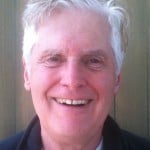
Guest Post by Greg Hutchins (first posted on CERM ® RISK INSIGHTS – reposted here with permission)
The idea of supply chain risk management has been around for about 10 years. It is only in the last 5 years, that it has become popular. We are still at the early stage of supply chain risk management adoption and deployment.
In terms of total dollar amount, external suppliers provide a significant portion of a manufacturer’s product. For U.S. firms, 50% to 80% or more of the final price of a product can be the cost of purchased goods. In Japan, it can be even higher.
For these reasons, any supply disruption can kill a supply chain. As a result, supply chain risk management is now critical to a company’s competitiveness.
SUPPLY CHAIN RISK MANAGEMENT SHIFTS
Supply Chain Risk Management has grown in importance due to the following trends:
- Emphasis on good governance, risk management, and compliance.
- Reporting of risk and materiality issues to the Board of Directors, investment community, and regulators.
- Focus on Enterprise Risk Management ERM within the organization and into the extended organization involving suppliers.
- Emphasis on risk based, problem solving and risk based, decision making.
- Focus on integrating operational and supply chain core competencies with the strategic direction of the organizatIon.
- Increased competition from companies moving from delivering products and services to assuring capable and stable processes to developing innovative, digital business models.
- Enhanced innovation and continuous improvement throughout the organization and in the supply chain. In critical performance areas, including build to order, process capability, product quality, product delivery, cycle time reduction, service improvement, and enterprise risk management.
- Ongoing emphasis to provide integrated system solutions not only provide quality products.
- Intense worldwide competition pressures to reduce overall supply chain costs, innovate, and manage risks.
- Strong leadership commitment, supplier involvement, quality at the source, and continuous improvement throughout the chain are key performance indicators
- Standardization throughout the value chain to ensure consistency, such as simultaneous design, lean manufacturing processes, mistake proofing, total productive maintenance and collaborative teams
- Streamlined and uninterrupted flow of material through the process chain to support cell manufacturing, pull/push production techniques, flexible operations, simplification, rapid machine/process changeover, and customer-supply development.
- Continuous elimination of waste, simplification, and redundancy is a priority across the value chain
- Supply chain information requirements must be understood and exchanged with supply-partners.
WHERE TO FIND SUPPLY CHAIN RISK MANAGEMENT EDUCATION?
Most colleges are developing risk certificate programs. As well, you may want to check out our Certified Enterprise Risk Management(R) certificate program.
Leave a Reply