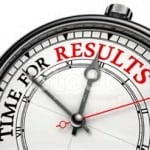
The Opportunity
Here is a diagram I generated when I was in the reliability group at my facility.
It came about because I was trying to identify why we may not be showing the value that was expected from the reliability improvement work we were doing.
Definitions
Some of the categories are easy to interpret but, to clarify, here is a synopsis of each:
Increased Output: The time can be put back into the maintenance workforce to get more tasks completed
Reduced Overtime: The extra time can be utilized to reduce the total overtime required
Emergency work reduction: The extra time can be used to do emergency work which will free up others to work on planned work
Reducing Failures: This can be through applying the time in Predictive Maintenance, or PM improvement
Reducing outside contractors: If you use outside contractors perhaps some of that work can be done with in-house personnel to save money
Helping to improve maintenance: Time can be utilized to improve PM’s, predictive routes, work on problem-solving teams, RCM work, etc.
Capital: If you have either capital groups or other groups that don’t go against the maintenance budget, the time can be utilized there to reduce the maintenance cost. (Granted this is a little fuzzy, but it was a real thing at our facility)
Attrition: If you generate enough opportunity, you might be able to allow someone to retire and not replace them
Waste: Do nothing and the opportunity, or a portion of it, will go to waste
Background
As a background to why I started thinking about this, I’ll relate a short story.
During an investigation of an improvement within the maintenance department, I found out that electricians were constantly being called to replace fuses on a bridge control circuit. The bridge is a movable part of an aluminum pot superstructure.
It has a limited travel though, and if it should hit the end stops, it would destroy parts if it didn’t stop moving. Because of this, there was a fuse on the motor circuit. It was designed to blow if there was an overcurrent in the motor.
The overcurrent was caused by the bridge hitting the end of its physical limits.
It is a whole other article about why they didn’t fix the problem of hitting the stops. One electrician was spending about ¾ of his/her time replacing fuses. The electrician got approval and replaced the fuses with a circuit breaker.
Because of this, the operators could reset the breaker without the need of an electrician.
A good improvement story with a successful outcome.
Capture the opportunity
The time freed up was approximately 30 hours per week as there were over 700 pots in the plant.
This got me thinking “ what did we do with that time?”
I was in the maintenance organization and knew we hadn’t reduced the workforce and the overtime hadn’t changed… Hmmmm.
What had happened?
We had generated an opportunity for improvement but hadn’t cashed the check. That time got absorbed into the other things by default, and no conscious thought was given to how to utilize it.
This drove me to ask, “why didn’t we do anything with this or other opportunities that were achieved in the maintenance organization?” I determined that the biggest reason was we didn’t capture the information or know that the opportunities were being generated.
I generated the categories in Figure 1 above to start thinking about where should the extra time go if we could identify it?
Decision Time
If we knew that we had freed up an electrician, we might choose to say, “I want to take that person’s time and not replace him (attrition).”
We might decide to use them to cut overtime by 40 hours per week or assign them to capital work to remove them off of the maintenance budget, or one of the other possibilities.
You can see in Figure 1 that there are many places this “extra time” could go. This is the list that I generated, and yours may be the same or include some other things.
The important thing to discuss is not necessarily what to do with the time, but rather, have I generated opportunities and what have I done with them?
If you are on the reliability side of things, your job is to generate opportunities.
You may not think of it this way, but I think that everything we do is going to come down to 1) Cost avoidance; 2) Reducing manpower, or 3) Direct material savings.
Full-Time Equivalent (FTE)
My example was convenient because it was close to an FTE (Full Time Equivalent) employee.
What do you do if you only generate 1/8 of an FTE? You can’t reduce 1/8 of an FTE, but you could plan that time if you knew it existed. If you do eight projects that each generate an opportunity of 1/8 FTE, that is 1 FTE, and you could consider attrition as a last resort.
We are now back to the same question – do you make a conscious decision on how to make the best use of the opportunities? As most of us know, small increments tend to be ignored or not identified.
After all, it is just a little improvement. I suspect that most do their jobs, generate improvements, but don’t think of equating it to time or think of it as an opportunity.
Lesson Learned
What is the purpose of this discussion?
Let’s assume you go throughout your time as a reliability engineer and save a significant number of incremental portions of an FTE. If you never point this out to anyone, you may have made significant gains in helping your organization, but it won’t be noticed.
It also won’t show up on the bottom-line because it won’t affect the important aspects of the maintenance budget. How do you do point out this “opportunity”?
I started tracking my reliability projects in a spreadsheet and assigned opportunity improvement to them.
Yes, this is subjective, but I always was very, very conservative and the numbers were easily justifiable. On occasion, I was asked “what do you do for me?” by management. I was always able to pull out the sheet and show them.
I continually alerted the management of the value, and let them know that it was my job to generate the opportunity, but it was their job to “cash the check”
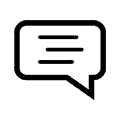
Leave a Reply