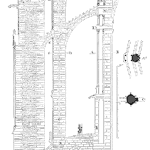
Asking the right question is important.
During a review meeting (informal or formal) asking a few reliability questions may reveal weaknesses, strengths, or uncertainty. The design team has many priorities and reliability is often difficult to estimate, yet knowing what is and isn’t known provides a clear picture of risks for decision makers.
If you are a decision maker and need to ascertain the reliability risks of the current design, then asking a couple of questions may provide just the insights you need. It also conveys that reliability is on your mind and that you want to have answers that are meaningful and well thought out.
Asking if the design is reliable is not useful.
It is a Yes/No questions and left to the judgment of the person asked. Instead, probe into the supporting evidence and underlying assumptions. You may find responses concerning reliability ranging from ‘trust me’, to theoretical models supported by carefully designed experiments. You may find out the true nature of the risk related to meeting reliability objectives.
The Questions
What will fail and why?
Explore what is likely to fail first and what causes the failure to occur. What stresses, scenarios or applications will hasten failure? What happens when these failures occur? Explore hardware, software, and human factor elements.
Then ask for the supporting evidence.
What elements of the design are pushing the edge of the team’s knowledge? Explore what is known, assumed, and unknown. Determine the areas that have reliability risk and set up plans to resolve or mitigate.
Continue the questions with an exploration of the use conditions.
This is both the environmental stresses and use profiles. How and where will the product be used and what is known, assumed, and unknown. Do we have measured distributions of stress conditions? Do we have evidence the product will survive the range and combinations of stresses and will do so over time? Which stress combination is the worst case and how many likely customers (be as specific as possible with these estimates) will experience these conditions?
What is the cost of a failure?
Failures will occur. What is the ramification to the customer and to us? In dollars and cents. Are the warranty or repair budget established, if so how? What is the basis for the accruals? If it’s not an engineering reliability estimate, why not?
What are the critical to reliability components, dimensions, and processes?
Back to the design team, ask about which elements are essential to the reliable performance of the product. How was this list determined? What are the criteria? Why can these elements not be fixed, resolved, or designed out? Cost? Time? What is the estimated impact on field failure costs? Is it still worth not fixing these issues?
Explore the plans to monitor and minimize variability for critical elements, when that makes sense. Also, ask about which components and elements are likely to change over time both from the suppliers and over time during use.
Questions about reliability
The questions are a way to determine if a design is reliable?
Instead of a yes/no response, ask for and expect a rich discussion about what will cause the product to fail, the robustness of the design and process, and the integration of product reliability with the rest of the business.
Typo noticed in: “Do we have measured distributions of stress contains?” “conditions”, I believe
Thanks – will update