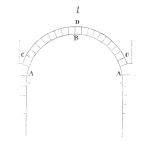
In Part 1 of this article series, we described validation engineering as the process of validating, monitoring and execution of product requirements to ensure customer needs are met. The validation engineer is the validation process owner and works with subject matter experts to develop complete, accurate and testable requirements.
We proposed the following “V” diagram which illustrates the requirements validation and allocation as well as the corresponding integration and testing at each level:
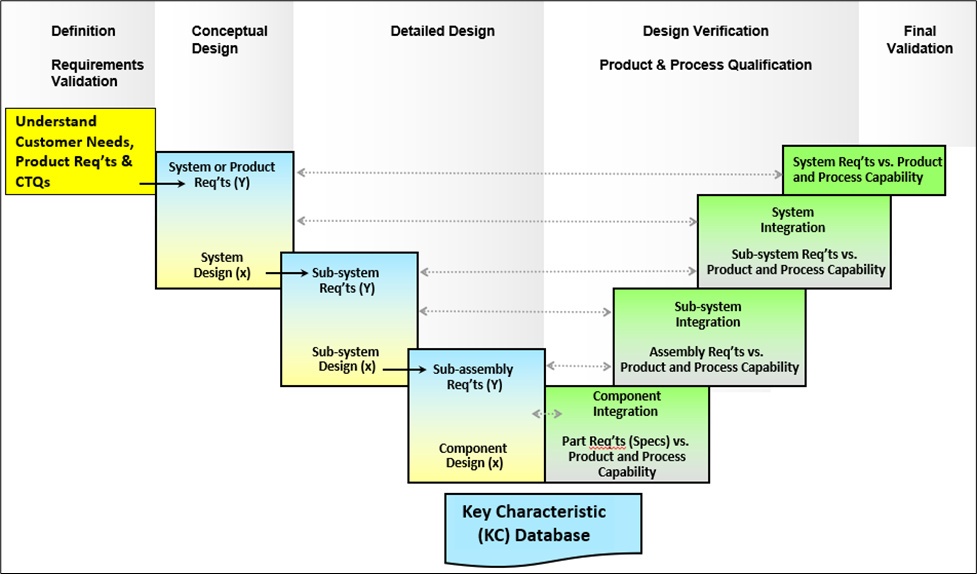
In this article, we will focus on the left leg of the “V”, where product requirements (including reliability requirements) are ultimately established and allocated down to component level specification or requirements. The specs/requirements that have the greatest impact on product performance are Key Characteristics (KCs) and for reliability, Critical to Reliability (CTR).
Pro-active identification of Key Characteristics and Critical to Reliability Characteristics enable robust design, and focus on the most important design parameters and components.
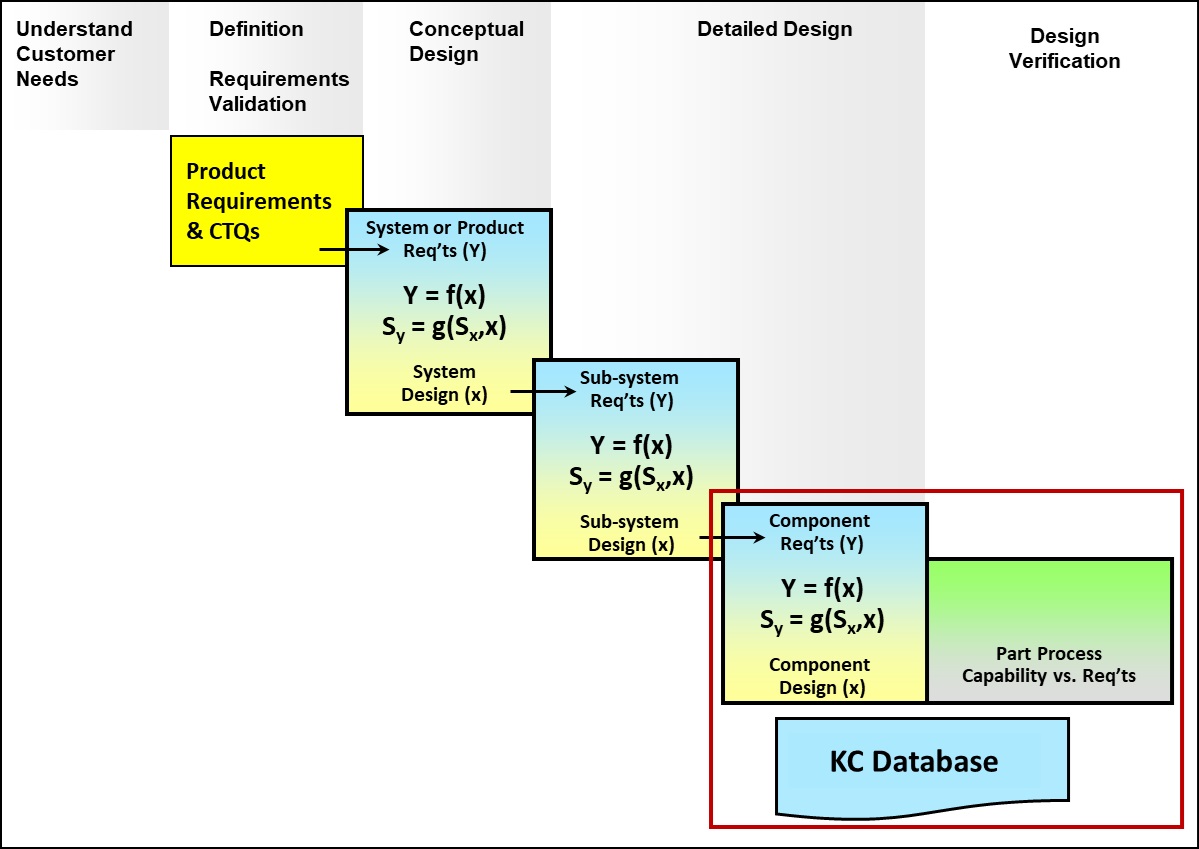
At this point in the development of the product, we have completed the modeling and analysis of our detailed design. Notice on this graphic we added the transfer functions Y = f(x) where Y = the functional output based on a design parameter(s) and Sy = g(Sx, x) is the variation of the functional output based on the variation in the design parameter.
A design parameter might be, for example, a diameter of a shaft or the resistance of a resistor in a printed circuit board assembly. Therefore, a key characteristic is a design parameter (mean and variability) which most significantly impacts product performance. A sensitivity analysis (such as a Monte Carlo analysis) would reveal which design parameters have the greatest impact on product performance. Reliability modeling can perform a similar function.
This information can be used to mitigate hardware product development as follows:
Recommendation | Enabled by: | Risk (if not performed) |
Identify key and critical to reliability characteristics establish a KC and CTR database. Start measuring process capability for key characteristics and verify reliability of critical to reliability components | Validation Engineer and Design Team – sensitivity modeling and analysis. Operations – process capability data, statistical process control (SPC) | A failure or defect could be identified later in the product integration or verification testing. Improvements to the process capability of the manufacturing process, or identification and qualification of an alternate source for the component may be required. |
Establish your control plan as KCs, CTRs, and factors affecting process capability, are identified | Operations – process capability data, SPC and analysis of factors affecting process capability | No control plan. Poor process capability would require troubleshooting, design of experiments, etc. and potentially disrupt volume production. |
Key characteristics and critical to reliability databases should be possible with modern design and analysis tools and manufacturing information systems. In the scenario by which a product is developed, pro-active determination of KCs and CTRs, process capability and control plans would significantly reduce risk of defect discovery in integration, verification and reliability testing.
Leave a Reply