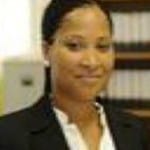
Guest Post by Roxann Dawson (first posted on CERM ® RISK INSIGHTS – reposted here with permission)
In order to improve business performance, manufacturing companies need to reduce the levels of non-conformance and attendant failure costs stemming from poor product design and development. Failure costs generally make up the largest cost category in a manufacturing business and include those attributable to rework, scrap, warranty claims, product recall and product liability claims. This represents lost profit to a business and as a result, it is the area in which the greatest improvement in competitiveness can be made.
The traditional approach saw inspection used as a ‘filter’ to sort good from bad and is suggested to be detection orientated, basically a continuous cycle of re-active firefighting.
LINK BETWEEN DESIGN AND
QUALITY
Modern studies have realised for many years that waiting until the product is at the end of the production line to measure its quality is not good business practice. This has led to an increased focus on the integration of quality into the early design stages of product development. This gradually saw a left-shift away from ‘traditional on-line’ quality techniques, such as Statistical Quality Control to an ‘off-line’ quality approach using design tools and techniques; adopting a more pro-active approach through better planning.
The most significant costs savings can result from changes in product design rather than, say, from changes in production methods. Studies have shown that the costs ‘fixed’ at the planning and design stages in product development are typically between 60% and 85%; but the costs actually incurred may only be 5% of the total committed for the project. Therefore the more problems prevented early on, through careful design, the fewer problems that have to be corrected later when they are difficult and expensive to change.
Design is recognised as a major determinant of quality and therefore cost. It is also a driving factor in determining the ‘time to market’ of products. Historically it could be said that Designers have focused on product styling, function and structural integrity. Demands now dictates that design now needs to include assurance that the product will conform to the customer requirements; comply to specification; meet cost targets and ensure quality and reliability in every aspect of the product’s use; all within the same production programme.
Good design practice does not simply mean trying to design the product so that it will not fail, but also identifying how it might fail and with what consequences. Effective understanding of the quality of conformance associated with design decisions requires undertaking a number of engineering activities in the early stages of product development. In addition to understanding the capability of the design, the Designer must consider the severity of potential failures and make sure the design is sufficiently robust to effectively eliminate or accommodate defects.
Effective failure analysis is an essential part of quality. Failure Mode and Effects Analysis (FMEA) is one of the preferred tools used in quality and reliability improvement. Research has proven that as much as 70% and 80% of potential failures could be identified at design stage by applying effective use of FMEA; performed correctly it can alleviate late design changes and provide better mitigations of foreseeable product or service risks.
CONCLUSION
Quality can be designed in with optimal part selection and proper integration of parts, for minimum interaction problems. By considering the cumulative effect of part quality on product quality, Designers are encouraged to carefully specify part quality.
Design for Manufacturability (DFM) can reduce many costs, since products can be quickly assembled from fewer parts. Thus, products are easier to build and assemble, in less time, with better quality. Parts are designed for ease of fabrication and commonality with other designs. DFM encourages standardisation of parts, maximum use of purchased parts, modular design, and standard design features. Designers will save time and money by not having to “re-invent the wheel.” The result is a broader product line that is responsive to customer needs. Companies that have applied DFM have realised substantial benefits. Costs and time-to-market are often cut in half with significant improvements in quality, reliability, serviceability, product line breadth, delivery, customer acceptance and, in general, competitive posture.
Bio:
Roxann Dawson MCQI CQP is the Senior Quality Manager for Costain. Roxann is responsible for ensuring the implementation and delivery of the Quality Management System and ensure customer satisfaction is achieved.
A proven Quality Professional , Roxann’s experience extends across a broad spectrum of disciplines encompassing Communications, Control Systems, Quality Assurance (QA), HSQE, performance management and including, establishing a fully compliant ISO 9001:2008 Quality Management System (QMS) for project delivery.
Her experience is complemented by her drive to embed quality behaviours into business operations through a combination of leadership, role modelling and local coaching specific to team and project requirements.
That’s a good point that having bad parts would lead to a bad product. I feel like making sure that each part is made correctly would be a good way to ensure that your quality standards are being met. I’ll have to consider getting someone to help me ensure part quality if I decide to start a business.
Most procurement seems to focus on delivery and cost. In reality, the biggest challenge is supplier designs and quality of delivered products. We believe the future of procurement is supply chain risk management. If you’d like we can share a power point deck with you. Just email us at gregh@europa.com