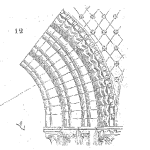
The offered warranty is an internal part of many purchase decisions, plus many business models.
While obligatory to offer a warranty, especially for consumer products, the specific terms, duration, and eventual total cost of honoring warranty claims may vary dramatically.
One key to managing the overall warranty expense is to estimate the potential future warranty claims, followed by accurately tracking actual expenses during the warranty period.
Elements of a warranty claim
Warranty expenses may include
- Call center calls for assistance
- Shipping and handling of returned or replacement items
- Repair center costs
- Spare parts costs
- Service center costs
- Field service costs
Some organizations even include the costs of failure analysis of the returned items.
There is not a definitive list of what is included for financial reporting. Each organization will define what is included or not included in the warranty expense line of reports.
Product failure in the hands of the customer is not the only source of warranty expenses.
It is a significant element, though. When a failure occurs the customer may call or email for support rectifying the issue.
The cost of the failure may include the call, return of the failed item, and the delivery of a replacement item.
These costs occur per field failure.
Yet other costs may occur which are not directly related to a specific field failure.
For example, the call center facility and staffing may have a fixed expense per month which occurs whether or not there are any field failures.
The same for field service or repair centers, the overhead expenses set up and maintain the facilities and staff occur even as the number of field failures may vary.
Creating a meaningful warranty prediction
Forecasting is tricky business, especially about the future.
Yet, we do need some way to estimate expected warranty costs prior to incurring those costs.
A common accounting practice is to accrue funds in anticipation of upcoming expenses.
This accrual practice essential sets aside some funds to cover the expected warranty expenses.
Being able to predict how many failures are likely to occur along with the cost of the relatively fixed warranty costs permits setting aside just enough money and not too much.
Work with your finance team to help them understand the technical risks that may lead to product failure.
A system reliability model built with engineering estimates, test results, and life modeling may provide an expected distribution or probability of failures over time.
The reliability model along with the shipments data permits you to create an estimate of the number of field failures that may occur.
Combine the number of failures with the warranty cost per failure, along with the fixed warranty costs, to determine an overall warranty estimate for a future time period of interest.
A common financial practice to predicting warranty expenses
Not all organizations have an accurate technical (design team developed) system reliability model nor a good idea of the probability of failure for the product.
Thus, many financial teams have little information to forecast warranty expenses based on expected failure rates.
These teams still need to accrue for warranty.
A common practice is to simply use the recent history of warranty expenses, adjust for changes in volume of units to ship in the coming month or quarter, and set that amount aside for warranty expenses.
This is fairly accurate when the product mix and technology, along with customer use and expectations, remain relatively stable.
It’s just a guess for new products, technology, or markets.
With either method, the financial team will adjust the accrual amounts based on recent history and local policy concerning budgeting for warranty expenses.
To see warranty accrual and expense trends for US publicly traded companies visit WarrantyWeek.com.
Eric Arnum reviews financial documents to track and report on warranty accrual and expense patterns. He regularly reports by industry segment and it’s a great way to see how your industry is doing concerning forecasting warranty accurately.
The Warranty CBA Process
The Warranty Cost Benefit Analysis (CBA) must be a well planned, coordinated effort among the program management, contracting, engineering, logistics and cost analysis functional areas.
It should be no surprise that the Warranty CBA process begins with planning. Warranty CBA planning must be done in conjunction with other warranty planning. As with all other aspects of the program, this is the ultimate responsibility of the program manager. Thus, the program manager must assemble or appoint a team of professionals representing the contracting, engineering, logistics, and cost analysis functional areas to perform the Warranty CBA. The program manager must also appoint a Warranty CBA team leader.
Once the team is formed, planning starts with a clear definition and understanding of the objective of the Warranty CBA. Definition includes a knowledge of the time frame in which the analysis must be conducted and the resources available for its execution.
Each team member must then become familiar with the system to be warranted. This familiarization includes a knowledge of the system purpose, its physical and performance characteristics, its configuration, support concept, plan for deployment, and acquisition strategy.
In addition, each team member must be familiar with various warranty types (assurance versus incentive) and, in particular, the warranty or warranties selected for the cost/benefit analysis. The candidate warranties for a particular system are based on the type of system, acquisition strategy, operational scenario, support concept, and essential performance requirements.
Having done the initial planning and having had the plan approved by the program manager, the team is now ready to begin formulation of ground rules and assumptions. Ground rules are generally imposed at the beginning of the process, often by outside sources, while assumptions permit the team to accomplish the analysis in the absence of complete information. These include, but by no means are limited to, cost limitations imposed on the program, program schedule and related time phasing of the estimate, and determination of a base year for the analysis. Adoption of ground rules and assumptions is a continuous and evolving activity throughout the course of the cost/benefit analysis.