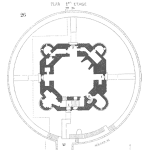
by Alan Ross
Getting experts to agree on most things is challenging at best, and often,downright impossible. Getting transformer experts to agree might be even more challenging. Despite the fact that transformers have been around for nearly a century—and with varying opinions on transformer design and maintenance—most experts agree that not all transformer failures are alike. Also widely recognized is that the life of the insulation or paper is the primary limiting factor towards the life of the transformer.
Since most industrial companies use power to produce something, the risks associated with loss of that power have been misunderstood and, all too often, ignored. But risk comes in many different forms. Risk of failure can be quantified by the insurance industry as the cost to replace the transformer. But the loss of productive capacity—business interruption loss—is usually much higher than the cost of transformer replacement alone.
Additionally, what is the risk of failure when the condition of the unit has deteriorated and routine preventive maintenance ignored? When asked, “Why do you test the oil in your transformers?” the most common response is, “Our insurance company requires it.” The need for a reliable system must become the reason why we test transformers, since every reliable system starts with and depends on reliable, uninterrupted power.
Condition Based Risks
Why do transformers fail in the first place? Many failures happen after an incident,such as a lightning strike or a failure somewhere down line from the transformer. These anomalies can be characterized as electrical, mechanical or thermal, but for the most part they are separate from the condition of the unit itself. These may be root-cause failures, but they 2neglect a significant contributing factor: the actual condition of the unit. An overloaded transformer with well-maintained dielectric fluid—and which is not already weakened by poor maintenance—is much less likely to fail than one that has not been maintained.
Can transformer failures be avoided? Can life extension mitigate this risk? I am tremendously biased when it comes to maximizing the life of a transformer because of my relationship with SDMyers. I have seen first-hand how effective it is to develop standards, to rigorously test and track the condition of the fleet of transformers and to maintain the fleet according to those standards. Quite simply, the easiest risk to mitigate is the condition-based risk.
It has become commonplace to maintain one’s productive assets with increasing rigor, yet too often chemical or electrical testing of a transformer is confused with the maintenance of a transformer. In one illustrative case, SDMyers was asked to develop a standard for testing and maintenance for a customer with multiple transformers and multiple sites. There was a great deal of commonality of the units, and we had conducted chemical testing over a seven-year time period, tracking the condition of the oil in the units. When we asked for the electrical test data so that we could properly assess the complete condition of each unit, we were informed that no additional data was available.
I think it was that moment that changed my perspective on the whole issue of risk and reliability of electrical systems, with particular emphasis on the heart of the system, the transformer. There is so much more to a complete condition assessment than trended oil tests. While that is a great and important first step, the next steps are equally as critical.
Keeping your transformers in good condition may require occasional oil processing to remove harmful contaminants. There is also a need to identify some standards for recommended maintenance on oil processing. It is important to realize that not all oil processing is alike. While some contractors clean the oil, others may process on the unit until they address issues in both the paper and the oil.
What criteria should be used for electrical testing to create a “Best Practices” testing and maintenance protocol? What data is available from the manufacturer at the time of assembly and installation to determine changes over time? A simple SFRA test can serve as the baseline for future condition assessment, yet too often we do not have that data.
Of course, our real concern is developing a reliable system that can address the condition of the unit without a lot of added costs or downtime, during the life of that unit, not at the end of life. It is all about assessment, planning and systems.
The Weakest Link: Paper
While there are cases when transformers fail without warning, most failures are ones that we can see coming. Deteriorating paper and oil inside a transformer emit gases, which contribute to a better diagnosis of the condition of the unit. Moisture content has also become a significantly valuable predictor of failure. Sadly, gassing and high moisture content are not perceived as critically important as they should be. Accelerated deterioration of the paper insulation is the result of moisture, acid, overheating or oxidation—a condition that weakens the the unit’s performance.
One of the underlying causes of this lack of preventative maintenance for transformers is that they have been very trustworthy for a very long time. Transformers have been overbuilt in the past, and many have performed beyond their projected useful life, and they continue to hum along behind the substation fence. With the onset of computer modeling for transformer design, the specifications began to be met without overbuilding the transformer. In short, we have been spoiled and have become complacent.
Transformers built today are built with much smaller margin for error than those of the past. If we now take the same approach to reliability as we did with equipment from the past, we will most likely see more unplanned outages and downtime from transformer failures than ever before.
Paper Aging
The best measure of paper aging is furan analysis. As paper ages, it releases Furan gases that are undisputed indicators of paper degradation. The Department of Defense, Reliability Information Analysis Center (RIAC) states the following:
“Furans are a family of organic compounds which are formed by degradation of paper insulation. Overheating, oxidation and degradation by high moisture content contribute to the destruction of insulation and form furanic compounds. Changes in furans between dissolved gas analysis tests are more important than individual numbers.”
Excuse Me, I’ve Got Gas
Gases are dissolved in the transformer oil and are formed by both normal operation and aging and by anomalies or abnormal events. By analyzing the volume, types, proportions, and rate of production of dissolved gases, we can get a very good picture of what has happened or what is happening inside the unit. Because these gases can reveal the faults of a transformer, they are known as fault gases. Gases are produced by oxidation, vaporization, insulation decomposition, oil breakdown and electrolytic action.
While it is becoming increasingly common for primary units within a substation (or in the case of steel production, the furnace units) to have DGA monitors installed on the units, the monitor will likely detect only that a gas or gases are present. An oil sample with DGA can determine the amount of gas and, in the case of frequent testing, the rate of change in that gas. The resulting test data reveals the cause of the increased level of gas. In extreme cases, the analysis will indicate conditions consistent with a potential catastrophic failure. In most cases it will indicate a weakening of the overall condition of the unit and the need to avoid overheating or higher loading.
