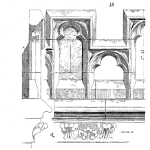
I often ask my classes ‘If we follow our procedures to the letter, do nothing more and nothing less; would we optimize our system productivity, safety and reliability?’ The answer is NO.
If anyone on this forum has ever worked in a union environment in the manufacturing world, they will attest that doing this (follow the procedure only as written) is a common negotiating tactic when it comes time to vote for deciding whether to strike or not. Why is this to their advantage, why is it an effective tactic?
Because no procedure could possibly cover every eventuality that could occur in the course of doing the task. There has to be a degree of judgment permitted and expected in any procedure, as expressed below by Wayel and concurred by others.
The gray area becomes when too much leniency is given for the ‘judgment’ portion and unsafe practices result (workarounds that deteriorate into an unsafe zone – normalization of deviance). Policing our procedures for proper implementation and obsolescence is the continuous improvement challenge.
Awareness and education about this cycle is a key to identifying when our systems are becoming deficient and eventually will be detrimental to accomplishing their purpose. A high reliability organization (HRO) would recognize this deterioration of standards and take proactive actions to implement systems to review and update our procedures and on periodic basis.
We all know that many of our procedures are written for legal purposes. We ensure that we have specific procedures in place to pass our audits and maintain compliance.
However, how confident are we that the end users of the procedures possess the knowledge and skill to apply them effectively?
How confident are we that the procedures in place are appropriate for the service they are in?
Do we adequately update our procedures for the inclusion of new technologies?
Do we ensure that the end users demonstrate the appropriate skill to apply the procedure (as opposed to just knowledge/in service)?
I agree that this is a common issue and continues to be a challenge. I’m curious about what practices other facilities have in place to control the uncertainty while empowering their employees (rather than micromanaging).
Although still not a perfect system, some practices we have in place are:
– Training matrix – employees sign off on procedures, depending on the process there are levels (ex., in-training, trained, experienced, capable of training)
– Layered Process Audit – different roles have different LPAs that review procedures from different perspectives – is the procedure accurate and up to date/does it make sense; review with an employee who executes the procedure (how familiar are they with it/check my understanding); and does it align with other documents/procedures (control plans, PFMEAs, process flows)
– Procedures contain the Why beneath each step – I like this aspect as it helps identify deviations. When you understand why you need to that step in that manner its adds to the purpose and understanding and can help with the detection when something is not normal.
Doing the annual reviews of every document is overwhelming, and often very unrealistic, we try to combat this by utilizing the entire indirect team in conducting bi-weekly reviews of a very selective subset. Makes it more manageable that people can work easily into their schedule.
The area of weakness I am still trying to come up with a strategy for is how do you empower the employees with good judgement and a keen eye, while trying to develop the employees who shall we say might be a little quicker to judgement and the result is not always ideal?