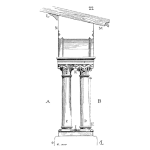
Companies that want plant and equipment reliability need to engage the people in the workplace and give them a large degree of responsibility for improving the performance of their equipment. The most successful solution yet discovered to do that is the autonomous work team.
Keywords: autonomous work teams, self-directed work teams, operator driven reliability
People run organizations and their processes. High operational reliability needs correct practices to be masterly applied in each process of each phase of the life cycle. The production group in an operating plant is an example. They are responsible for running and managing the facility. They know the production process and how to make the products. They can use the equipment to get production. They are accountable for delivering the budgeted operating profit. But do they have the full engineering understanding to operate assets most safely, most reliably, and most profitably? If they have limited design knowledge and mistaken reliability beliefs, they will cause unnecessary failures and waste. Operations groups need the support of cross-functional experts with finance, engineering, and maintenance wisdom to get the best performance from their plant and equipment at the optimal profit. The most successful solution yet discovered to do that is the autonomous work team. Figure 1 shows how the concept developed in the last few decades from the militaristic silo structure prevalent in the 1950’s and 60’s.
The benefits of a team approach to running business activities become clear when you realized that a team is a parallel arrangement of knowledgeable and proficient people. Figure 2 shows the parallel structure that teaming up produces for a pumping system at an industrial site. A maintenance mechanic and an electrician are a part of a team within the operations group. They bring their specialized equipment knowledge and trade skills to the team. Professionally qualified engineers are also appointed to work on the team. The engineers bring their technical knowledge and design understanding. The team gains the engineering skills, experience, and information needed to achieve high reliability. Each team member learns to call on the situational expert for advice and information before making decisions. This does not mean that people move to new job roles or change offices; rather, they are appointed to fill a team function and become team members who work together and develop a team approach to running and caring for plant and equipment.
Something great happens when the team structure and dynamics work. Managers who want higher reliability, top-quality production, and fewer problems need to understand why teams are so powerful and how to gain that power for themselves.
There is a mathematical reason why teams improve the chance of success. A team-based decision cell structure is a probabilistically better design for a business than the militaristic hierarchy structure. Group decisions are more likely to be better choices if the conditions are established to promote mutually beneficial interaction.1 Reliability math offers insights into why and how teams get better outcomes—especially why they are a powerful structure for achieving business goals.
Reliability concepts can be used to design organizational and business department structures. Teaming people together to get greater reliability stems from two parallel reliability principles.
1. The more components are in parallel, the higher the system reliability.
2. The reliability of a parallel arrangement is higher than that of the most reliable component.
The people on a team work collaboratively. When one person is uncertain about a decision, he or she asks other team members for advice. If the team is a mix of subject matter experts, then each person is a knowledgeable resource, and team members help one another work with less chance of error. An example is an autonomous work team composed of operators, maintainers, and quality control staff in a production department. The maintainer can advise the other team members on equipment reliability issues, the operator has experience in using the production equipment, and the quality control staff can advise on the product’s properties. Each member contributes know-how and experience to the decision making processes of the others. Instead of one person working alone, a team has several people guiding each other in their work. The team interaction improves the chance that things will go right more often for everyone.
Once people are paralleled in well-functioning teams, the odds of getting better results rises markedly. Teams bring high success rates to organizations. Teams can help people increase their individual chances of doing outstanding work. They have the ability to greatly improve the odds of delivering correct results the first time. In companies that want high quality, high reliability, and fewer risks, teamwork is far likelier to produce many more favourable outcomes.
Choosing the right organizational structure is vitally important for operational excellence success. Experimentation with autonomous teams by forward-thinking managers has taught us that teams of people with multiple skills, who are willing to help each other in a spirit of friendship, trust, respect, learning, and support for the mutual benefit of all, are far more successful at creating outstanding performance than previous other organizational designs.
All the very best to you,
Mike Sondalini
Director
www.lifetime-reliability.com
1 James Surowiecki, The Wisdom of Crowds: Why the Many Are Smarter than the Few and How Collective Wisdom Shapes Business, Economies, Societies, and Nations (New York: Doubleday, 2004).
Leave a Reply