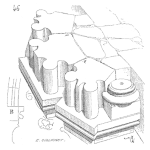
Many of you may be surprised to learn that Reliability Centered Maintenance (RCM) was actually developed with cost cutting in mind! Aircraft maintenance costs were huge. For example the Douglas DC-8-32 aircraft (a four engine narrow body jet liner built from 1958 to 1967 that carried 150 passengers) required upwards of 4,000,000 man hours of maintenance work for only 20,000 hours of flying time! That’s 200 maintenance hours per operational revenue earning hour. With growing demand for air travel in those years, wide bodied aircraft were being designed (B747, DC-10 and L-1011). But air travel was prohibitively expensive. That limits the size of the market and growth potential. A solution was needed.
A succession of methodical approaches to designing maintenance programs were introduced. In the mid-60’s MSG-1 was developed and first applied on the B-747. In about 1970, MSG-2 (an improvement on MSG-1) was applied to the DC-10 and L-1011. In the late 1970’s Nowlan and Heap’s report, “Reliability-centered Maintenance” is published – it was the first time the name was used. It led to MSG-3, published in 1980 (later revised in 1988 and 1993). The use of decision diagrams to develop maintenance programs led to an incredible improvement in safety. Crashes dropped from over 60 crashes per million take-offs, to less than 2 per million by 1990. That improvement is often credit to RCM, but strictly speaking RCM didn’t come along until that rate was already down to about 5 per million. However, the use of scientifically designed decision logic, can take the credit. Today that method is RCM and rates have dropped even further.
Nowlan and Heap’s RCM also spawned development of Mil Std 2173 (1986 – for naval aircraft and weapon systems) and the experimental application of RCM at two nuclear power plants by the Electric Power Research Institute (EPRI) in 1982. By 1986 EPRI standardized on RCM for its nuclear power plants and contractors applied it, turning it into a commercial product. Given the high cost of maintaining nuclear plants, EPRI’s focus was on cost reduction without reducing reliability and safety. Improving reliability and safety were not the objective at that time, and financial returns on the efforts were somewhat disappointing. In those days, no one was really considering protective devices and dealing with hidden failures. By the early 1990’s RCM was becoming known and commercial variants began to appear. The first books on RCM were published, John Moubray’s RCM II in 1991 and Anthony M Smith’s book in 1993. Both authors began businesses to bring RCM to industry and others quickly popped up as competitors. By 1993, Moubray began introducing the concepts of risk into task interval setting, US NavAir RCM Guide (403) was published and in 1994 the Royal Navy introduced NES45 (their standard for RCM). By then, RCM had developed a reputation for being an expensive resource intensive method to us, so a number of commercial variants arose to “streamline” the method and reduce its costs. Given confusion in the market about what RCM really meant and a desire on the part of the US DoD to reduce procurement costs, SAE standard JA-1011 was published in 1998. That eliminated the need for US military standards and gave procurement professionals a standard for comparison of what had become a confusing array of RCM methods on the market.
Today, RCM does require a team-based approach for best results. Responsible proponents link application of RCM to asset criticality analysis results and recommend it only for your most critical assets. With proper facilitation it can be done just as fast as some of the less rigorous methods that still exist today and the team composition can be kept only to those really needed. It does NOT require software tools to be implemented effectively, although they can be helpful. The costs of software for RCM add to the cost of using the methodology. I’ve used paper based approaches, several of those software tools and spreadsheets. Paper is a night-mare to maintain so I don’t recommend it. Some of the software is quite good, but I find spreadsheets to be more than sufficient.
Keeping your analysis fresh with changes in your operating context will always be a challenge and I see no advantage arising from any of the various software options. Those revisions occur infrequently and the expertise to use a dedicate software product must be relearned each time. So long as the individual knows the RCM method and can find her way around a spreadsheet, they are quite easy to update. What’s important is the context and its impact on the analysis, not the tool itself.
Today’s enhancements to RCM come in the form of integration with International Standards and application of reliability analysis within the RCM context. RCM-R® is perhaps the best example today.
RCM does remain somewhat labor and thought intensive. It takes time. On average, with experience, it will consume one hour of effort for every 4 to 6 failure modes. To put that in perspective, analysis of a complete diesel engine with all built-in sub-systems (fuel, lube, air, exhaust and mechanical output drive) will take about 2 weeks. Analysis of a cooling system for a plant (including suction, pumping, cooling, distribution and cold-weather provisions) at the design stage can take just a few days. My experience with RCM is that it will require the equivalent of about 2 % of capital investment to carry it out effectively. Leveraging it into maintenance planning and provisioning of spares, training, etc. will double that. Is it worth it?
Consider the benefits. One electric utility I worked with reduced maintenance costs by an average of 22% (annually) when compared with the use of manufacturer recommended maintenance. They also eliminated many “infant mortality” failures by shifting from a predominance of preventive to condition based maintenance. The program paid for itself within months of its initiation from savings produced in pilot studies alone.
In mining environments, which often tend to be reactive to failures, maintenance costs can be reduced by even more, while reliability and output levels (production) are increased. In a recent case we demonstrated a $97 million per year cost savings across 6 mines. The resultant maintenance program, if executed well and on schedule, would also increase mine output dramatically. Estimates of the value of increased production in that case were just shy of $1 billion annually! The program costs to deliver that (including RCM and other maintenance practice improvements) were in the range of $10 million over a 3 year period. ROI was huge!
If you consider only the costs of RCM, it might be seen as expensive to an uninformed cost accountant. To a finance manager considering the value generated, it is a bargain with huge payoff and it can far outstrip the returns made from far larger (albeit more sexy) capital projects.
Leave a Reply