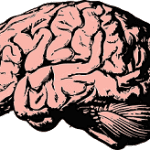
If a manufacturing plant was a human brain: Maintenance would be the repairing blood flow, Operations would be the electricity sparking between synapses, and Reliability would be the conscience.
It is important to remember that in a plant, each department has its own function, and the interplay between them is desirable and critical to an effective organization.
Operations advocates for production. Maintenance advocates for the equipment. Reliability advocates for doing the right thing.
Here is an example:
A critical pump without an installed spare is making an awful racket. The Operator notices it on their daily walk down through the area and promptly puts in a work notification. Operations Supervisor (gatekeeper) reviews it and approves. The notification goes to Maintenance.
Maintenance reviews it in the daily morning meeting and sends a Reliability Engineer out to take vibration data. The data comes back that the bearings are in Stage 3 failure. What to do? Should we shut down production and replace the bearings? Or run-to-failure and risk additional damage and a longer repair interval?
Operations says, “But wait! We have to run! A critical customer is waiting for our product and we will lose money and face if we delay.”
Maintenance says, “The equipment must be repaired immediately or catastrophe will ensue!”
Reliability says, “Let’s get the facts. How long will the repair take? Do we have the parts on inventory, and if not how long is the lead time? How much will it cost us to shut down the line? What kind of relationship do we have with the waiting customer? What is the potential impact of cost and time if the equipment is damaged because repair is not immediate?”
Ultimately, it is the job of Reliability to gather the evidence and present it with a recommendation to management on how to move forward. Reliability acts as the conscience of the plant in an emotional situation, to gather and objectively look at the facts, and suggest how best to allocate the available resources. Finally, management must decide how to move forward.
Maintenance can’t be the conscience because they are working for the best interest of the equipment. They should advocate for repair or replacement as quickly as possible. This reduces their backlog size and gets a high priority, corrective work order off their KPIs. It also reduces the cost of the department to repair because less labor hours and fewer expensive parts are needed if the equipment doesn’t run to failure and risk additional damage.
Operations can’t be the conscience because they are focused on production. If the plant is down for a repair, their billable labor hours are reduced and therefore overhead is being paid to make no product. The schedule gets off track, affecting production targets. On-time delivery of the entire customer order is compromised. There is a high potential for customer complaints due to the delay. All of this affects Operations KPIs adversely.
Operations and Maintenance KPI’s are designed to be short-sighted, because that is the best way to motivate them.
Reliability, on the other hand, is driven by the best result in the long term, which ultimately results in better KPIs for Ops and Maintenance but not Right Now. In fact, if Reliability is really doing the job right, then the situation described would rarely or never happen, because ultrasound would be picking up the bearing failure in Stage 1, long before it becomes an Operations or Maintenance problem.
Those departments will be impacted in positive ways. Production will not be lost, and Maintenance will have a nice low priority planned Work Order to complete during scheduled downtime, with the proper parts ordered during the planning process long before implementation is needed.
Firefighters need not apply, and everybody looks good to management.
This is why I consider Reliability to be the conscience of the plant. We look forward for the best path for long term satisfaction of the plant, rather than the Right Now.
Reliability is that little inner voice that says, “I really ought to plan for that contingency, because if I don’t it’s probably going to happen in a big way.”
It is easy to say you don’t need an ultrasound route because chances are that failure will be picked up in Stage 2 by the monthly vibration route. But Reliability’s conscience says, “But wait, if I catch the damage now then everybody has more time to plan for it and we will certainly be ready, and maybe we can even prevent it.”
So, the next time Operations or Maintenance is pressing Reliability for an answer or results Right Now, remind them that a solid Reliability program is focused on the long term, and doing the right thing takes time and diligence to be successful.
Leave a Reply