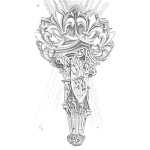
A good way to change mindsets and behaviors toward preventing forced outages and stoppages is to show everyone in the operation the total business losses of breakdowns.
It is incredible what the total business losses of breakdowns can rise too. Plant and equipment breakdowns are ultimately due to having wrong thinking and doing wrong practices. In this response to an FAQ, I advise to tell your people the true costs of breakdowns. Let them share the pain and loss suffered by the business and start them thinking of better ways to care for their operating assets.
Often an item of plant will fail and there is a group huddle about when the job is to be done. Some will insist the repair is carried out here and now, with overtime if required. Others will say that there is a spare unit so the repair of the broken unit can wait until tomorrow (that is, in ‘ordinary’ time). Even without a spare unit, there is a case to be made to just leave it to the next ‘ordinary’ time shift to effect repairs.
Usually the guys in the huddle are the tradesmen directly concerned with maintenance activities, and generally are not aware of the plant risk or cost ramifications involved.
Are you aware if anybody has written a white paper that considers this aspect of maintenance, and summarized all the necessary information into a simple spreadsheet. Then certain factors and costs can be entered into the spreadsheet, which will give a cost for either option, hence allowing a very quick decision to be made.
The risk factor could be taken from a simple risk vs outcome matrix. Other things to be considered in the modelling may be:
- Hourly cost of labor
- Resources required
- MTTR plus time to bring back to an available state
- Cost of parts
- Risk to plant
- Cost of downtime
- Cost of capital
- Etc.
I look forward to your reply.
Hello Kenneth,
Helping your shop floor people to make the right business decisions in plant breakdown situations is highly commendable. Basing the choice of response on first identifying the true and full business risk from a failure event is wise.
Unfortunately, if you expect your maintenance and operations people to sit down around a computer, or use a digital pad or tablet at the breakdown, and develop or complete a spread sheet to calculate the financial loss to the business of the stoppage, then decide the course of action, I would expect none of them will. If they did model the response options they would probably be wrong because your shop floor people are unaware of all consequential effects and also carry biases. They will arrive at the answer they like, which still may not be the best choice for the business.
I suspect you do not actually want to turn your shop floor operations and maintenance people into financial modelling experts. (Though I would expect your maintenance engineers and maintenance manager to be financial modeling experts.) You really want them to make the best financial choices for your company when there are no prescribed best actions to follow.
In all honesty Kenneth, shop floor people are not responsible to run the business effectively. That is their managers’ duty. Your management should have already worked out what is the best thing to do for the business when each asset breakdowns and set those actions down as standard operating practice (SOP) to be followed by their staff and employees. Then, upon breakdown, the maintainers and operators go to the computer or digital tablet, bring-up the relevant SOP, and do the actions and responses it describes.
The simplest solution (that I have seen) for what you are trying to achieve is to publish a list of equipment numbers and the business-wide cost and loss of an hour’s downtime for each tag number.
Rio Tinto at their Pilbara iron ore mine sites in Western Australia have a list of every asset’s total loss to the company per hour of downtime. They have a conveyor that costs them $300,000 lost sales each hour it does not run. You can be sure that everyone at that operation knows what they must do to keep that asset running.
It is my experience shop floor people in maintenance and operations will make good decisions to minimize your production losses once they know the total moneys a failure costs the company and themselves. People will instinctively work-out the best strategy and actions for the business if they know the per hour cost of a loss event and how much bonus they are personally losing from the failure.
It is human nature to want to minimize personal loss and get maximum gain. A successful breakdown prevention strategy needs to also benefit the people who will prevent the breakdowns. To ‘reward what you want’ is the surest way to get the results you want. That is why you need to clearly identify the financial loss of forced stoppages and breakdowns—your people need to know how much money they are missing out on.
If I was doing what you are trying to do I would get a layout drawing of the whole operation showing the production assets. On the drawing, in big red numbers, I would write the total business-wide and opportunity cost/loss for each asset of an hour downtime. I would put a copy in the maintenance workshop and another copy in the operations control room.
To supplement that I would put a copy of the drawing and a list of the same information on the Intranet so everyone in the whole company knows how much a breakdown of an asset is losing their business and reducing their bonuses. I might even go as far as putting a counter in the corporate dashboard screen of the daily moneys lost to failures and breakdowns across the site. (That would get the senior managers jumping.)
Be sure to correctly identify what options are already available to minimize the loss upon each asset’s failure. For example, if on breakdown the product can be diverted to another circuit and production is largely unaffected, then the breakdown will only be the total business-wide cost of the failure rectification and the minor production disruption. Do not claim greater impact than what are the true costs and losses if a failure event happens. Your maintenance and operations people know what can be done to keep the plant running. Any falsehoods will be quickly identified.
To summaries: All the financial modelling you want your people to do for an asset’s breakdown needs to be done for them and the best choices identified and made public knowledge. The hourly losses and costs of asset failure are not a secret—put the financial truth onto the production assets layout drawing in big red numbers. The process of arriving at the true losses for each asset breakdown, and publishing the outcome for all to use, sets in place the eventual identification of the best strategy and actions to do to minimize operating profit loss when an asset fails.
The biggest worry I have in doing the above is that you risk sending a ‘signal’ to everyone in your company that management accepts breakdowns as part of normal business performance. That is a terrible and disasters belief for managers to have. Breakdowns and forced outages are evidence of weak processes, misconceptions and errors in a company. Knowing how much money a failure costs is useful to encourage sensible response, but there should have been no failures in the first place! Instead of living with the losses from breakdowns, identify and adopt the proper and right strategy, practices and habits that create endless reliability. That is what the Plant Wellness Way was designed to do and its adoption will save you the vast majority of the money now lost in breakdowns and forced outages.
I hope these thoughts are useful to you.
All the best to you,
Mike Sondalini
Leave a Reply