End-of-Life Risks
Recently, SDMyers was asked to consider the end-of-life risks for a metal processing facility. While the greatest risk was that of application, the most costly risk involved several rectifiers that were built in the 1990s. These three rectifiers were not part of the normal inventory or the production schedule of the transformer manufacturer. These units were essentially customized units with a 26-week lead time. If there is no planned back-up transformer, no spare and no way to operate without one of the rectifiers, then the end-of-life risk increases.
With the rapid expansion of industry in America, transformer manufacturing and installation peaked in the 1960s and 1970s. Many of the transformers designed during that time period are no longer being produced. Some of those units had very tight physical footprints due to the building of production facilities around them and may not now even be able to travel the roads and rails available years ago. In one instance, the old rail spur leading to a facility ended seven miles away from the plant, so getting the unit out and back in again was more costly than rewinding the unit itself. It also required special transportation and permits, a competency the company did not have.
Only when the end-of-life risk and the application risk were combined could we monetize the cost of developing a reaction plan. That cost will likely move any decision on planning up the corporate ladder to a much higher level. Is it better to (1) plan ahead by developing a reaction plan, (2) develop budgetary costs for unit rebuild or replacement, (3) understand and budget for transportation and contractor access, or is it better to wait until something (usually bad) happens? Of course, in this instance, good reaction plans will save significant amounts of time and money while allowing corporate management to develop capital budget plans over years rather than within days of a failure.
Life Extension
The first and most important take-away from this risk analysis must be that we are doing everything possible and economically feasible to extend the life of these critical assets. Even a company with only one transformer is at risk of they happen to run their data center off that one unit. How long can most businesses remain afloat if their data and/or ERP systems shut down for a couple of weeks? Imagine getting a phone call from the CEO about that.
The subject of transformer maintenance and life extension has been viewed many different ways in a variety of markets, yet it’s certainly becoming a universal concern. The unification of strategy on transformer maintenance and life extension have been driven by some common factors that include the aging population of transformers and a higher than expected failure rate with newer replacement units.
The general aging population of electrical power equipment—given that the infrastructure building peaked in the 60s and 70s as pointed out earlier—means a great potential for failure over the next decade. Prior to having to develop impact assessments, reaction plans and condition assessments, we should first consider a life extension system to develop and maintain the necessary testing and preventive maintenance practices as a priority.
Developing a Reliable System
So where does that leave us? What should any company do that depends on safe, reliable and uninterrupted electrical power?
- Understand the short and long term, direct and indirect impact and costs associated with unplanned power outages that result from the loss of a transformer
- Develop and implement a set of standards for determining the operating condition of your transformers through the use of intrusive and non-intrusive testing
- Develop a company-wide preventative maintenance plan, giving reliability professionals the tools they need to monitor and maintain this critical and often overlooked asset class
- Develop a reaction plan for every critical transformer in your area of responsibility/control
Preventive Maintenance Plans
Any good PM plan will start with an assessment of the condition of the transformers. However, while many transformer oil testing labs in the U.S. are dependable and of high quality, the weakest link in that testing process is often the sampling itself. Contaminated sampling leads to invalid test results or worse, false negatives. When the sampling process is coupled with a reliable field inspection, the knowledge gained from that sample is more predictive of potential failure. It also leads to a clear maintenance profile for the transformer.
Too often, transformer maintenance companies are focused on cleaning the oil, based on good inspection and sampling information. But cleaning the oil does not necessarily clean the paper. Moisture is a perfect example. There is usually much more moisture in the paper than in the oil. Processing the oil to remove that moisture is a temporary fix. Within days or weeks moisture will leach out of the paper and back into the oil, leading to a high reading in the Karl Fisher test (the one proscribed for moisture). The same principle is true for acid build up in the oil and paper.
Best Practices for transformer maintenance will be the result of a program for:
- Oil Testing. This is to be conducted on a regular basis with corresponding maintenance assessment reporting. Remember, if testing is conducted only because the insurance company requires it, the point of developing a reliable electrical system is altogether missed.
- Electrical Testing. For more critical units—and in the event of an oil test result that indicates a need for additional testing—standardized testing will be required.
- Mechanical Inspections. Checking the level, proper functioning gauges, bushings, fans, radiators and connections.
- Infrared (IR). While most companies provide an annual IR scan of their entire system, there is a great advantage to conducting an annual routine IR at the same time the oil sample is taken. The combined information can lead to specifics about faults, loose connections or potential bushing failure.
- Monitoring for gases. Fault gases can lead to catastrophic failure, which goes well beyond a simple unplanned outage. Monitoring for these gases creates an early warning system. Since Hydrogen is almost always present with gases, a cost-effective solution may well be a single gas monitor with a robust follow up oil testing program.
- Why do we test? Amazingly, one of the most frequent responses we hear is, “Because our insurance company requires it.” This really misses the point. The real reason we test is to determine the condition of the unit so we can perform preventive A well-maintained and serviced transformer can last over half a century. We test so that we may more fully understand the condition of our equipment, and that knowledge leads to wisdom to provide a low-cost, reliable electric system.
While we may not get every transformer expert to agree on everything, there is universal agreement that a healthy and robust electrical system starts with the heart of that system: the transformer.
Alan Ross is the President of the Electric Power Reliability Alliance (EPRA). He is responsible for leading the alliance to build electric system reliability in the industrial and commercial marketplace. Formerly, Alan was the Vice President of Reliability at SD Myers.
I’ve been having issues with my electrical system, and I’m not sure what to do about it. It makes sense that I would want to ensure that the right transformer is used! I can see how it could cause a lot of problems if I use the wrong ones. It would be a good idea to work with a professional for this.