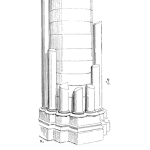
To Embed Safe Work Practices You Write Detailed, Strict Workplace Safety Procedures that Get World Class Job Safety
You must select OHS risk management mitigations appropriate to a job safety hazard using a formal method that delivers safe work practices.
Each task safety control will need to be developed, assessed for suitability, and recorded so it’s clear what the plan is, and how it is to be done.
In the end, there is a practically designed, completely resourced, fully scheduled, and totally sure safe work practice procedure approved for use.
The need to have a designed business system to guarantee occupation health and safety means your workplace safety performance is not an accidental outcome—you must create and use sure ways to guarantee world class safety results for the people in your Company, and those people it impacts. You must design, build and use a safety management system which makes the workplace safe, and then continually safer again.
The most effective safety management systems are those designed to eliminate workplace hazards; second are those designed to prevent and control workplace hazards. Though workplace hazards elimination has the best safety strategy results, prevention and control of workplace hazards is an acceptable first risk management strategy to use.
There is a misunderstanding in occupational health and safety circles that a Safe Work Method Statement (SWMS) is as good as a Safe Work Practice Procedure for high risk work control. In fact, they are so vastly dissimilar in the way they control job risk that they are incomparable. The difference between the two approaches for addressing high risk work makes Safe Work Practice Procedures much more robust and anti-fragile than Safe Work Method Statements.
To develop a Safe Work Method Statement requires an assessment of the risks associated with a work plan. The SWMS lists only milestone job steps and the related methods and equipment used to complete the job. To assist in identifying potential hazards and their risks you make use of resources such as workplace experience and consultation with competent people (e.g. toolbox talks), codes and standards, industry publications (e.g. safety alerts; trade group hazard profiles), etc. Provided there is a written indication in the Safe Work Method Statement of how the job step risks are addressed, then its purpose is suitably achieved. You find companies adopt completed SWMS templates that are reviewed when required for a job. The Safe Work Method Statement templates might have 15 to 20 rows in which to record the job steps. This causes people to record only the key steps in a job. Yet when the complete job is analysed in detail the number of activities to complete the tasks may number several dozen. Each activity can carry a variety of risks. It is quite easy for one job to have several hundred opportunities for errors, illness, and safety incidents.
A Safe Work Practice Procedure takes job safety and risk prevention well beyond the Safe Work Method Statement standard. In documented Safe Work Practices you specifically indicate what practices are only to be used to do the job. Whereas with an SWMS the choice of mitigations for identified risks is left up to the incumbent to select and apply, that choice is removed in a Safe Work Practice Procedure and instead the necessary mitigation is specified in the document. This allows the chosen risk controls to be reviewed and disputed or confirmed by competent others. A Safe Work Practice cannot use a pre-completed template dusted off for use again, as the risk mitigations can only be finalized once every activity in each task of a job is specified how it will be done.
Writing Truly Effective Safe Work Practices for High Risk Work
The development of soundly written Safe Work Practices Procedure is not only about designing the workflow so only safe work methods are used, it also requires removing all unsafe work practices and intentionally creating safe work areas and healthy environments. Whereas a Safe Work Method Statement for a job lists only its milestone work steps, a fully detailed Safe Work Practice Procedure notes every activity and how it is safety done. Following a fully itemized and specified Safe Work Practice not only prevents job risks at the task level, it can also be used to reduce and proactively prevent risks in dozens of potential occupational health and safety (OHS) incidents, like noise exposure, respiratory harm, blood-borne pathogens, chemical use and storage, electric shock, and many other injuries that may result from activities wrongly performed.
Create detailed Safe Work Practices and Safe Work Procedures that address each activity in each task of a job. Unlike a Safe Work Method Statement, where only the job plan needs to be considered, Safe Work Practices includes every action that will be undertaken to complete the job. This makes Safe Work Practice Procedures the preferred work risk prevention solution for high risk jobs when maximum safety under conditions with numerous factors need to be controlled.
Once a Safe Working Practices Procedure is developed you may need workforce education, training, and individual assistance for it to become the established practice.
When you want world class safe work practices to be used, and a healthy working environment maintained on your jobs, ensure that your people use our Safe Work Practices. With a formal safe work procedure, your workers only need follow the instructions and use the inbuilt risk mitigations to deliver the job right-first-time. On your next high risk job make sure it’s better controlled, with fewer errors, healthier, and with least work safety risk than ever before.
All the best to you,
Mike Sondalini
Lifetime Reliability Solutions HQ
Leave a Reply