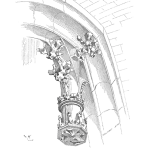
Abstract: Do the reliability math on organizational structure design, and in a militaristic silo configuration you’ll see that managers have a huge influence on their departments performance. But what is most surprising is that supervisors in silo groups have more than double their manager’s impact on their group’s success. Managers making poor and wrong choices will cause serious trouble. But supervisors who get decisions wrong cause catastrophe.
Keywords: teams, teamwork, organizational design, department structure
Great managers and supervisors are not born great, they become great through experience, experimentation, and gumption. We all get better at what we do as we do it. You learn to refine your work through observation of cause and effect and learning what works best. Gradually you become both more efficient at doing your work, and more effective when doing it.
For managers and supervisors in silo organizations it’s especially important that they are only appointed to those roles when they have mastered their duties. When you do the reliability math on silo organizations you discover just how important good managers are to a business. But the greatest discovery is to see how vital it is to have highly competent supervisors.
The extract below on the reliability of teamwork design is from our book, Industrial and Manufacturing Wellness. It’s available at the Industrial Press website and also at Amazon books.
How reliable is a cross-functional team structure compared with a militaristic structure in doing the work? The answer is critically important to an organization that is looking to be more successful. We need to compare the reliability of the silo structure with that of the team structure and see what difference there is. Figure 1 shows the silo structure drawn as a functional block diagram, assuming that work is passed from one operator to the next in the work process.
For the sake of the example, assume that the people are working in a complicated industrial process without strict quality control. They make 10 errors in every 100 opportunities, which means that 90 in every 100 opportunities are done right—a 0.9 probability of doing an activity correctly. An indicator of defect rate is the number of standard deviations of the result from the ideal, also called
its sigma level. As the frequency of defects reduce the results that are defects become less probable and their sigma value increases to show the events are becoming uncommon outliers of the range of expected results. If shown on the quality characteristic’s distribution curve, the result is at one or other extremity of the curve, indicating it does not happen as often is the more common outcomes. For 10 errors in 100 results the failure rate is about 2.5-sigma quality (3-sigma quality would be 7 errors per 100 opportunities and 4-sigma would be 0.6 errors for 100 opportunities1). The chance of success for the whole militaristic process can now be analyzed. Starting with the three individuals working alone, the reliability of a group’s work process is calculated as follows:
R = RS1P1 x RS1P2 x RS1P3 = 0.9 x 0.9 x 0.9 = 0.729
With a supervisor in parallel arrangement to oversee the group, each group’s reliability becomes,
R = 1 – [(1 – 0.729) x (1 – 0.9)] = 1 – [(0.271) x (0.1)] = 1 – [0.0271] = 0.9729
The supervisor’s activity paralleled to the workers’ activities lifts the group’s performance. The three groups in the department are sequentially feeding work to the others producing a series reliability expressed as follows:
R = 0.9729 x 0.9729 x 0.9729 = 0.921
With the manager placed in parallel to manage the operation, the department reliability is,
R = 1 – [(1 – 0.921) x (1 – 0.9)] = 1 – [(0.079) x (0.1)] = 1 – [0.0079] = 0.992
The department has a theoretical reliability of 0.99, or 1 error in every 100 opportunities—nearly 4-sigma quality. Yet industrial organizations that produce 4-sigma performance in their operations and workshops are rare. Businesses without a quality control system produce outcomes typically around 2.5 sigma.2 Those with a working quality system can be 3 to 3.5 sigma. The assumption of 90% reliability for people doing uncontrolled tasks is too high because the calculated results do not happen in reality. Let us repeat the calculations with a task reliability of 70% for each individual—2-sigma quality, or 30 errors in every 100 opportunities.
