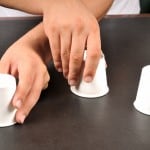
Many product programs ( actually all) are on a tight schedule. When Accelerated Life Testing (ALT) get’s it’s place in the process it is another mouth to feed. ALT is not a short process. Each round of testing typically takes weeks, and the results may drive design changes that prescribe additional testing. It is common to want to get the ALT process going as quickly as possible. In this haste the primary wear-out failure modes and it’s driving stresses are confidently stated, a model is created, and the test is started.
This seems insane to me. The resource and schedule hit that is being invested in the ALT process is significant, and a total waste of time if the stressors and model are incorrect. Not only are you losing any return on the test program there are two disastrous outcomes of an incorrect ALT program.
- The test says that the product can survive the use life goal, but it can’t
- The test says the product can not make it to the use-life goal but it actually can.
In scenario 1 you are sending out a product that will have a sudden spike with a 100% failure rate sometime during expected use-life. Remember that wear-out failure modes are a design characteristic and guaranteed.
The second scenario hit’s the panic button mid-development and will possibly drive a major redesign which in turn will delay product time to market as well as other product development program start dates. This is then added to by the fact you do not know anything about the real wear-out failure mode. At least in scenario 1 the customer was nice enough to do your life testing for you and now you know the primary wear-out failure mode.
This is simply solved by putting a specific milestone in the program for communication and evaluation of the wear-out failure mode and related factors.
- Collect a team of the people who know the most about the design technology. This includes technicians, service people, R&D engineers/scientists, design engineers, QA. It is a small investment on their part to share what they know about how the technology works.
- Decide if a DFMEA, FTA, or other failure risk assessment should be done to further parse out the wear-out failure modes and the driving stresses.
- Do some simple experiments on the predicted physics of failure. This does not require full units. It can often be done with raw material, older generation products, spare parts or simple design assemblies. We are testing the physics of failure, no the design operation.
- Create and validate a model. The ALT model should be demonstrated at three levels to verify it’s relation to the wear-out failure mode and the correct model factors.
These steps are a small increase in investment in an ALT program that ensures valuable results. It’s analogous to taking the time to pull out a map and plan a trip before just hoping in the car and heading in what you think is the right direction. You’re going to be hearing a lot of “Are we there yet” on the way. Making the trip longer is not a good idea.
I will be speaking on this topic at the ASTR conference this fall in Austin Texas on September 28th. If you can not attend look for a video of the seminar on the blog soon after.
-Adam
Leave a Reply