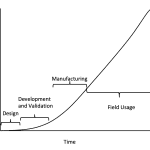
Introduction
Businesses, to be competitive, need to control all costs. Product or service failure can result in large uncontrolled costs. As product development proceeds, the cost of failures increases. The concept is shown in figure 1.
Figure 1
This story illustrates the cost of failure in the field. Years ago a company created an electronically controlled transmission. Transmissions had a high failure rate in the field. To replace a transmission, the cost was about $2,000 per repair; and to change the control module with new software, the cost was about $300 per repair. Today, the cost of reprogramming a control module is probably about $40 per repair. However, these costs could have been avoided if the transmission design and software requirements were adequately defined.
Design Phase
In the design phase, it is difficult to identify design flaws that cause form, fit, function or durability failures. One needs to rely on the expertise of engineers, programmers, and quality professionals in design reviews. Once located, the flaws are easy and relatively inexpensive to correct. Removing a flaw may require changing a part print or CAD design to redefine the part geometry. It is the flaws that are not caught that create later failures in the product cycle.
For instance, many years ago, during the review of an engine compartment layout, the design was signed off to the director level. As a new young engineer, I asked the designer what problem needed to be fixed. A path was needed past a very complex assembly of parts to rout a control cable to a carburetor. To rout the cable, the designer created a bump in an air cleaner housing. Unfortunately, the bump was located on a flat surface needed by the air cleaner. This was a no-build situation that would have been caught in development testing at significant costs. These cost were avoided by a different design.
Development and Verification
During the product development process, prototypes are created. The prototype form, fit, function, and durability are tested. When problems are detected, they can be corrected with a redesign. But the redesign needs to be verified, at some cost, to determine that the change fixed the problem and didn’t introduce any new problems.
In modern products, many functions are controlled by software. The software need to be validated to assure the product performs as intended and without any unexpected side affects. If faults are detected, then software needs to be modified.
Manufacturing and Assembly
Some part characteristics are critical for form, fit, function, or durability. Critical characteristics need to be checked for conformance to requirements. For example, a part dimension, like the diameter of a hole, may be critical for fit and must conform to part specifications. Non-critical characteristics could be the dimensions or finish of a non-contact surface. After an initial review, non-critical characteristics may not be monitored.
In an assembly operation, the there are many control opportunities. In the manufacturing of electronic components, there are complex processes that need to be controlled. In a vehicle assembly plan, there are many control opportunities. For example:
- Welding operations
- Torque guns need to be calibrated to their assembly task.
- Mounting, inflating, and balancing different size tires on a variety of wheels.
- Wheel alignment
- Many others
A choice needs to be made between 100% inspection or sampling from the process. When a part function is critical, it may be tested at the EOL. When safety/regulatory issues are involved, manufacturing is required to perform 100% inspection. Other critical characteristics are sampled for conformance.
Non-conforming parts should be scrapped or reworked. Each non-conforming part represents an investment in materials and processing costs that are lost if the part needs to be scrapped. Reworking a non-conforming part is often very expensive so scrapping is the primary option.
Sometimes the 100% part inspection provides an opportunity to sort the product into grades. The grades represent relaxed requirement levels. Consider the 100% inspection of tires, figure 2.
Figure 2
Tires were produced to very strict automobile specifications, but the process was not capable. At the EOL, tires are 100% measured for critical characteristics, like radial run-out, vertical and lateral force variation, and other characteristics. Those that conform to all requirements were directed for sale to automobile companies as original equipment. Those tires that fail the OEM specifications, but meet the next lower grade, were acceptable as replacement tires by the tire company distributor network. Others that exceed those reduced grade requirements were acceptable for tire sales. Finally, there were limits, which if exceeded, result in a scrapped tire.
Field Usage
In field usage, the cost of failure increases dramatically. Warranty costs are one of the largest single cost factors for business. A part that costs $10 to produce may cost $100 in warranty. If safety or health issues are involved, litigation costs may result in bankruptcy. It does not matter if failure is the result of a design defect, inadequate development and validation testing, or introduced by manufacturing processes that are out of control. The cost of quality (or lack of quality) will contribute to total business cost.
Conclusion
The best time to correct design errors at the minimum cost is in the product design stage. During development and verification, the costs increase, perhaps by an order of magnitude. In manufacturing, failures are probably an order of magnitude higher. In the field, warranty, regulatory, and legal costs can bankrupt a company.
This article on cost is the introduction to future articles that will focus on statistical process control (SPC). SPC is a collection of analytic and graphical tools that are adaptable to many manufacturing situations. SPC can be employed to control manufacturing processes, conform to requirements, and reduce waste.
Note
If anybody wants to engage me as a consultant or trainer on this or other topics, please contact me. I have worked in Quality, Reliability, Applied Statistics, and Data Analytics over 30 years in design engineering and manufacturing. In the university, I taught at the graduate level. Also, I provide Minitab seminars to corporate clients, write articles, and have presented and written papers at SAE, ISSAT, and ASQ. I want to assist you.
Dennis Craggs, Consultant
810-964-1529
dlcraggs@me.com
Leave a Reply