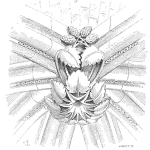
Business processes are often talked about, yet not well understood. The big problem with them is that too few people know what the whole process actually should be. Whenever you are following a set of steps to achieve some goal you are following a process. Sometimes various people follow different steps to achieve the same goal. You rely on processes in order to deliver results. If they are ill-conceived or inefficient, then things move slowly and results are more expensive to obtain than they need to be. Well designed, efficient, and consistent processes that integrate with other related business processes keep things running smoothly, costs down, and help to keep people motivated.
Over time our natural tendency to want to do things “better” causes us to re-design our business processes. We streamline here, add something there, etc., all in an effort to deal with changing circumstances or situations that have arisen or disappeared. Sometimes those changes are for the good, but not everyone follows them or even knows about your changes. Unfortunately, that tendency often results in added complexity, not simplicity. In fact, that is how bureaucracy grows and becomes bloated – just look at any government process and you’ll easily see signs of inefficiency and wastefulness.
Maintenance is a business process and one which we can ill afford to be inefficient. For best performance, it is tightly integrated with materials management, supply chain, human resources, and engineering. If those various “departments” operate independently of each other, or communicate poorly, they will most likely optimize their own results and sometimes (perhaps often) at the expense of others’. If they work together the result is the optimization of the entire business. That entails a degree of compromise and cooperation that is becoming rare in many organizations.
From time to time it makes sense to take a hard look at your maintenance processes, how they integrate with other business processes, and then evaluate whether or not you really need them and all the steps they entail. Sometimes dramatic changes can arise from what is learned in those reviews. If the changes are dramatic they are often called “re-engineering,” but more often the changes are fairly minor – more of a continuous improvement process.
There are a variety of tools used in analyzing process flows: process mapping, process analysis, value stream mapping, visioning, and redesign are all used to help wring more value from business processes. Even when you believe things are running smoothly, there’s a good chance that someone has found a way to improve on the “formal” process and no one else but them knows about it.
In organizations where corporate-wide management systems have been installed, there is a tendency to impose consistent business processes on all parts of the company. In theory, this is great but it fails to take account of the unique circumstances that exist at each location and business unit. Local thinking and methods are often more effective than ideas from elsewhere. Regulations or laws that result in complexity in some processes may be required in one country, but not others where the company operates. Why impose those elsewhere if there is no need or advantage in doing so? For large scale corporate transformations across multiple sites it is best to layout standards and expectations but leave the decisions about execution to the local levels.
While large corporate EAM or ERP systems are wonderful tools for accounting to see what is happening all across the enterprise, they often result in complexities at the local level that are unhelpful and downright inefficient. The result of that is inevitable. Those systems and the way they are implemented result in much higher operating costs in the form of a myriad of minor inefficiencies that add up to big costs. Unfortunately, there is no way to capture those costs and inefficiencies without a formal process re-engineering effort, itself a cost.
Leave a Reply