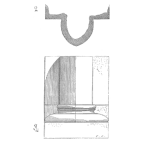
When equipment working parts are operated within their precision quality standard zones, world-class reliability is guaranteed.
The figures below demonstrates the importance of setting precision quality standards to achieve outstanding equipment reliability. It comes from a conference presentation on the production equipment reliability improvement in a steel mill in Australia.
At the time the company was called OneSteel. Its production plant availability was terrible, with only 52% availability. To learn why reliability was so poor, and fix the problems, the company formed a reliability improvement group. The team found that nearly a third of repairs were repeated every month, and nearly half of the repairs re-occurred every three months (Graph 1).
They also identified the two major problems. Firstly, that the quality of equipment components was imprecise. Secondly, the operating conditions were outside design standards. As a result, the machinery was out of balance, suffering high vibration levels, overloaded operations, contaminated lubricants causing particle wear, misaligned shafts, and were operating at high temperatures (Graph 2).
At this time, the standards the company was using for maintenance and were considered tolerable. They were “close enough”. However, the use of these low-quality standards meant that machinery ran well below its designed reliability. Instead of getting 100% of designed life, their machines are getting barely one quarter of the possible reliability.
The improvement team established new higher engineering standards, and new higher operating standards for the mill’s production assets. By doing so they eliminated misalignment and out-of-balance issues, reducing vibration levels. Equipment was operated within the design loads and temperature ranges specified by the machine manufacturers. Lubricants were replaced to prevent contamination and particle wear. The equipment was rebuilt to precision quality standards and run at higher operating quality standards.
Once this was achieved the machinery failure rate dropped dramatically and equipment reliability step-changed up to its designed service duty. The Graph 2 shows there was immediate, huge improvement in reliability. It was not a gradual rise in the equipment reliability—once the precision quality standards were delivered there was a significant change in reliability.
These graphs are real evidence of the necessity for equipment to be built precisely to high engineering quality standards, and to run machinery to high operational standards. High equipment reliability is only possible within the precision quality standards zone where components work together precisely so the equipment runs smoothly. This means that there is no looseness; misalignment does not exist; vibration levels are extremely low; and lubricants have few wear particles and no free water.
Over a 5 to 6-year period OneSteel turned their production plant performance around to reach a plant availability of 77%. Their production throughput increased, and their maintenance costs reduced. All because they moved their equipment maintenance and operation standards into the precision quality standards zone.
Nothing else you do to improve equipment reliability matters until your machines and equipment work and live within the precision quality standards zone—only within the precision zone can you get the utmost operating asset reliability.
Leave a Reply