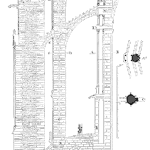
Your skilled maintenance trades are a valuable resource that is often squandered by poor management and a lack of proactive approach to the maintenance of industrial assets.
This article by RBC’s Thought Leadership group on Human Capital describes a problem that many of our industrial customers are dealing with.
There are two possible solutions that they’ve missed when it comes to skilled trades in the area of maintenance – better planning and scheduling, and improved asset reliability programs.
Planning and Scheduling – in maintenance circles the rule of thumb is that a fully planned job executed on schedule will require about 1/3 the time of a job that is done without planning and scheduling. I’ve seen that estimate vary from about 1/2 the time to as much as 1/14th the time in one extreme case (underground mining operation).
On its own, planning and scheduling will reduce the wastage of time and increase the “wrench time” or active time on the tools from an average of only 32% to about 52% or higher. That’s a huge boost in productivity and it only requires one planner for about every 20 or so tradespersons.
The ability to stick to a schedule depends on a few factors, one of the most important being the lack of interruptions. In the industrial environment, most interruptions are due to the failure of equipment and systems. Of course, they never fail when they are idle or not needed – they fail when under load and producing. That creates an urgency to get them fixed fast and workers may be taken from other planned and scheduled work to make that happen. It’s unproductive for the job that was now disrupted. Production capacity is lost. And because the failure was unexpected, the planning and scheduling are not done, therefore the job is likely to take long and suffer from a lot of inefficiencies. There is no good news in that scenario.
Planning and scheduling alone don’t contribute to a reduction in those interruptions. That comes from achieving reliable performance. That comes from having what I call a “reliability program”. Many others call it PM or Proactive Maintenance. I like to emphasize reliability because that is what you want. Maintenance is the activity, not the goal.
A good reliability program requires some up-front thinking about failures and failure modes (the events that cause the unexpected interruptions) and decision-making about what you can do proactively to avoid those situations or at least lessen their impact. The method best suited to that is Reliability Centered Maintenance – Re-Engineered. A well-designed reliability program, combined with good planning and scheduling can deliver terrific results for your business while dramatically increasing skilled trades workforce productivity.
Reliability programs that are 20-30% less costly than the maintenance programs they replaced are not uncommon. A spin-off benefit from that is a reduction in use and demand for spare parts. Productivity boosts that almost double the work done by your existing workforce and reduces the demand for more skilled trades hiring is another major benefit. Finally, your producing assets will run longer at higher outputs, increasing revenues.
In a couple of recent cases, we estimated revenue gains to be as high as 10 times the value of the cost savings that were achievable. Those cases were dealing with high-value and high-margin products, but even with lower value, lower-margin products the revenue gains can easily outweigh the cost savings.
Many industrial operations are leaving a lot of money on the table by reacting only to short-term immediate problems. To learn more about the potential savings and gains for your business talk to us. james@consciousasset.com or +1 705 408 0255.
Leave a Reply