For the individual workers doing series steps, the reliability of their process is as follows:
R = 0.7 x 0.7 x 0.7 = 0.343
With a supervisor paralleled to oversee the work, each silo group reliability becomes,
R = 1 – [(1 – 0.343) x (1 – 0.7)] = 1 – [0.197] = 0.803
The three work groups have the following series reliability:
R = 0.803 x 0.803 x 0.803 = 0.518
Placing the manager in parallel over the operation, the department reliability is,
R = 1 – [(1 – 0.518) x (1 – 0.7)] = 1 – [0.145] = 0.855 (about 2.5-sigma quality)
The department output is now 2.5-sigma quality, which is what is expected from a typical business without an inspiring quality system. The difference in results using different error rates warns us that poor departmental performance is the accumulated effect of poor individual task performance.
One troubling aspect of the silo organizational structure is that the manager improves department performance by 65%, and the supervisor improves stand-alone workers’ results by 134%. The results from the silo organizations seem to depend on how knowledgeable the supervisors and managers are, and whether they can effectively use their peoples’ efforts. The manager and supervisor are key to the success of the silo structure, and if their mistake rate is high, the business suffers badly from their many errors. A militaristic structure is fraught with many risks of failure, as great managers and supervisors are few in number.
Figure 2 shows a block diagram of the people from the silo structure reconfigured as a team structure. The team puts people in a parallel arrangement. Each team is responsible for a process, and each person works with 0.7 task reliability. The supervisors disappear and become team players who coach the workers, and the manager parallels the teams in the department and works with them to help them succeed. There is no supervisory position in the team, since the team makes its own decisions, the “speaker” role is the team’s representative.
For a team of four people the team reliability is as follows:
R = 1 – [(1 – 0.7) x (1 – 0.7) x (1 – 0.7) x (1 – 0.7)] = 1 – [(0.008)] = 0.992
The groups work in series, feeding their output to the next group. The combined reliability is expressed as follows:
R = 0.992 x 0.992 x 0.992 = 0.976
With the manager (also at 0.7 reliability) included over the teams, the team structure’s reliability is as follows:
R = 1 – [(1 – 0.976) x (1 – 0.7)] = 1 – [(0.007)] = 0.993 (near 4-sigma quality)
With the same people doing work with 0.7 reliability, the silo structure produced 2.5-sigma quality, whereas the team structure delivered 4-sigma quality. The manager improves the silo arrangement by 65% and achieves 0.86 departmental reliability. In a team structure, the manager’s influence on departmental performance is only 2%, but departmental reliability rises to 0.99. It seems that most of the reliability benefits of a team structure are attributable to the team and not to company management.
The modelling of the silo hierarchical organization and the cross-functional team structure in the foregoing calculations do not represent how real organizations actually behave. The examples are constructs for the sake of exploring the effects of each structure on the outcomes of an organization. The investigation indicates that people organized in a team arrangement allow the team to produce better results than putting those same people in a hierarchical structure.
The big assumption is that the people in a team will actually work together as a team to get the benefits of a parallel arrangement of subject matter experts. This requires that all team members and managers have multiple skills and are willing to help each other in a spirit of friendship, trust, respect, learning, and support for the mutual benefit of all.
Organizations with hierarchical structures have the potential to deliver reliable outcomes, but in reality, they perform poorly. Too often in a hierarchical business, the outcomes are wrong. What happens in such organizations to ruin their performance? One possibility is that these companies employ people with variable abilities from a pool of available workers, such as persons from the local community or from those already within the industry. These employees simply do their jobs as best they can. Few are experts in what they do, and so it is likely that errors and defects result from variable work quality. Where there is no work quality control, each person does the work in his or her own way. Because there is no standard accuracy-controlled method, there are a wide range of outcomes, some of which must be wrong because the process allows errors.
There is a lot more information on designing organizations for reliability and robustness in the Industrial and Manufacturing Wellness book, which you can buy from the publisher’s website: Industrial Press. An ebook version is available. It is also at Amazon Books.
My best regards to you,
Mike Sondalini
Director
1 Mike George, Dave Rowlands, and Bill Kastle, What Is Lean Six Sigma? (New York: McGraw-Hill, 2004)
2 Jay Arthur, Lean Six Sigma Demystified (New York: McGraw-Hill, 2007)
Leave a Reply