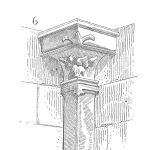
Asset reliability assessment when buying running and used operating plant and equipment. Aging asset reliability assessment can be done quantitatively if all past component stresses are know, or it is down qualitatively when only operating and maintenance history is available.
I am a developing reliability professional and often read your articles. I was wondering if you could give me a bit of advice about the subject of aging asset reliability assessment for operating assets?
Can you please share your thoughts on reliability assessment for a thermal power plant, and its importance in acquisition of a running ageing plant. Is it a common practice to look at this aspect prior to acquisition and is it practical? And if so, how do we go about it?
Thank you for your advice.
Hello Jyothi,
I agree with you that when acquiring an existing operation, be it a power plant or any other industrial facility, the due diligence needs to include analysis of the plant and equipment’s current condition. Especially its likely reliability during the coming years of ownership, and for its future resalable value.
What you have asked about is a very common requirement for insurers. Aging asset reliability assessment appraisal is often done by insurance companies taking on a new industrial client, or if an existing client asks for an insurance premium reduction. They will send assessors with checklists of standard questions to review and appraise each asset’s physical condition. They will also investigate the enterprise asset management and maintenance management systems for their content, completeness and robustness. In addition they will interview engineering, operations and maintenance department managers and supervisors using relevant checklists to get each persons’ view of the operation’s historic practices and culture.
QUALITATIVE AGING ASSET RELIABILITY ASSESSMENT
A nice thing about qualitative plant and equipment reliability assessment is you only need to walk around the operation observing the reliability practices, and operations and maintenance quality control methods in use; review the plant and equipment’s operating and maintenance history; and gain a good appreciation of the physical asset management systems and philosophies used during the original design and the subsequent years of operation. From such due diligence you will gain an appreciation of the organization’s asset management capability and by inference the likely health and condition of its operating assets.
QUANTITATIVE AGING ASSET RELIABILITY ASSESSMENT
Where a quantitative analysis of asset reliability is required it is first necessary to determine component materials-of-construction stress history to estimate the remaining life of the working components. As the entire life of plant and equipment involves probabilistic risk events with varying consequent effects on components’ failure, a quantitative analysis of equipment reliability can deliver results well wide of the real reliability. Typically quantitative assessment of reliability is justified and done in high risk situations such as for aircraft and aerospace, nuclear equipment, space flight, military equipment and technology, and where occupational health, safety and environmental consequences are potentially catastrophic upon failure (e.g. deep sea operation, applications using dangerous goods).
In general industry the history of component stresses are not recorded and so quantitative aging asset reliability assessment cannot be done. This situation is changing as more and more new equipment is being supplied with on-board sensors providing a full history of operating performance data that can be analyzed. But until component stress related information is available from plant and equipment as standard outputs it is normal that qualitative reliability assessment and auditing is used.
ORGANIZATIONAL RELIABILITY INDEX AND RELIABILITY CAPABILITY AUDIT
Elsewhere I’ve written that a big difference between safety and reliability is safety is an outcome you create in future, whereas reliability is an outcome you inherit from the past. You can improve safety over time, but you lose reliability with time. The implication when assessing operating plant reliability is you need to determine what an organization has done in the past to ensure high reliability assets, and whether its current business system can deliver and sustain highly reliable operating assets.
If you want a quick, rough-and-ready way to gauge the capability of an organization to have and sustain high reliability physical assets you can use our 5-factor Reliability Assessment Index explained in the 2-page PDF article A Scale for Measuring Reliability Health in Organizations. It will give you a strong indication of the effectiveness the organization’s practices and culture in achieving engineering asset reliability.
When you need a more extensive means to assess an organization’s capability to have high reliability assets we would use a Plant Wellness Reliability Audit. The system-of-reliability assessment arrives at an index measuring an operation’s capability to have and sustain highly reliably production assets. The Target Board shown below is used to display a spider-web diagram of organizational capability for world class production asset reliability.
To assess the Plant Wellness Index (PWI) we use a checklist of questions and factors related to each of the six arms of the spider web—Defect Elimination, Least Parts’ Stress, Systematic Success, Same Mission, Right Information, and Role Competence. There is a generic scale, called the PWI Key, used to rate the way a company’s business addresses each question in the six criteria.
After answering all questions in a category its overall index value is plotted on the Target Board. When an organization is hitting bulls-eyes in a category the index point is within the circle numbered ‘1’. The worse a category measures the further from the bulls-eye it will plot. An operation with bad capability to get reliable assets shows a category performance that is well away from the bulls-eye, whereas a world class reliability-focused organization would get bulls-eyes for all categories.
The assessment arrives at an index measuring an operation’s capability to have and sustain high reliability production assets. The Target Board is used to display the organizational capability for world class production asset reliability.
For example, the first question in the Least Parts’ Stress criterion is ‘All situations causing an asset’s working parts to be stressed are identified’. You would look for documented evidence that a company has a process which insures each production asset has been analyzed to identify which parts in it will be those that could fail. If such a process exists then the answer would rate near the bulls-eye. If no such process exists the rating would be a 10. If they have something approximating such a process, like RCM, they would get an in-between rating.
For the second question, ‘All stress situations have 3T parameters covering world class through to OEM design performance standards’ you would want documented evidence that the identified parts which can fail in an asset have defined operating parameters specified, e.g. ideal operating load plus a maximum operating load permitted by OEM; ideal operating temperature and least/maximum temperature allowed by OEM; ideal flow rate and most/least flow rates permitted by OEM; for lubricating and hydraulic oils they would have a world class ISO 4406 count as the Target and the OEM contamination specification as the outer limit, etc. In PWW we set the 3T quality assurance range with a world class Target as the ideal outcome, but will accept the OEM design criteria as the worst Tolerance that can be used. If the client has established an ideal and allowed operating zone for each of the failure prone parts they would rate close to the bulls-eye. If there are no operating quality controls for the parts that can fail they rate a 10.
The PWI audit tool is a different way to judge a client’s capability to deliver reliable plant and equipment compared to the standard audit tools used by most maintenance consultants. The questions used in the standard maintenance assessment tools do not focus on reliability creation, but typically measure maintenance maturity. That is interesting to know but it does not answer the question of what to do to get highly reliable assets. What PWI does is seek to explain why a company’s operation is having equipment failures and what is wrong with their various processes that have allowed equipment failures to happen.
When contemplating the acquisition of an operating plant it is smart business to know the health and condition of its machinery and equipment before you own it. There are simple, overall business system assessment methods as well as exhaustive asset-by-asset reliability assessment audits you can do.
I hope the above is of use to you. Let me know if you have further questions about the topic, or if you want to know more about doing a Plant Wellness Reliability Audit.
All the best to you,
Mike Sondalini
Leave a Reply