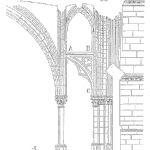
Being the reliability engineer on a project doesn’t have to be a lonely assignment.
Nearly everyone on the team shares the same goal. That of creating a reliable product or maintaining equipment availability.
Other may be electrical or mechanical engineers, technicians, procurement or some other part of the organization, yet they all have something to contribute to improving reliability.
Sometimes you have to find the reliability-minded individuals – to assist when gathering information – to identify potential weaknesses – to provide support for a reliability task – to encourage others to fully consider reliability with each decision
Traits of reliability-minded coworkers
My estimate is approximately half of the working reliability engineers are individuals that showed an interest in reliability. They then learned the skills and tools associated with reliability engineering.
It is that interest that we are seeking. It is that interest that aligns with improving reliability and learning.
In conversations, in meetings, and during presentations pay attention to the focus, ideas, and questions of your coworkers. In one or more ways they will reveal their interest in reliability.
Look for those asking questions about
- risks of failure
- failure mechanisms
- design options to make the product more robust
- vendor selection including component reliability
Of course, there are others, yet this short list may provide just the tip to let you encourage more such questions.
What to look for:
Look for meeting participants that
- tend to focus on the durability of the product for the end user
- tend to ask reliability related questions
- tend to join discussions about failure mechanisms
- tend to get engaged when reliability is the discussion topic
During presentations look for speakers that
- lead the presentation with reliability goals or measures
- includes sections of potential failure modes
- discusses risks to the durability of the product
- encourages discussion of reliability improvements
The basic idea is to listen and encourage discussions around reliability. This may include design, assembly, operations, suppliers, budgeting, and customer feedback situations.
Whenever the discussion turns to reliability, you should pay attention to who started it and who’s engaged. These people are you potential reliability champions.
How did you start in reliability? Did someone encourage you based on your interest? That was my path.
Related:
To Change the Reliability Culture (article)
Role of Reliability in an Organization (article)
Look for those asking questions about
• How do we perform failure analysis as a formal team?
• Ask about the design of the failure analytic and how we are pulling the bad actor report
• Do we know which assets and systems have the highest business risk exposure?
• Are we capturing failures modes on the work orders?
• Ae we updating the RCM analyses that exist, as needed?
• Are we capturing O&M tech feedback such as maintainability issues, ergonomic, safety/hazard, design flaws, PM adjustments?
• Are we performing defect elimination? Why not?
• Is the warehouse properly cataloged so that we can find things?
• Are vendors working with us to remedy maintenance issues?
Look for “reliability leaders” that desire to leverage failure data from the CMMS.
Do we have staff certified in reliability? Is management encouraging that knowledge base?
Do we have a long range plan towards excellence?
ALIGN – ENGAGE — EMPOWER
Well said John, thanks, Fred