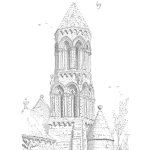
Something to think about in a day and age when most companies post their mission, vision, and goals on the company web page.
Do we really stand behind these statements and demonstrate the behaviors that clearly show we are willing to do what it takes to create a safe workplace?
If you have ever questioned this, consider two questions I ask RCM Teams as we analyze failure modes that impact health, safety, and environment:
- If someone were to lose a finger or part of a hand in a machine at your plant, how long would it be before the equipment was up and running?
- If someone were to die in a work-related incident working on this equipment, how long would it be before the equipment is up and running?
Some of the answers might surprise you, someone in the food industry once told me; “It would be quite a while we would probably have to clean the machine quite thoroughly before they would let us run it again so I would say at least 4 hours.
The answers I get to these questions tell me a lot about each company and the value they put on not only employee health, safety, and environment but the well-being of each employee and their family.
I have come to realize I was lucky enough to work for a company who truly valued our safety and wellbeing. We were force-fed health, safety and environmental standards and regulations from the time I was an apprentice all the way through my time as a reliability engineer.
Needless to say, the most shocking discussion I have ever had with a company was about 10 years ago just outside of Houston, we were discussing consequence ranking criteria for failure modes, I had suggested that any failure mode that impacted employee health, safety or environment should be considered a high consequence.
A controls engineer who worked for operations at the plant spoke up and said: “As a company, we already have a consequence ranking system, do you mind if we use that?”
I replied that would be great but we would need a copy of the criteria to refer to as we performed the analysis and within 5 minutes he had a copy for me to review.
I looked over the document and tried to contain the shock of finding out that in order for a failure to have a high consequence at this company the incident had to garner national news coverage!
After reading the document I looked up at the group and asked two questions;
- How many people die in on the job accidents each day in the United States?
- How many of those deaths are covered on the national news?
In 2013, 4,585 workers died in on the job accidents, that’s 12.5 people a day! How many of those deaths make the national news each day?
So the message here is that if one of us in this room right now were killed on the job today your company would not consider that a high consequence failure?
Think about the message that sends to everyone who works here; bad press means more to this company than your life does!
Companies who understand health, safety, and environment and value their employees have a common understanding that if we pay attention to the little things the big things never happen.
If we build a culture that treats a near miss the same way it treats an OSHA reportable, fewer reportable incidents occur. Companies that follow Lock Out Tag Out to the letter of the law and audit their own process build a culture where people won’t attempt to short-the process.
More important, companies who refuse to restart equipment until after a thorough incident review with operations, maintenance, and EHS representatives send a message everyone who works there that safety is important.
They recognize that in working together to perform a thorough investigation of the incident they can determine exactly what happened and why, and then work to eliminate the behaviors.
Ten years later I after learning that there are actually companies who operate today who don’t consider an on the job accident that takes the life of one of their employees or contractors a HIGH consequence I can still remember their corporate mission/vision statement on safety that hung in one of their conference rooms: “Our company is committed to safe, compliant and reliable operations through continuous improvement, capability, and execution.”
I guess they forgot to add “but only if it makes the national news.”
The reality is when it comes to reducing and eliminating health, safety and environmental incidents and accidents, it’s as simple as paying attention to the small things.
Treat near misses as if they were an actual incident, take the time to determine the causes and look to eliminate causes and defects.
Safety isn’t a slogan, a mission or a vision, it’s a lifestyle!
Yes, safety is a lifestyle and should be lived as we live our daily life. to me, safety should be a part of you just as breathing air is apart of you