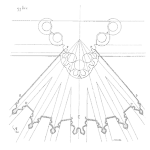
Good physical asset management is about making sure our physical assets do what we want them to do at optimum operating cost and tolerable levels of risk to safety, our environment and to your business.
Managing physical assets to achieve that in an industrial setting involves much more than simply buying and running a piece of equipment.
It will probably last a long time and suffer breakdowns that require repair. Of course a more reliable design will suffer fewer failures and be more available to do its work. Doing all this successfully involves good engineering, maintenance, operation and information management. It is management of those physical assets and all that accompanies them to deliver sustained value to your business – after all, that’s what you invest good capital funding to provide. We call getting it all right so that there are “no surprises” good Capital Asset Management™.
Engineering a new system isn’t enough for success. Engineers do a good technical job at design but they don’t always have a lot of operational experience to guide their thinking about what can go wrong. Making sure it is a reliable design requires insight from operations and maintenance to be included during the early stages of design and choosing your equipment. A team is needed including designers, maintainers and operators to do this well.
Once commissioned, your new system will be In-service. The new machines will need maintenance to prevent breakdowns, some predictive checks to catch those failure mechanisms that can’t be prevented and diligent operation to avoid overloading and overstressing. Most industrial machines are complicated and there are many ways they can break down. Forecasting those potential breakdowns allows us to do a better job of avoiding, preventing and predicting them so we can manage our maintenance to proactively keep the machine running well instead of reactively fixing it when it breaks.
We can trust our ability to learn as we go. We could observe failures in service and take steps to avoid having them occur again. But that is reactive and risky. It means we will have a few nasty surprises before we take steps to mitigate their effects. Alternatively, and preferably, we can predict those failures at the design stage and avoid most, if not all, of those nasty surprises. This proactive approach costs a bit more at the design stage, but it pays big dividends in terms of reliable and more consistent operation. The cost is as little as 2 or 3% of the cost of the system itself and the payback can be measured in multiples of the capital cost over the life of the system. Any smart investor would take those odds!
Of course more reliable operation is also safer and more environmentally friendly. Reliability is better for your people and it is socially responsible. If your systems are not breaking down the people who most often suffer injuries (your maintainers and operators) are exposed to fewer risks due to exposed process fluids, broken machinery components, slips, trips and falls. If you contain your fluids and emissions remain within allowable limits you will avoid fines and possible orders to shut down. A more reliable operation has less output variability and is more predictable. Insurers and lenders like that because their risks are also reduced.
We get that payback by influencing the design before we invest extensively in its construction and by preparing our organization for its operation. We do that by learning how the system will work, how it should be operated, how it can fail and what to do about it. This knowledge helps us reduce risks and costs throughout the operational “life” of the asset.
Knowing what actions we will take enables us to plan for the future. We identify future work (repairs or preventive actions). Planned work is always cheaper than work that is unplanned. We can prepare training for our maintainers and operators that is specific to our system. When they know what to do and how to do it, they are better at doing it – risks are reduced. If our training programs don’t already cater to those new training needs we can upgrade them and the training facilities if needed, in time for our crews to be ready for when the system enters service.
The plans we generate also identify parts, tools and other requirements for work to be carried out. We also know how often we will need to do it so we can acquire spare parts (and other needs) in the right quantities and at the right time for their eventual use. This helps us avoid overspending on parts we don’t need and ensures we have exactly what we need at the right time.
Throughout all of this we are using information and managing it. We are making sure that our design ideas and changes to them are full recorded and reflected in the training, in the parts we stock, the operating procedures and the maintenance programs we develop. We keep the “information plant” in step with the “physical plant” and reduce the risk of mistakes years later.
We’ve described this whole concept of Capital Asset Management™ in depth in our new book, “No Surprises”. By Uri Wittenberg and James Reyes-Picknell
In this blog, asset management is simplified with practical insights making it easier for organizations to navigate challenges and improve reliability without unexpected surprises.