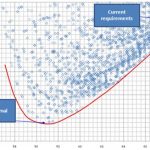
Intuitively, the emphasis in reliability to achieve a reduction in warranty and in-service costs results in some minimal increase in development and manufacturing costs. However, use of the proper techniques during the proper life cycle phase will help to minimize total life cycle cost (LCC).
To minimize total LCC, your organization should do two things:
1. Choose the best techniques from all of the techniques available, and apply these techniques at the proper phases of the product life cycle.
2. Properly integrate these techniques by feeding information between different phases of the product life cycle.
- Program costs go up as you spend more on reliability improvement. At a certain point, you won’t get any return on investment (ROI), because the reliability has reached a point where it is becoming increasingly difficult to improve. That is why it is important to know what the goal is. It can be just as detrimental to your company to produce a product that is too reliable as not reliable enough. The product that is too reliable usually comes with increased costs; your customers may not need this level of reliability and will opt for the less expensive product. When was the last time you purchased a $2,000 blender or toaster?
- Effects of Over-reliability in Development:
- Product is too expensive for target market
- Product is later getting to market
- Company is behind technology leaders due to slow program development cycles
- Effects of Under-reliability in Development
- High field Return Rate
- High Warranty Cost
- Loss of product sales once low reliability is known in market
- Loss of market share in all product lines due to poor brand perception.
-Adam
Leave a Reply