, where the hole originated. Sorting the modules by their Weibull slope, with the module with the lowest slope on the left and the module with the highest slope on the right we can get an overview of where we should put our focus for each module that makes up our system. The following is an example of what I’m talking about for a system of 24 modules (A through X):
Note that when sorted in this way, the modules are sorted according to the bathtub curve where those modules on the left are failing due to infant mortality issues, those in the middle are failing randomly and those on the right are failing due to wear out issues. From this view, a team can see where the gaps exist in their design and manufacturing practices and where to focus their efforts for each module:
Modules S through B: gaps exist in the manufacturing processes
Modules M through Q: gaps exist in stress-related design requirements
Modules G, E and O: The gaps exist in cyclical stress-related design requirements
Modules J and D: Gaps in exist in reliability-related requirements or life testing (either reliability or Real World Usage Profile (RWUP) requirements or Life Testing to the reliability and RWUP requirements).
Module C: This was a major life testing miss in that the life test either didn’t represent the real-world usage profile or a key failure mode wasn’t monitored during life testing.
This is somewhat a simplistic breakdown of the modules as it doesn’t take into account the effect of multiple failure modes. But, at a high level, it gives the team a starting point of where to look for the causes of these failure modes.
In my next article in this series, I’ll show how a team can use the P Diagram (a traditional Robustness tool) to drill down toward getting to more specific actions toward filling their design, development, and manufacturing gaps for each of these modules.
Leave a Reply