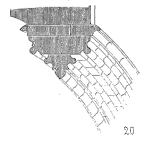
This will be the last of the series, considering the different positions in an organization that deals with product reliability. We’ve moved away from the positions where the focus on reliability is central, but there are important considerations in relation to product reliability for each of these roles still. In this concluding post the subjects are the manufacturing team, and field service and call center staffs.
Manufacturing and reliability: a rocky relationship
Manufacturing can only make a product’s quality and reliability worse. It is impossible to create a product as good as the design intent owing to material, assembly, and environmental variation. Therefore, the role of the manufacturing team is to minimize variation that adversely impacts field reliability.
Understanding the critical Q & R elements of design enables the manufacturing team to focus on monitoring and controlling elements that have a high impact on Q & R performance. The common focus on production yield is often related to field Q & R performance when the production testing includes the ability to detect latent defects or significant adverse changes to the expected product durability.
Field service and call center staff are crucial
The primary role of field service and call center organizations is to support installation, operation, and restoration of product for customers. Members of these teams must also understand the Q & R risks to better enable rapid troubleshooting and restoration for customers. The Q & R information required should not come from customer complaints; rather, it should come from product development, new product introduction, or manufacturing teams.
Another critical role played by field service and call centers is to provide early detection of field failure issues. To enhance this capability these teams should understand what is expected to fail or cause complaints, thus permitting the detection of unusual events or trends. Another role is to secure information and returned products that exhibit field failure or unusual behavior. It is often time-consuming and frustrating for the consumer to work through a detailed diagnosis and troubleshooting procedure, so replacing the product can restore the customer’s use of the product and also permit a detailed failure analysis of the faulty unit.
Setting up an aggressive replacement policy for limited periods of time, along with creating a dedicated failure analysis team to analyze returns and implement improvements, enables reliability improvements. This practice is best done at the beta testing phase or early during the product launch when the number of units in the field is limited.
Leave a Reply