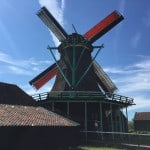
The original windmills of Europe are feats of engineering. I was able to get inside of a few in Holland and see all the mechanisms that have been operating for hundreds of years. I was lucky that the wind was strong and the windmills had their sails out the days I was visiting. A few were grinding flax seed and others designed to pump water from a low basin to a high basin to control basin water levels. Being inside of the windmill was like being an insect inside of a grandfather clock. It was so interesting seeing how they engineered the mechanisms to optimize the balance of the system needs in such a different manner than we do with many of our currently engineered products.
But one thing caught my attention in particular, there was a wood working shop on site for the ones that pumped water to the basins (remote). I looked at the shop in detail and tried to see what was considered regarding it’s functionality.
In current product development we work hard to get maintenance out of the product life cycle. Car engine oil used to be changed at 3k miles now it’s 12k miles; spark plugs used to be 4k miles now they are 100k miles. Television and vacuum repair shops don’t even exist any longer.
The windmills were designed with maintenance and uptime as the key feature. Components were clearly in one of two categories; “last forever” or “consumables”.
There was no in-between. The consumables were designed to be easily fabricated on site and quick to replace. The “last forever” ones were still original on the day I visited and going strong, so about 400 years. One example is the vertical drive shaft that runs the entire length of the structure was original in all of the windmills that I saw. (I asked of course). Bearing wear was designed to not be the cast iron bearings but the wood raceways.
The consumable parts were all made of the same kind of wood, easily removable and easily carried by one person. As I mentioned they had wood working shops within a short walking distance that were stocked with wood, tools, and drawings.
I would say that the order of priority of product factors when the windmill was created was something along the lines of
- Robustness: It had to be able to take storm strength winds on the structure as well as the veins, take lighting strikes, rodent, insect, small animal damage, seasonal weathering.
- Maintenance: Items had to be either designed to be permanent or consumable. The consumable ones have to be easily accessed and fabricated in the on-site wood shop.
- Efficiency: When you are counting on these windmills for necessities like making sure fields that are under sea level stay dry, or processing staple foods, or oil for fuel, you need to extract every last bit of energy from a fickle source like the wind. The “necessity” term for these windmills is not used lightly. 40% of the country of Holland is reclaimed land that was under sea level and marsh or lakes/bays. They created 12,000 windmills for this task of controlling the water levels.
- Functionality: As the windmill technology progressed they added more features, swivel tops to aim the blades into the wind, interchangeable parts to diversify functionality, rotating grinding wheel but can switch to cam operated pressing hammers.
A product we design today is so rarely developed around the same order of product priorities. Many of our products follow an order of:
- Functionality: Has to have every possible integration of new technology in it or it won’t sell.
- Efficiency: Must be able to use remote power sources or comply with energy standards. Not to mention everyone wants a green leaf or sunshine sticker on their product so consumes don’t feel bad about buying a new product even though they have a perfectly good one at home.
- Robustness: No one wants a quitter and it’s not acceptable anymore because there are competitors at the same cost point that can satisfy this.
- Maintenance: Ehh whatever I’ll throw it out before we get that far.
But there is a notable exception. It was the inaccessibility of some of the windmills that drove the general design for maintainability that they all carried. After leaving the windmills an article I read back in 2014 came to mind. NASA did a test to see if they could design a tool in CAD, email it to the space station, have them print it out on a 3D printer on-board, and then use the tool. Seemed to run in parallel with the system of having the drawings sitting on the work bench next to the wood and hand tools by the windmills.
When we first started space travel we only went short distances for short periods of time. But now we are striving to go long distances for very long periods of time. We are working out the details of how to do long distance with our current rover expeditions and long duration with certain exercises on the International Space Station (ISS).
With space travel having an inventory of components is not easy due to limited storage and weight requirements. With the limited opportunity for delivery of supplies this becomes a big factor for maintenance. With 3D printing you can have a raw material on board, plastic or composite spool, a method for shaping it, 3D printing, and CAD models. There I now an infinite inventory of spare parts and custom tools as long as you have spools of material.
- Plastic Spool = Wood
- 3D printer = lathe, chisels, hammers
- paper drawings = CAD model
Looks like that design factor priority list for windmills up above may be similar to one found in a product plan at a modern day aerospace company.
This is the original article on the 3D tool printed on the ISS. Very interesting.
-Adam
Leave a Reply