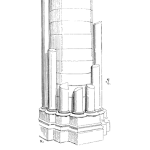
Abstract: Many companies struggle with constant plant and equipment problems despite doing the very best they know how to keep their plant and machinery reliable. Their real problem, which they cannot see for themselves, is that what is done in the company is completely wrong for creating highly reliable production equipment. If you cannot “see” how reliability is destroyed in your business, then you are doomed to suffer poor reliability and low uptime forevermore.
Keywords: reliability creation, equipment failure
Most industrial businesses make their equipment fail. Misunderstanding risk, variation and probability leads managers and engineers to use processes that cause trouble. An analysis of a real business illustrates the effects of this all-too-common management error. Figure 1 is a run chart of a company’s total breakdown hours per week over 16 weeks. If the graph is representative of normal operation, the time series can be taken as a sample of the company’s typical businessperformance. Important information about the company’s operations is exposed by using two basic statistical analyses on the data: a frequency distribution, and a control chart.
The frequency of total downtime hours each week due to breakdowns is plotted in Figure 2. The distribution is twin peaked, with the lower portion looking like a normal bell curve but suddenly there is a discontinuity between it and the higher breakdown hour weeks. This company has two types of breakdowns—the normal and the catastrophic.
For the run chart, the average breakdown hours per week are 38 hours. The standard deviation is 18 hours. The upper control limit is 92 hours. The lower control limit is 0. These control lines are shown in Figure 1. Because all data points are within the statistical boundaries, the analysis indicates that breakdowns are common to the business processes and not caused by outside influences. This company has a statistically stable system for making its equipment break down. Breakdowns are one of the “products” made every week.
Because the breakdown creation process is stable, the future generation of breakdowns is predictable and certain. If this time series is a true sample of normal operation, it can confidently be said that there will always be an average of 38 hours lost to breakdowns every week in this business. In the three weeks following the 16-week period represented, the “normal” weekly breakdown hours were 25, 8, and 25 hours, respectively. This business has built breakdowns into the way it operates because the process of breakdown manufacture is part of the way the company works. The only way to stop the breakdowns is to change to processes that prevent breakdowns.
Figure 3 shows you a workshop in a company that makes its machines breakdown. In the image is listed a few examples of how the company’s maintenance and repair processes are making their plant and equipment fail. There are many obvious causes of future reliability problems and equipment failures when you know what to look for. But the biggest problems in the company are those that you cannot see, which are causing all those troubles that you can see. The people in the maintenance group, from shopfloor to upper management, do not understand that it is their own methods, practices and standards that are causing many of their equipment failures and problems. They cannot “see” that much of what they do will make their machines fail.
The physical evidence in the photo screams at you that company has many business process failures and weaknesses that initiate, allow and encourage their production plant problems. Troubles exist with employee selection, skills development and training, maintenance work quality assurance, equipment rebuild practices and techniques, quality system auditing, crew supervision—and there will be numerous other process problems as well.
How many other bad practice related reliability and safety problems can you see in the photo? What good and proper practices that should be used are not in evidence? What about the “hidden” business process related causes of future reliability problems—how many more process design issues can you “see” in Figure 3?
What if you went to your company’s own workshop—how many causes of your own business process, plant and production failures will you find right in front of you?
Mike Sondalini
Director
Leave a Reply