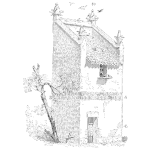
A product or system may fail for many different reasons.
One cause is a faulty part. A component is susceptible to failure when either improperly used in the design or is a damaged or flawed component.
The selection of parts is an essential process of design for reliability accomplished by the designing engineer.
The bulk of part selection work is done during the concept/planning phase of the product lifecycle. Of course, some parts are selected later in the development phase or later, yet the same selection process should still apply. The process provides a balance between functionality, cost, manufacturability, and reliability.
Depending on your specific product, technology, and market, other part selection considerations may apply.
Purpose of a Part Selection Process
According to RBPR-3 Designing for Reliability. (1996. Blueprints for Product Reliability. Rome, NY: Reliability Analysis Center), section 3.8 Part Selection the purpose of this design for reliability task
is to select parts for a product that will enable a design to meet customer reliability needs, and to control parts to ensure that the inherent reliability design of the product will not be compromised.
There are a couple elements to a part selection process:
- Establishment of a preferred parts list (often called an approved vendor list)
- Management of a parts control program to encourage reuse of existing parts and limit use of new parts
- Conduct of a new part/vendor evaluation program to fully consider all elements of long-term supply chain relationships
The overall intent is to select and use components within a design that will be available and function well over the expected use of the product.
Potential problems with a poor Part Selection Process
Without a proactive and systematic parts selection process the risks to the project include:
- Part cost increase risks
- Part unavailability risks
- Part incompatibility risks
- Part unknown failure mechanism risks
The actual part cost is a function of supply and demand, the component technology and materials, along with being a profitable part to sell in the marketplace.
The ability of the supplier to create the component is a consideration when selecting a part. Is the supplier able to successfully (profitably) control costs, part quality, and do so for the foreseeable future?
Cost risk
Selecting a part not already on the preferred parts list may also incur the additional burden of part/vendor evaluation.
Plus, it will increase inventory costs as another part number enters the system along with any shipping, inspection, warehousing and inventory costs. Some parts require special handling during transport, storage, and during product assembly processes, thus increasing the effective cost of the selected part.
Availability risk
Part availability means the selected part for a specific design physically exists when needed for product assembly.
Specifying a part that has long lead times or short shelf life may limit availability. Another factor is parts have a lifecycle, and selecting a part about to become obsolete or discontinued from a supplier, further limits or ends availability.
A preference of many supply chain managers is the selection of parts that are available from two or more suppliers. While there are benefits to working with a sole supplier it does increase the risk of unavailable if the supplier goes out of business or loses production capability for any reason. It also reduces the market pressure to limit costs or improve the quality of a part over time.
Incompatibility risk
The parts selected should work not only for the functional requirements of the design, they must also work with the product assembly and maintenance processes.
The parts should not by their presence in the product damage other parts (off-gassing, electromagnetic radiation, etc.). Likewise, a selected part should not require unique or expensive handling or assembly techniques to add to existing manufacturing, transport, or storage systems unless the specific benefits outweigh the associated costs and complications.
Unknown failure risk
Unique or non-standard parts generally increase assembly errors due to the lack of familiarity with the part characteristics.
Plus, non-standard parts limit or significantly increase complexity and cost of assembly automation processes.
Part Selection impact on reliability
The best way to know a part works with a product when in use with customers is to monitor field failure causes.
Unfortunately, this is a risky method to validate part reliability, by allowing the customer to first verify the product works. The reliability considerations during part selection work to minimize the risk of field failures.
Using standard parts with long successful field performance limits the range of reliability risks when the part is selected for a new design. We then focus on the new aspects of the design impacting the part reliability, such as increased duty cycle, increased use stress or loads, or different interactions with other components of the system.
Rather than characterizing and qualifying a new supplier or part, the focus is on the marginal differences, if any, for the new design.
A new part brings a set of risks for reliable product performance.
- Functional performance over time —degradation, wear out, drift, etc
- Environmental range —robustness to expected range of weather and use conditions
- Quality —process stability and capability of the supplier(s) over time
- Technology —what is expected to fail and when
- Supply Chain impacts —the quality and technology concerns for the supplier’s suppliers
Generally, anything new (new technology, new material, new factory, new line, new process, new technique, etc) should make reliability engineers ask more questions.
Something new is not bad in itself, it does come with increased uncertainty and risks of unanticipated field failures.
Working closely with design engineers during the part selection process allows us to identify and work to fully understand and minimize any reliability risks early in the product lifecycle.
Selecting parts is a complex process that done well (including considerations from all stakeholders) does reduce the risk to costs, assembly capability, and customer satisfaction.
Related:
Reliability in Product and Process Development (article)
Reliability as Part of Every Decision (article)
Material Selection and Reliability (article)
Dear Mr. Schenkelberg
Congratulations by your article. It has lot of details and help me so much, I a engineer from Brazil that really appreciate yours reports.
Thanks very much for share your expertises.
Hugs
Miraveti, Paulo