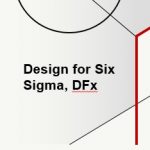
In a previous article, we defined design for six sigma (DFSS) as a thought process focused on maximizing customer value and minimizing cost.
More specifically, DFSS is used to reduce variability in product performance (thereby increasing value), using analytical models and our knowledge of manufacturing variability to enable specification limits on difficult-to-manufacture tolerances to be increased (thereby reducing cost).
Meanwhile, when most people are asked “What is the “x” in DFx?”…a range of answers would be provided (design for assembly, service, procurement, costing, reliability, safety, reuse, etc, etc..). However:
DFx is focused on design-by-analysis, where design performance is modeled, the model is verified and exercised to optimize the design.
While there’s nothing wrong with a design focus area, we don’t want to miss the key points of the “DFx” thought process. Let’s review the thought process as follows:
- Understand Customer Needs
- Define Initial Design Concept
- Model Design Performance
- Optimize the Design (close gaps in modeled design performance)
- Validate Design and Models
- Control (control key x’s that influence customer CTQ’s)
The key questions to be asked, therefore, when developing any new product, new service or even a new business process is: Can the (product, service or process) design be accurately modeled? Can we learn from the model to optimize the design?
Some examples include:
- Matlab/Simulink Models
- Circuit Design Models
- Finite Element Analysis
- Process Maps
- Reliability Models
In summary, the DFx objective is robust, optimized designs through validated models rather than through “design by test” and multiple build cycles. As a result, DFx can significantly reduce design risk and shorten your product (or process) development life cycle. Also, powerful software, analytic, simulation and emulation tools should enable DFx now more than ever.
Leave a Reply