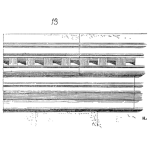
Overview the Plant Wellness Way EAM Methodology for a simple and successful Enterprise Asset Management System. Learn how to apply the Plant and Equipment Wellness enterprise asset management methodology. Follow the steps to get the best performance from your plant and equipment. Learn what systems and processes produce the optimal plant and equipment reliability results. From creating low stress component environment for lasting equipment health through to establishing the simplest and most effective business system and processes for world class asset management performance, this overview guide to the Plant Wellness Way takes you step by step in creating the outstanding asset performance needed for world class operational excellence. As with human wellness, the Plant Wellness Way requires you to build a healthy life for your machines. Learn to control your plant’s reliability by managing the stresses put on equipment parts and reducing the risk of failure so plant and equipment remains fit and healthy to produce its best performance. The Plant Wellness Way EAM methodology lets you find the ideal health conditions for your equipment and machines and makes you establish business processes and systems to achieve and maintain outstanding reliability performance.
Keywords: operational excellence, enterprise asset management, maintenance management, plant wellness
Plant Wellness Way EAM System-of-Reliability is a fully integrated life cycle asset management methodology. Its processes identify and install the optimal asset maintenance system and work quality practices into your company to minimise operational risk and gain operational excellence. Figure 1 is the Plant Wellness Triangle for asset management excellence, is shows you how to create and sustain highly reliable plant and equipment.
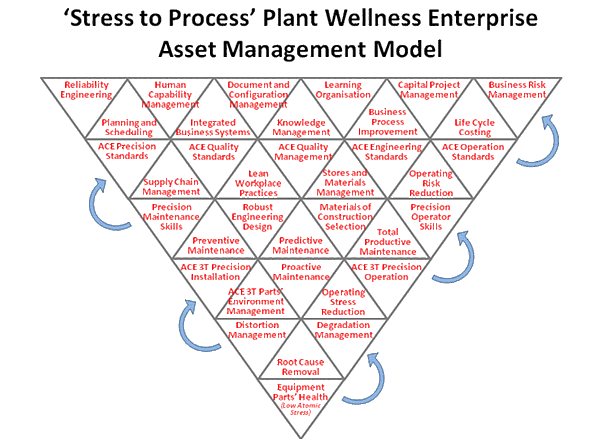
Figure 1 Contents and Processes of a Plant Wellness Way Asset Management and Maintenance System
Great operational asset performance is a vital component for operational excellence. An ideal asset management system is perfectly structured to produce world class asset management results. An optimal asset maintenance system uses the least resources to produce world class operational equipment reliability. The Plant Wellness Way encompasses the full life cycle requirements for least cost, long-lived, lasting physical asset health. Like human wellness, Plant Wellness focuses on living a life of maximum health and vitality, continuous fitness and wellbeing, and failure-free longevity.
Summary of the Plant Wellness Way EAM Methodology
Table 1 collects together the contents of the Plant Wellness Way EAM method. It shows you the steps to take to apply the methodology so that you can produce outstanding reliable equipment for operational excellence.
Table 1 Summary of the Plant Wellness Way EAM Method
Plant Wellness Way is a scientifically based, business risk prevention technique used by shopfloor maintainers through to degree qualified manager. It is a universal asset management process that is simple in concept, correct in method, easy to apply, yet thorough and complete in its outputs. The methodology is based on sound business risk management strategy and successful reliability improvement science. It gets you and your people thinking correctly about failure prevention and shows you the right answers to adopt to create high equipment reliability and minimise life cycle operational costs.
This article explains how to use the Plant Wellness method. You follow a step-by-step process that starts with how big the breakdown and failure risks are in your operation, then determines the simplest and most effective ways to remove and prevent those risks and ends up with showing you how to create the optimal business processes to deliver a powerful wellness and health strategy for high equipment reliability.
1. Determine Equipment Criticality and Resulting Operational Risk
First an Equipment Criticality Analysis is done to identify the equipment where your operational risks are located to allow you to focus operational and maintenance efforts on where they pay-off the greatest for the business. Chart 1 is used with a company’s risk matrix to determine each physical asset’s criticality. Equipment by equipment, from the power supply into the operation through to each physical item of plant, gets rated for its criticality, i.e. the operating risk it brings to the business.
