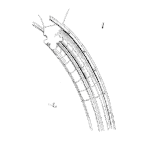
What is reliability management? Reliability Engineering? Would a product design or an organization benefit with a focus on reliability management and engineering? What is the value of a focus on reliability?
Any organization, that develops and produces products, has resource limits. It may be talent, capabilities, time, funding, or some combination of these.
Yet, the goal to create a product that meets customer expectations includes the concept of product reliability. The product should provide the expected functions over time, without failure. This expected product reliability occurs, even if the design requirements and advertising do not explicitly mention product reliability.
“It shouldn’t have failed so soon”
For example, consider a laptop that needs a new power supply.
When this situation came up, my first thought was how old the machine was. Is it still under warranty? Then my thoughts turned to the inconvenience of either being without my laptop during the repair period or the hassle of moving over to a new machine. If the machine was only a few months old, it would likely still be under warranty, yet my dissatisfaction would be higher. It shouldn’t have failed so soon.
If the machine was five years old, that’s a different story. I’d have had many years of use and if this was the first failure, I’d have gotten a lot of value.
Besides, it may well be time to upgrade to a new machine. The inconvenience of a repair or new machine, while not totally alleviated, is still much less.
The value of product reliability
The primary value of product reliability is in meeting the customer’s expectation that the product will work as intended for sufficient time.
The market rejects products that fail often, and desires products that ‘just work’. Creating a reputation for a reliable product assists in increasing sales.
An extension of the value that consumers place on reliability is the willingness to pay a premium for products with high reliability. Automobiles, computers, printers, appliances and test equipment are all examples where products known for high reliability charge a premium. It’s worth it, as the cost of downtime during a failure more than outweighs the additional purchase expense.
For the business creating a reliable product, it creates value in a similar manner. Products that are sought after and command a price premium lead to higher sales and higher profit margins.
Additionally, the lower failure rates reduce the warranty expenses, which further increases the profit margin.
Yes, it may cost more in materials to create a durable product, but it returns rewards of higher customer satisfaction, market share, and profit margin.
Reliability engineering – what’s our job?
Reliability engineering is an engineering field that deals with the study, evaluation, and life-cycle management of reliability: the ability of a system or component to perform its required functions under stated conditions for a specified period of time.
Reliability engineering includes the use of statistics, data analysis, experimental design, customer and environmental surveys, component and product testing, failure analysis, design, manufacturing, procurement, and at times marketing and finance.
It is a broad set of skills, and the proper application of reliability tools and techniques generally permit an organization to create a reliable product.
I like the role due to the span of tasks and disciplines. While some reliability engineers will specialize in one area of the field, say accelerated testing, others may find a role that spans nearly every function within an organization.
The ability to influence and create a product the meets the customer’s reliability performance expectations is both challenging and rewarding.
Reliability management
The oversight and control of reliability activities is a management role.
Some organizations have a dedicated reliability manager, others a senior reliability engineer, and in others, reliability management is part of the organization’s management functions. There is no one right way to organize to accomplish improved product reliability.
It is more the focus, brought across the organization, on the impact of decisions on the resulting product’s reliability performance. The management of reliability, like reliability engineering, may involve working closely with many functions throughout an organization.
Reliability engineering and management are very similar.
The former works to implement activities and analysis that enables the creation of a reliable product. The latter does the same though the allocation of resources to enable the right activities and analysis.
The organization that includes reliability considerations (i.e. requirements, predictions, risks, evaluations, analysis) deliberately and uses the information to guide decisions across the organization will create reliable products.
Those that ignore or isolate reliability to a limited role within the organization are less likely to create a reliable product.
The actual individual titles are less important than the reliability engineering activities and decisions. The reliability engineering skills are part of any engineering discipline; with some practice and encouragement, nearly all engineers have the capability.
The management skills are similar to any other product producing an organizational set of skills.
The ability to coordinate activities, allocate resources, and focus on reliability is augmented with a solid understanding of reliability engineering tools and techniques, just with any other management task.
Related:
Purpose of a Reliability Program (article)
Basics of Reliability Engineering (article)
Successful Reliability Engineers Add Value (article)
Leave a Reply