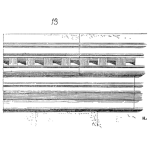
Introduction in ALT:
Accelerated life testing (ALT) is a method used to enhance product reliability by subjecting prototypes to stress levels significantly higher than those encountered in actual use.
By increasing the stress on the component, failure is induced more rapidly, which is equivalent to speeding up the passage of time. This approach is particularly useful when waiting for failures to occur at their normal rate is not feasible, such as when a manufacturer needs to release a product to the market soon and cannot afford to spend several years performing a reliability test.
Accelerated life testing (ALT) is used to determine the relationship between stress and time to failure curves. Time to failure for a device generally correlates with the amount of stress applied, with failure models existing to mathematically define this correlation for various failure mechanisms.
Models in ALT:
Typical models having use in mechanical and electrical engineering:
Arrhenius Model: This model is commonly used in high-temperature aging failure mechanisms to determine the time to failure under specific conditions. It is expressed as:
$$ TTF=C\times e^{\frac{E_{a}}{kT}} $$Where:
- (TTF) = Time to failure
- (C) = Model parameter ((C > 0))
- (Ea) = Activation energy (eV)
- (k) = Boltzmann’s constant ((8.62 \times 10^{-5} eV/K))
- (T) = Temperature (Kelvin)
The Arrhenius model is widely used in the electronics industry for life evaluation and accelerated life testing of electronic components. It is employed to establish a relationship between stress, typically absolute temperature, and the time to failure of electronic components
Power model: The power model is commonly used to calculate fatigue or wear-out in materials. It describes the relationship between stress and time to failure, particularly in the context of fatigue damage accumulation. The power model is expressed as:
$$ TTF=a\times S^{b} $$Where:
- (TTF) = Time to failure
- (S) = Stress level
- (a) and (b) are model parameters
This model is frequently utilized in the analysis of fatigue life and damage accumulation in materials, especially in composite materials and fiber-reinforced plastics. It provides a mathematical framework for understanding how materials degrade over time under cyclic loading conditions, making it a valuable tool in predicting fatigue failure and wear-out behavior in various engineering applications.
Eyring model: The Eyring model is indeed used in mechanical engineering to connect thermal load and stress load predictions, particularly in the context of accelerated life testing and fatigue damage evaluation of mechanical parts. This model is applied to estimate the time to failure under combined temperature and mechanical stress, providing valuable insights into the behavior of materials and components under such conditions. The Eyring model is utilized in the evaluation of fatigue damage of mechanical parts, voltage resistance damage of insulation materials, and power corrosion of semiconductor devices under temperature and mechanical stress. It plays a crucial role in understanding the interactions between vibration and temperature stress in accelerated life testing and in predicting the reliability and robustness of mechanical components under combined stress conditions. Therefore, the Eyring model serves as a valuable tool in mechanical engineering for assessing the effects of thermal and mechanical stress on the performance and durability of various components and materials.
The use of multiple models for critical subcomponents of a product offers several benefits, including enhanced accuracy, robustness, and reliability in predicting the behavior and performance of these subcomponents. Here are some insights from the search results:
Enhanced Accuracy: Using multiple models for critical subcomponents allows for a more comprehensive and accurate assessment of the behavior and performance of these components. Each model can capture different aspects and nuances of the subcomponent’s behavior, leading to a more holistic understanding.
Robustness: Employing multiple models provides a robust framework for evaluating critical subcomponents, as it accounts for various factors and uncertainties. This approach can help mitigate the limitations of individual models and provide a more resilient analysis.
Reliability: By utilizing multiple models, the reliability of predictions and assessments for critical subcomponents is improved. This can be particularly valuable in engineering applications where the performance and longevity of subcomponents are crucial.
Comprehensive Understanding: Employing multiple models allows for a comprehensive understanding of the behavior of critical subcomponents, enabling a more thorough evaluation of their performance under different conditions and stressors.
Risk Mitigation: Using multiple models can help in mitigating risks associated with critical subcomponents by providing a more nuanced and multifaceted analysis, which can aid in making informed decisions and developing effective risk management strategies.
In summary, best outcome of ALT use is as follow: employing multiple models for critical subcomponents of a product can lead to enhanced accuracy, robustness, reliability, a comprehensive understanding, and effective risk mitigation in evaluating the behavior and performance of these subcomponents.
Leave a Reply