Chart 1 Assess Every Plant Item’s Criticality
This assessment identifies how bad things can get in your operation if any of your operational equipment fails. The top of the chart is for situations where you never want a failure event to happen. Deaths, law breaking, environmental disasters, business destroying losses are failures you never want to face. The probability of such a failure event occurring is not a concern. These types of events must never happen because the consequences would be too severe and disastrous.
Where the effect of a failure event is a production impact, then the lower portion of the chart is used to apply probability of the event occurring through use of a risk matrix during the risk assessment. The risk analysis and risk prevention tools used in the Plant Wellness Way (PWW) will get you to select risk controls and mitigations that drive your operational risk to low and lesser levels. At the completion of Step 1 you have a list starting with the most critical plant and equipment and going down to the least critical
2. Determine Assembly and Parts’ Criticality and Resulting Operational Risk
This step looks at the assemblies and parts in each item of equipment to identify which are the critical components that cause bad risk when they fail. An item of plant or equipment item only causes operational risk if critical components breakdown, stop working or lose integrity. The critical parts are now identified so appropriate risk management strategies, including operational and maintenance activities, can be selected.
The same risk assessment chart used to identify equipment criticality is used to identify component criticality. The one difference is that in Chart 2 we start with an assembly or component. In the review each part in a machine and every section of pipe, flange and valve is risk analysed. It was a failed pressure relief valve (PRV) on a section of pipe that caused the Three Mile Island nuclear power plant disaster, and a PRV was involved in the Piper Alpha off-shore platform fire, so you must look at every physical item in your operation and identify the worst case events that could happen should it fail.
Chart 2 Assess Every Equipment Component’s Criticality
3. Identify Component Failure Categories
Because parts fail before the equipment fails, the Plant Wellness Way requires you to prevent critical part’s failure. From Step Two you know the critical parts in all your machines and items of plant. Now we need to understand how each critical part can fail—what situations can cause a part to fail and make the equipment breakdown, stop operating properly or lose integrity.
PWW focuses on using proactive failure prevention strategies instead of failure detection and repair. We are not interested in using the normal asset management practice of Reliability Centre Maintenance (RCM) where you identify the many failure causes and their resulting failure modes for each item of plant. Instead we want to understand the type of situations that will lead to equipment failures and control the situational causes so that no failures will arise that we then have to fix. By preventing failure causes starting Plant Wellness saves companies vast amounts of money.
For each equipment item its parts drawing, such as the one in Figure 2 for a V8 motor, and parts list, Figure 3 for the V8 Motor, is used to identify the critical assemblies and components. Using the parts list each part is categorised by the situations that can cause it to fail. Equipment components fail for one of two causes—they become degraded by use or they are over-stressed by deformation. Deformation is the result of a stress creating incident and human error. Degradation occurs through wear-and-tear and accumulating contamination. In Step 3 the parts that degrade from use and wear are identified, as are parts that fail from deformation through excess stress. Usually equipment parts fail multiple ways.
Figure 2 Equipment Parts Drawing
As shown on Chart 3, part by part is reviewed to see which situational causes lead to their failure. The explanation box in Figure 3 shows how they are categorised by those circumstances that produce degradation and those that produce deformation.
Chart 3 Identify Situations that Cause Critical Parts Fail
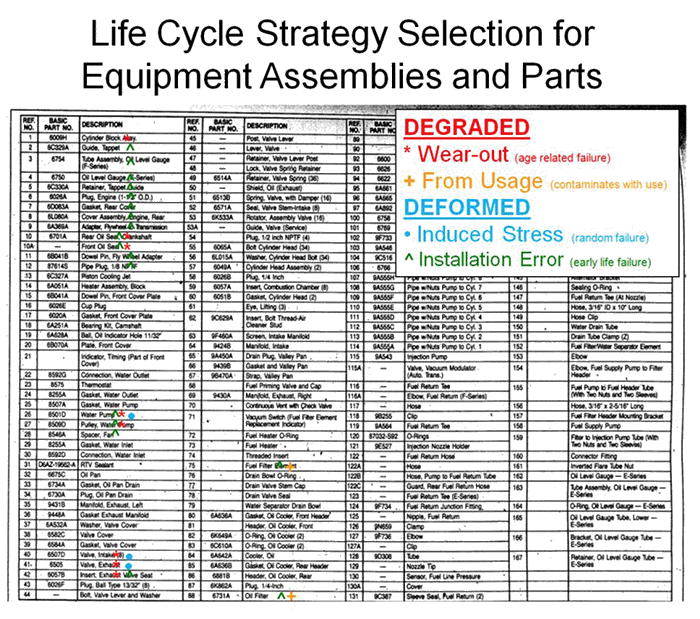
Figure 3 Equipment Parts List Showing Parts Situational Failure Causes
At the end of Step 3 the critical parts are identified and the situational causes of their failure are known.
