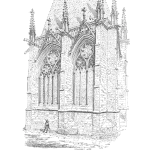
Guest post by B.D. McLaughlin, ScD, MInstrP
Using a comprehensive and inclusive definition, risk may be defined as the cost of “failure to add value” per unit time. Such failure includes performance deficiencies for employees, equipment, material and method. It includes the types of “failure to add value” comprising traditional waste such as overproduction, wait time, transportation, processing, inventory, motion and defects. It includes the cost of injury, litigation and damage to company reputation. It encompasses the total cost of failure and not just the cost of remediation. You must minimize risk to stay competitive. Risk is consuming the hidden wealth of your enterprise. It is disguised and concealed as the “cost of doing business.”
Consider a manufacturing plant for example. Risk Abatement is an Essential Objective during all Pre-operational Phases from Design through Construction. After construction is complete and the plant is commissioned, that phase of the Life Cycle called “Operation and Maintenance” begins. The objective of traditional maintenance is to “prevent all equipment breakdown having serious consequences.” This narrow scope for traditional maintenance ignores the consequences of performance deficiencies for employees, materials and methods. It ignores the types of failure to add value comprising overproduction, wait time, transportation, processing, inventory, motion and defects. It ignores the cost of injury, litigation and damage to company reputation. Furthermore, these omitted types of “failure to add value” are generally not effectively addressed in any department because of restrictive organizational structures. Therefore, strategic maintenance planning, in the Factory of the Future, must embrace a new objective: Remove “Failure to Add Value” From All Aspects of the Value Stream. Strategic maintenance planning, in the Factory of the Future, should comprise Comprehensive Risk Abatement.
A world class comprehensive risk abatement strategy should be applicable to any aspect of any business. While details of application may differ, the overall objectives and process should remain unchanged. For example, the strategy should be compatible with ISO certification. The established concepts of ISO tell the organization “what” needs to be done but not specifically “how” to do it. For the “how,” practitioners must choose from a smorgasbord of Analytical and Maintenance Procedures. But four critical questions must always be asked:
- What are the enterprise wide common objectives that should be achievable by any completely effective set of Analytical and Maintenance Procedures?
- How can a complementary set of Analytical and Maintenance Procedures be selected so that each provides critical information lacking in the others?
- How can a complementary set of Analytical and Maintenance Procedures be systematically integrated to achieve balanced progress toward common objectives?
- How can the links between process and objectives be evaluated to ensure that the chosen set of Analytical and Maintenance Procedures is capable of satisfying the objectives?
A world class strategy answers these questions by:
- Defining specific and comprehensive objectives.
- Providing drill-down levels of analysis facilitating the selection of complementary procedures appropriate for each level.
- Creating an Analytical and Maintenance Procedure integration process for achieving balanced progress toward common objectives (Matrix Management of Risk Abatement).
- Testing for symmetry within the lines of communication between process and objectives.
The 1st bullet item pertains to enterprise wide common risk abatement objectives. The 2nd and 3rd bullet items focus on the risk abatement process. The 4th bullet item connects the process to the objectives.
Many objectives have been tried and found wanting. Maintaining system function but not individual component function is a cornerstone of Reliability Centered Maintenance. However, RCM works well only in very structured strictly controlled industries (e.g. nuclear power and aircraft). Six Sigma focuses on defining project specific objectives, extensive statistical analysis and Change Control Boards. In many cases, however, more attention is paid to reducing variation than to developing robustness which can reduce the impact of variation. Here is a list of enterprise wide objectives, under the acronym FORTUNE, applicable to any aspect of any business:
- Fix problems not symptoms.
- Optimize materials selection, equipment performance and value stream flow.
- Remove “failure to add value” from all aspects of the value stream.
- Target excellence, Tolerate only small variation and Test continuously to achieve an Accuracy Controlled Enterprise.
- Utilize Predictive Maintenance (condition monitoring) with Precision Principles.
- Numerate progress using the six steps of IONICS for tracking (Identify risks, Order by importance, Numerate options, Introduce solutions, Control processes and Synthesize new ideas)
- Exhume hidden wealth from your enterprise.
The designed overlap and comprehensive depth associated with these objectives guarantees removal of “failure to add value.” But what about the risk abatement process used to achieve these objectives. One such process is Matrix Management of Risk Abatement.
Practitioners of process improvement, asset management, quality control, risk abatement and reliability optimization frequently combine multiple analytical and maintenance procedures because engineers, managers and health care professionals have not embraced a single procedure to cover all issues. The most prominent example is the combination of Lean and Six Sigma. Several other analytical procedures (TPM, P-M Analysis, TOC, TQM, ACE 3T QMS, PEW) and a variety of maintenance methodologies are also combined in various ways. But how can different analytical and maintenance procedures be systematically selected and then integrated to achieve balanced progress toward a common goal?
The matrix integration process starts with the overall Value Stream Map and drills down, with increasing magnification, through successive levels (map, individual map activities, resources within each activity and components within each resource) for a coordinated four level attack on risk. Appropriate analytical
and maintenance procedures are selected for each level. The selection of procedures is generally unconstrained and several procedures can be combined at a given level of analysis. For example, a procedure called “Flash of Genius, Innovation, Creativity and Insight” can be included at each level. This accelerates the process of meeting objectives by sidestepping tedious analysis and plodding, incremental changes whenever possible. However, the procedures should have a common objective such as “failure elimination” as opposed to “achieving acceptable failure rates.” Otherwise a disunity of purpose will confuse the integration process.
Finally, the process must be connected to the objectives in such a way as to ensure that the chosen set of Analytical and Maintenance Procedures, working in and through the process, is capable of satisfying the objectives. One way is to connect the four risk matrix levels to the four central objectives of FORTUNE and periodically check for symmetry in these lines of communication.
Strategic maintenance planning, in the Enterprise of the Future, should comprise Comprehensive Risk Abatement which should, in turn, include objectives, process, a balanced progress methodology and recognized Analytical and Maintenance Procedures. How much wealth are you willing to absorb under the “cost of doing business?”
B. D. McLaughlin, ScD, MInstP
Leave a Reply