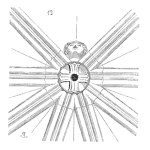
According to the US Bureau of Labor Statistics data released in December of 2020, 5,333 Americans died on the job in 2019. While 40% of these deaths were cause by transportation incidents and 15% were attributed to workplace violence, nearly 2400 on the job deaths were a direct result of one of the following causes;
· Falls, trips or slips
· Contact with objects or equipment
· Exposure to harmful substances or environment
· Fire or explosion
What the Bureau of Labor Statistics leaves out are the deaths that occurred where employees had come forward to warn of a potential incident.
In performing Reliability Centered Maintenance (RCM) analyses over the last twenty-five years, I’ve always tried to build trust with the team members to ensure that in assessing potential failure modes we covered the failure modes that could lead to injury or death. In completing the analysis and moving into the implementation phase I have always strongly advised plant management to ensure that every task that had the potential to impact employee health, safety and environment gets both implemented and executed at the recommended interval.
In making that recommendation I explain to the managers that in order to get the best result from the RCM process, we require that the team be open and honest when it comes to not only what has happened at their plant but what could happen. In doing so we often uncover hazards that currently exist and require immediate attention. While rectifying these is an easy decision, they have also identified other potential failures that should receive the same attention. I then wrap up the discussion with the following; “I want to make it clear that in identifying potential heath, safety and environmental incidents, your company now has documented evidence that you are aware of the potential. If you fail to implement the recommended tasks or address the potential failure, you as a managers now become negligent should a failure occur. I therefor strongly recommend you take immediate action on these items. Please, do not put the safety of your employees, the reputation of your company and the wellbeing of your family and career at risk.”
In truth, nearly all workplace deaths are preventable. In Gainesville, Georgia this week, 6 workers died on the job and several others required immediate medical attention for a failure that was both detectable and preventable had the plant been performing routine ultrasound leak detection routs. While we all wait for OSHA to investigate and report on this tragic event, If reports that employees had reported the leaks previous to incident are correct, what happened at this plant wasn’t an accident.
So, while 6 families grieve, no excuse, no explanation and no financial settlement will ever change the fact this this incident should never have occurred. In closing, the best way to ensure that your employees all return home safely is to create an environment where safety really is the highest priority.
Douglas Plucknette is the President of Reliability Solutions Inc. and the creator of RCM Blitz™
Leave a Reply