4. Identify and Select Component Life Cycle Wellness Requirements
Plant Wellness is a life cycle asset management philosophy that proactively prevents the causes of failure starting. It requires that you put into place in your business the strategies, methods and practices which create highly reliable plant and machinery. Prevent and control the situations that can cause bad risks and problems to parts and you stop operational failures.
To maximise operational profits we must prevent operational risks occurring. You need to find and implement the specific actions that produce the required health outcomes which prevent critical parts failing. Loss can only happen if first a bad risk is present that can lead to the failure of an equipment’s critical parts. If you prevent the start of a bad risk you kill the failure cause and effect tree by removing the root causes of failure. Stop opportunity for a failure to start you get reliability.
The PWW gets you to choose risk removal and mitigation activities for each phase of a critical component’s life cycle to greatly reduce the opportunity of error and defects arising during its lifetime. By preventing operational risks at every stage of a component’s life you stop the defects and errors that will later become operational equipment failures.
Chart 4 helps you to target the sort of practical techniques and deeds that create machinery and equipment health and plant-wide wellness in your operation. When you stop critical parts failing your equipment becomes outstandingly reliable. Chart 4 is used to select the types of life cycle activities on which to focus that will prevent equipment failure.
Chart 4 Selecting Part’s Failure Prevention Life Cycle Strategies
For each critical part, the trigger risks listed at the bottom of Chart 4 are used to review the part and identify if it can be failed from any of the risk factors. Activities are then identified to address the part’s local environment, operational stresses and life cycle risks to remove or at least greatly reduce the risk factor. The power of Plant Wellness is its recognition that there are only a few fundamental causes of failure and by controlling them you can get any level of plant and equipment reliability that you want. Unlike other asset management methodologies that look for evidence of failure and then fix the failure, PWW instead gets you to recognise the situations that produce outstanding reliability and create them in your business.
5. Categorise Risk and Failure Prevention Strategies
PWW requires you to put the risk mitigation actions into appropriate engineering, operational and maintenance processes to ensure that they happen correctly. Knowing how the critical parts will be protected from failure allows you to identify guiding project engineering, operational and maintenance strategies to prevent their failure. Chart 5 is used to categorise the life cycle failure prevention activities into the applicable strategies that prevent and control the situational circumstances that lead to a critical part’s failure.
Parts that fail from induced stress require strategies that remove and prevent over-stress circumstances developing. Parts that fail from installation error need their installation process to be carefully controlled. Parts that fail from contamination require strategies to prevent or remove contamination. Those parts that degrade by wear need strategies to reduce degradation and ensure that they are replaced before they fail.
Notice that we have started at the bottom of the Plant Wellness Triangle—with the parts. By delivering the right strategies for your parts you get outstanding equipment reliability. Once the right pre-emptive risk activities are selected the PWW methodology will take you up the ‘stress to business process’ triangle and show you the business processes to build in order to surely deliver the right life cycle asset management strategies to your equipment and machinery for lifetime reliability.
6. Identify and Select Component Health and Wellness Standards
We have so far selected engineering, operational and maintenance risk management strategies and activities to prevent defects and errors during each critical components’ life cycle phases. Next you need to set the performance standards for each activity that, when the standard is achieved, will deliver long, highly reliable component life. With long, failure-free component life comes long, trouble-free equipment life and you get the high plant availability that you want.
These standards are the precision workmanship and quality control standards that need to be met throughout the life cycle by your consultants, vendors, suppliers, contractors and your own engineering, operations and maintenance people. In setting and providing quality standards you place minimum acceptance criteria on equipment performance and work quality outcomes so that a known degree of reliability is achieved. When a higher level of reliability is wanted we make the quality standards more demanding and develop the methods to achieve them with certainty.
Some of the suggested precision machinery health standards are noted in Table 2.
