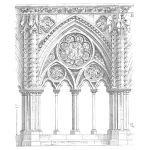
The Rate of Occurrence of Failure (ROCOF) curve is the sum of all the individual component failure curves across the service life of an asset. As shown below, it looks like a bathtub, giving it the nickname, a bathtub curve.
Equipment reliability is malleable by choice of policy and quality of practice.
The bathtub curve shown below is typical to industrial machines and equipment. Put simply, there are higher rates of component failure at the beginning and end in the service life of an equipment item. The high rates of component failure at the start of an asset’s operational life are due to poor manufacturing or installation quality controls. Random failures that occur during the asset’s use are due to the overstressing of microstructures. As components age, or are used in service, stress accumulates within their microstructure or the material degrades, and higher rates of component failure occur.
There are ways to reduce these failure rates, and so, lower and extend the bathtub curve. Firstly, using well designed equipment is effective capital asset selection. However, it is important to also have high quality maintenance performed on the asset to ensure the rate of failure curve stays low and events are stretched to longer and longer times. Numerous practices can be applied in each phase to prevent component failure.
Early Life Failure – use accuracy, precision, higher-level skills, error elimination practices etc.
Random Failures – use precision maintenance, applying operator ITLC (inspect, tighten, lubricate, clean), and deformation and degradation management to eliminate the possibility of overstress.
End of Life Failure – use better material selection, degradation management, better maintenance strategies, precision operating zones, and precision maintenance practices during the service life to help extend operating life.
Equipment reliability is created by the choice of policies and quality of practices used. By using best practices and removing the causes of microstructure deformation and degradation, you are choosing to create reliability in your assets. The benefits of which extend across your whole company, from fiscal earnings to production quality standards.
Removing thousands of causes of failure from across the life cycle of your operating assets is one of the many business benefits your organization gain when using Plant Wellness Way EAM methodology. It’s worth millions of dollars profit each year to make sure the parts in your plant and equipment do not fail. PWW EAM comes with processes and techniques to proactively identify the tens-of-thousands of defects and risks sitting inside your plant and equipment that will become future operating losses, wastes, and safety incidents.
Talk to us when you want a sure answer to prevent thousands of future problems and make new, lasting operating fortunes.
Leave a Reply