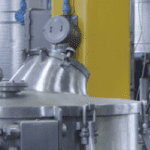
Welcome to part seven of my 10-part series of blogs called “Uptime Insights”, where we explore a journey of excellence in maintenance. To stay on top, managers must implement strategies that keep operations performing at high levels. In these articles I will show you how to achieve excellence in maintenance – a critical business process in any capital intensive industry.
Uptime Insights Part Seven:
Support Systems Improve Efficiency
Computerized systems are important and now seemingly indispensable tools for business. Just remember the last power failure you experienced and you’ll understand. There isn’t much that isn’t computerized these days. Technology and its business applications continue to grow and proliferate. The world of maintenance is no exception. Most maintenance work is not computerized, but it is complex and managing it requires sophisticated tools. Using those tools effectively will improve the efficiency with which you deliver maintenance services. Use them poorly and you only add cost.
There are two broad categories of technology that maintainers work with: support systems and management information systems.
The first category includes the various specialized support systems for data gathering, processing, analysis and decision-making support. These tools are meant to help today’s knowledge workers, your maintenance technicians and engineers, do their jobs efficiently and more effectively. They are used to monitor equipment condition, analyze equipment performance trends, analyze failure history data, perform complex reliability calculations, provide support to equipment replacement decisions, forecast probabilities, etc. They are often designed as stand-alone systems to be used by trained specialists and they seldom integrate seamlessly with management information systems. These tools, in the right hands can produce remarkable results and quickly earn a return on your investment.
The second category includes the various management information systems: computerized maintenance management systems, enterprise asset management systems and enterprise resource planning systems. These systems automate business processes and information flows associated with a variety of business transactions. In maintenance these systems use the Work Order as their primary transaction document. These systems can produce management reports, schedules and plans from which it is possible to see trends in performance measures and then to make management decisions. They support management processes. They are expensive to acquire, install, implement and operate. They can take months or even years to get going, however, when coupled with business process re-design, the implementation of effective maintenance, inventory and supply chain processes they can add a great deal of value.
In all these systems there is constant development and expansion of capability. The single purpose systems and simpler forms of management systems tend to be easier to use. The broader the capability and the greater the functionality encompassed in these systems the more difficult they tend to be to use. The suppliers of these systems are working hard to change that. One development is the emergence of standards for data interchange using internet architectures that would permit multiple systems, each having different purposes, to share data. This opens up the possibility for specialized decision support systems to gather needed data from management systems and vice versa.
The world of maintenance support and management systems is complex and crowded with competing products. Explore what you really need to achieve, define how systems can help and keep the choices as simple as you can. It will all change again tomorrow!
In our next blog we’ll explore part eight of our 10 part series “Uptime Insights: Managing Failures Before They Occur.”
To learn more visit Conscious Asset where you will find training, workshops, books, and resources.
Related
Uptime: Strategies for Excellence in Maintenance Management (book)
Leave a Reply