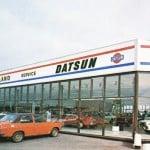
We are all familiar with the base of our car warranties being in both months and miles. Some of that is that they want a definitive end to all warranty periods. But another reason is you can’t just boil down all aging factors to one stress. In a product development program, we are always under pressure to keep all activities as short as possible. Accelerated Life Testing ALT can loose almost all of it’s value when not executed with care.
ALT typically has three distinct phases.
- Select an acceleration stress and corresponding model based on a physics of failure analysis.
- Demonstrate the acceleration factor with a set of runs at three stress levels
- Demonstrate wear-out of product with validated model
- If you truncate the first step you may be executing an ALT test that is accelerating a stress that does not drive the primary wear-out failure mode.
- If you truncate the second step you may be using an acceleration equation that is off by a significant amount; 8 weeks of test converts to 12 years when in fact it only converts to 9 years.
- Everyone does the third step because that is the one that gives the answer of thumbs up, thumbs down that the product can last to spec. But this is now more dangerous than helpful because the gut feel fo the designers on wear-out is going to be more accurate than the test results, and these results will be used to push back on the desinger’s opinion.
So what if there is more than one primary wear-out failure mode based on the variability of use or environment? That means that this entire three-step process may be a six step process.
If you recall I recently purchase a 40 year old car with only 23,000 miles on it, 78 Datsun 280Z. Now 27,000 miles because I drove it from LA to Boston. Today when the warranty period is up in years we aren’t that far behind in mileage, if not having already voided the warranty with mileage.
But this car is such an extreme case, 40 years old and only 2 years worth of mileage. 70’s Japanese cars were made of absolutely horrible alloy steel. The joke is that if you found a Datsun with no rust it was because it was still in the dealer showroom. Now yes this car spent it’s whole life in LA. But there is one corrosion component that is only related to mileage even if you live in a dry area, the exhaust pipe. The exhaust pipe rots from the inside out because the moisture from exhaust gas sits in the pipe and has plenty of heat to get to activation energy. So the exhaust pipe corrosion is directly in correlation to the amount of combustion which translates into mileage pretty well. When I purchased this car I didn’t like the muffler so I changed it before I left. When the mechanic cut the pipe we saw that it was the original exhaust and the cross section of the pipe was about as thick as stock.
But this is what we did experience driving back across country.
Every piece of plastic we touched shattered like glass.
So if back in the design phase the design team wanted to create an ALT for the rubber and plastic increased speed is not a good acceleration factor. But increased UV and temp cycle might be the ticket. So a time-based stress, not miles. If you wanted to do ALT for the exhaust then it may be increased speed of RPM to get the equivalent moisture to react with the metal.
So if the plastics and rubber teams guy used the engine teams acceleration model/test they would end up with a really bad prediction.
I can’t tell you how many times I have seen this in engineering programs. An acceleration test is developed for a product by one discipline and then all other teams use the same model and test regardless if the increased stress is associated with their physics of failure.
Keep an eye out for this. It has lead to many, high expense recalls, excessive warranty claims, and angry customers. Finding out your product, as designed, can’t meet the life goal on a global scale is a horrible day.
-Adam
Leave a Reply