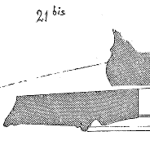
A plan is a road map toward a destination. It provide guidance toward a goal. The idea of a plan is to consider the path forward, the knowledge necessary to acquire, and the decisions along the way.
No plan is perfect other than those that successfully accommodate the successes and setbacks along the way. No plan can anticipate all the information yet to be uncovered, yet it can set a course to deliberately uncover what is necessary to move forward.
There is no one plan that will work within your organization. There is a framework to guide your plan development and adjustments along the way. What worked for your previous project will not quite work for the next one. Every situation and challenge is unique, thus every plan has to be unique.
Reliability Plan and Decisions
A reliability plan assists the people in your organization to make better decisions that result in creating a reliable product the meets your customs and your business objectives. A plan provides a roadmap for your team to know what is the objective what are the hurdles in knowledge or understanding that may prevent the achievement of those objectives. A well crafted plan sets out specific tasks to address the creation of the specific information that enables the entire team to make appropriate decisions resulting in a reliable product.
The essence of a reliablity plan is to incorporate the reliablity vision, understand the gaps, and provide a robust set of tasks that allow a team to set a goal, understand and learn along the way as they adjust to the available information as they consider the many priorities, including reliability performance.
Keep in mind that a plan does not create a reliable product – it is the thousands of decisions that occur during the creation of a product, from concept through manufacturing, shipping, and installation. Reliability is built-in primarily during the design phase by all the decisions concerning design concept, component selection, material selection, etc. These decisions are not all laid out in the reliability plan, yet the plan can influence all of the decisions across an organization that impact reliability performance.
Stay Flexible
Another key concept is a plan is not a fixed object once created. It has to bend, flow, or change as the information available, constraints, and uncertainties change. The plan should include reminders to check if the existing plan is the plan that best serves the project at this time. If not, change the plan.
Sometimes, we do not know enough about a new material, so plan to run some experiments to learn how it may fail in our application. The initial plan most likely would not include running accelerated testing, as we would need to know how it fails to design such a test. Sometimes, a key component becomes unavailable, and we start exploring viable options. Plans change.
Another common occurrence is the project changes a set of key requirements, or adds a function, or changes market scope. These changes often signal a change in timeline, material set, or design complexity. Each signals a need to review the reliability plan to insure the plan addresses the new challenges.
The Ongoing Work of Planning
The initial plan does take some work to fully understand the requirements, constraints, capabilities, and more. The plan should focus on the key decisions that require better insights and information.
Furthermore, the plan will change. Plan to change the plan to keep it relevant and focused on what is needed to improve the ability to make better decisions.
The plan may consist of goals, models, specific activities, and guidelines. It is there to guide not only the work of the reliability professional. It is there to guide the work of the extended design and development team.
This is an excellent hint.). My experience is that, in general, Companies expect a to-do-list as much standard as possible. This is doable we need simply assess a product compliance to some standards or requirements, not product reliability.
The switch to this mind set is hard for a couple of reasons: there is the ‘feeling’ the time is too long and the cost too high and , probably, the awareness the not always the available skills are adequate.
Hi Carla, true if the expectations are for the use of standards and it’s quick and easy – it is a mindset issue. Hence the need to focus on what are the key decisions that involve reliability and help the team understand the value of having good information to assist in making those key decisions. cheers, Fred