7. Identify Engineering, Operational and Maintenance Actions to Apply
You next identify ownership for each risk mitigation activity and action. You make clear where the responsibility and accountability lays for the performance of each activity. Chart 5 identifies the applicable business and risk management processes that an activity will belong to. The selected strategies, methods, activities and standards are written into the applicable company processes by including them in the relevant business process documentation. Policies, procedures, work instructions and training are updated to include the activities that need to be performed and the standards that need to be achieved.
You start by documenting the correct way equipment reliability is achieved and then you train your people to do the right activities rightly. We first educate people in the right practices and then teach them to correctly use the right practices. The Plant Wellness Way is written into your processes and inculcated into the operation, and thereby it is forevermore made part your organisation’s cultural DNA.
Chart 5 Selecting Applicable Business Processes for the Failure Prevention Strategies
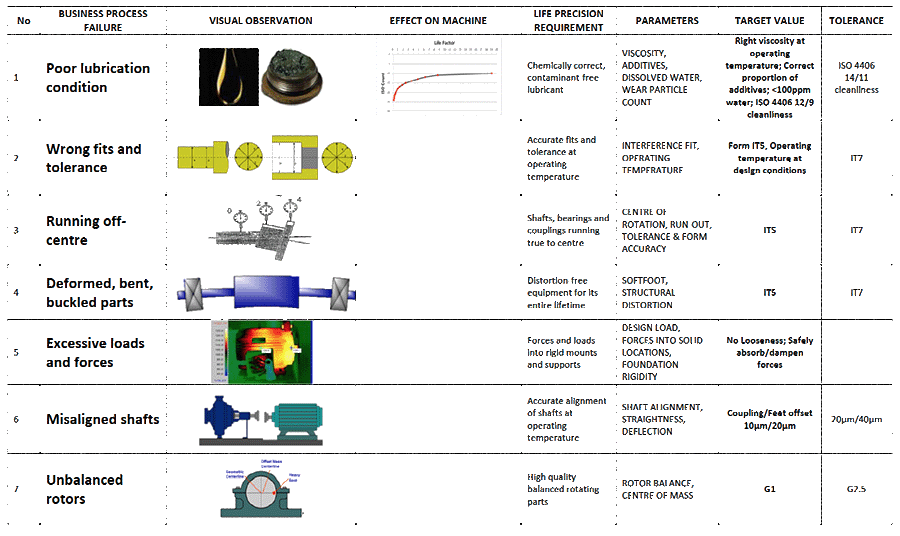
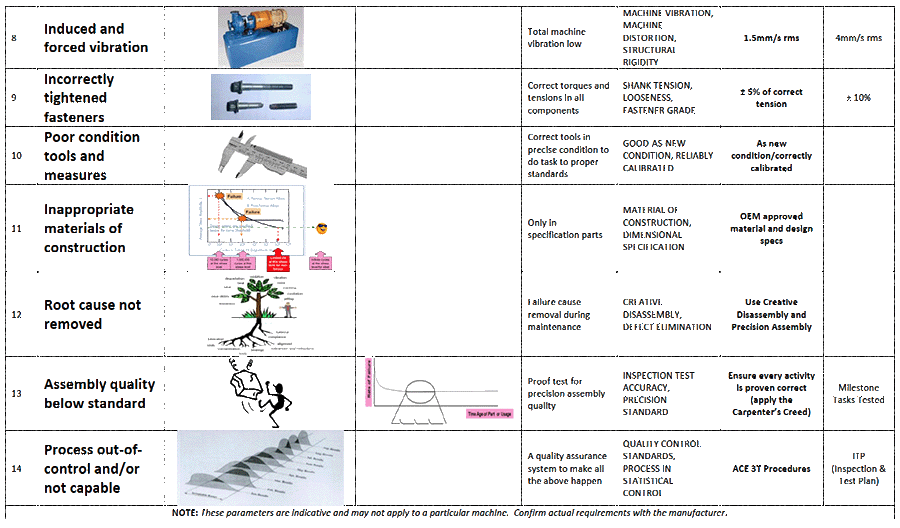
Table 2 Indicative Target Values for Creating High Machine Reliability
8. Identify Spares and Supply Chain Management Strategies
Some of the actions and activities in the various risk management strategies used will require that parts and material be available to minimise business and operational risks. The supply chain management, purchasing and materials management practices that make those items available at the appropriate times need to be identified and put into place. Which parts and materials are needed on-hand or which can be brought are identified with the help of Chart 6, which is Chart 1 modified to consider spare parts criticality.
