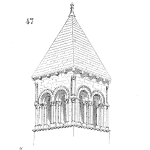
The benefits of proactive maintenance are the avoidance of consequences that occur when something fails. If you knew that you were going to suffer a heart attack and roughly when it would happen, wouldn’t you do something to avoid it? Or maybe you would just prepare better so the consequences of it occurring are minimized.
You can also do that with your plant, installed systems, and equipment. Being proactive is about managing risks and minimizing consequences. A good reliability program, properly executed by your maintenance department achieves that.
A reliability program, comprising mostly of proactive maintenance, delivers maximum uptime for productive purposes. Your machinery, systems, fixed and the mobile plant won’t be reliable if you don’t treat them well. That means taking care of lubrication, cleanliness, basic services, and monitoring their condition. Condition monitoring is an amazingly powerful tool that is often under-utilized. Worse still, some organizations even ignore the warnings that arise.
Being proactive with your assets is all about managing failures before they occur and the consequences of failures. You can reduce or eliminate the consequences of failure by forecasting what is likely to happen and deciding in advance about what to do about it. Some are preventable, but many are not. Even if you can’t prevent them though, you can take steps to avoid the consequences of those failures. For example, take some scheduled downtime to correct the problem before it crashes during a production run.
The advantage of doing this is that major business impacts due to equipment breakdown can be avoided. High-performing companies manage proactively – they foresee and avoid problems. It’s good for business!
Reliability Centered Maintenance (RCM) is the most proven proactive approach for developing proactive maintenance programs from scratch. It is a logical process that can be used during the design stage of an asset’s life cycle or later after the asset has entered service. It uses the knowledge we have of how things fail to arrive at logical decisions for individual asset failure management policies. The intent is to avoid or minimize the consequences of failures. One of the great strengths of RCM is that it does not require failures to have occurred in order to generate data for analysis – it anticipates the most likely failure modes and deals with them and their consequences before the fact. While data is helpful, you can do a very credible job without it. In fact, if you do that good job, you will end up collecting fewer failure data – not a bad situation to be in unless you like to over-analyze.
Programs developed using RCM, provide for the safe minimum amount of appropriate proactive maintenance. These programs provide a balance of cost vs. reliability that is tailored specifically to your assets in your operating environment. The tendency to over-or under-maintain, often a result of using other methods, is avoided.
RCM was developed and first proven in the aircraft industry where reliability really mattered and was quickly adopted for use in nuclear power generation. Today RCM is used in all capital-intensive industries where reliability is important. It is the cornerstone of any reliability improvement program. The most recent version of it is RCM-Re-engineered, created by myself and my co-author, Jesus Sifonte.
RCM (and RCM-R(R)) require careful application of the process and follow-up by implementing the results in your maintenance program. That program must then be followed. There is little point in doing scheduled proactive condition monitoring if you don’t follow up on the findings that will arise.
Many failures of well-run RCM analysis projects have occurred because the outputs of the analysis were not put into practice in the operational environment. That follow-up is critical. Once it is in place, then optimizing that maintenance program is done on a continuous basis.
If you want high reliability at optimum cost, RCM-R(R) is the answer, but even it is not perfect. Some unforeseen failures may still happen and you will want to avoid having them happen again. In those cases, you may want to use Root Cause Analysis to identify what steps to take in the future.
Root Cause Failure Analysis (RCFA) is entirely reactive to failures that have already occurred. RCFA is a method of performing a sort of “post-mortem” to determine what caused any particular failure. The intent is to eliminate the “root cause”, that being the identifiable cause that you can manage in some practical way.
Even RCM programs do tend to go a bit stale over time. Our systems are constantly being used in new ways and subjected to new stresses. They also age through usage. The maintenance program designed for a new asset may not be as good a fit if that asset is now used differently. Its “operating context” has changed and so too should its maintenance.
Preventive Maintenance Review / Optimization (PMR/O) is a method based on RCM logic that is applied to existing maintenance programs in an attempt to optimize them. PMR/O arose out of the need to improve the performance of existing maintenance programs that were now failing to meet desired performance expectations.
Decision optimization techniques and tools help maintainers to make fact-based decisions or to improve on decisions already made. RCM can be used before the asset is put into service (as it is in the aircraft and nuclear industries). In those cases, even the decisions made about task frequencies and failure modes were invariably made with some degree of uncertainty, albeit informed by past experience.
Once the new program is put into place, some failures will arise that were not anticipated. It’s possible that the frequencies of failures differ from what was expected, or the consequences of those failures in the new design are different. Optimization techniques are used to analyze the in-service data to validate or modify the original decisions. These techniques can be very accurate provided the data is accurate and they are perhaps one of the best approaches for continuously improving on an existing maintenance program. Accurate and complete data can be a problem in many industrial environments. To deal with that we also deal with Asset Information Management.
Reliability and simulation modeling are computer-based techniques that allow us to mathematically model the behavior of our installed systems. They can reveal where we have process bottlenecks and if we are working to improve on one bottleneck, where the next ones are likely to arise. These models can also show us the effect of various reliability improvements at different points in the systems and help us focus our engineering efforts more effectively.
There is much we can do to become more proactive and it is all good for business. As Benjamin Franklin once said, “An ounce of prevention is worth a pound of cure”. He was talking about health care at the time, but his statement is also very true when it comes to our physical assets of all sorts and in all industries.
Leave a Reply