Chart 6 Assess Spare Part Criticality
Like any risk based decision, which parts to carry, which parts to purchase-on-demand and the integrity of the business processes that support the supply chain and materials management practices are dependent on the risk a company is willing to carry.
9. Confirm Equipment Risk Reduction is Below the Risk Boundary and Industry ALARP
The PWW methodology requires that the risk mitigations selected must drive the operational risk for an asset to below the Corporate Low risk level, and if necessary down to the industry’s As Low As Reasonably Practicable (ALARP) level.
It is easy to select risk management activities and create a lot of work for operators and maintainers. Just because a mitigation can be imagined and performed it does not mean that operational risk is reduced by doing the activity. When risk mitigations are chosen they must surely, without question, reduce risk—either by reducing the loss from the failure event and/or by reducing the frequency of the failure event. Plant Wellness requires indisputable evidence that the failure rate of a critical part is substantially reduced by doing the mitigation activity. Consequence reduction alone is not enough; there must be clear frequency reduction visible on the risk matrix. Only frequency reduction means real reliability improvement.
Figure 5 Not All Maintenance Work Actually Reduces Risk
The quantum of moneys saved is determined by using a spreadsheet in which each mitigation’s consequence reduction and frequency reduction financial benefits are tabulated and tallied.
11. Develop Planned Maintenance Work Orders to Deliver and Track Activities
The selected risk mitigations must be done to prevent opportunity of a bad event to arise and develop, and to limit the consequence of a bad event. It is only by doing the mitigations that risk is contained. It is necessary to ensure that all mitigations are done, traceable and their proper actioning is recorded. The risk management activities selected to be done by Operations and Maintenance are put into the Computerised Maintenance Management System. Each activity is planned thoroughly and in detail so that a work pack with all necessary information, parts, materials and actions to be taken and recorded is available for each job when it is done.
Those operational risk mitigations that belong to Capital Projects, Engineering and other departments are written into the applicable process documents. Where mitigations are time based in those departments the mitigations are initiated through an automatic system so they are not forgotten. For situational based mitigations applicable procedures will generate needed actions and management activities will track them.
An annual audit reviewing risk management and mitigation is undertaken to ensure the necessary risk control activities and actions are being performed by all parties. As part of weekly, monthly and annual reporting the performance and success of risk mitigations are measured and reported to senior management.
12. Develop the Business Quality Management System Needed to Support Plant Wellness
We are now at the top of the Plant Wellness Way Triangle in the region related to the business systems and processes needed to sustain the equipment health that delivers Plant Wellness at the corporate level.
The previous steps in the PWW methodology produce the risk control activities and risk mitigation actions that greatly reduce operational risks. Across the life cycle of every asset we identify what to do to get outstanding equipment reliability. It is now necessary to ensure that all these risk reduction activities and lifetime reliability deeds are done, and always will be done, by the organisation.
Chart 7 shows a business quality management system and the Plant Wellness processes needed to reduce operational risk and reach high equipment reliability. The processes shown are used to produce the asset management performance required to get operational excellence. The top row of processes are the ‘working’ processes—those whose outputs deliver lifetime reliability. The bottom row of processes are those that sustain Plant Wellness. The aim is to have small the smallest business processes while ensuring each process achieves, nourishes and maintains everlasting Plant and Equipment Wellness in your company.
13. Continually Improve the Company’s Use of Plant Wellness Strategy and Activities
Figure 7 shows the self-improvement model used by learning organisations to push themselves to the forefront of performance. It is a powerful tactic for improving equipment reliability and getting Plant Wellness asset management success. It asks you to test new ideas and approaches purposefully seeking improvement and to adopt changes that bring you benefits. Introducing Lean principles and practices into your organisation and using them properly fits the model and provides you with pacesetter rewards.
The success of a company depends on the usefulness of its products and services and its ability to deliver better products for less cost using fewer resources. This requires new cost reduction practices and innovations that generate an advantage. The simplest way to become a learning organisation that continually improves itself is to adopt the practices and methodologies of LEAN throughout the business. From Boardroom to shopfloor introduce and master the Lean processes and practices that create efficiency to reduce costs and those that drive creativity and change to improve the business.
Figure 7 Becoming a Learning Organisation
Chart 7 The Supporting Business Management System and Its Processes Needed to Reach and Sustain Plant and Equipment Wellness
Leave a Reply