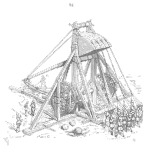
CMMS overview
A proper CMMS (Computerized Maintenance Management System) setup can make a world of difference in an organization’s asset management journey. Conversely, a substandard setup can be a living hell for Reliability Engineers like myself and other analysts. I have personally wasted hundreds of hours of my work life sifting through a poor CMMS structure trying to find records. Ever wanted to make your Reliability Analysts more productive and engaged? If yes, then this article highlights 10 highly recommended set-up requirements.
A CMMS software manages and tracks maintenance activities in organizations. This applies to equipment, machinery, and facilities. CMMS software typically helps with tasks such as scheduling maintenance, tracking work orders, managing inventory and spare parts. It generates maintenance reports and helps to optimize asset management processes. In industry, the CMMS is an indispensable repository of historical records and asset attributes. A “data gold mine” with records added daily and required for asset related studies. Use this gold mine to your advantage by ensuring the following attributes are present.
1 – Cost and expense records
Every task or maintenance work entered in the CMMS should have a cost attached, PERIOD! No work is free. This includes spare parts consumed, labor costs, logistics, vendor fees, etc. Asset Management decisions in “for-profit” organizations are based on minimizing costs. Although there are some notable exceptions such as safety or any regulatory requirements. Therefore, it is indispensable to track and account for every penny in the CMMS.
2 – Equipment commissioning dates
The CMMS should record all equipment start dates. Not having a start date record is like trying to sell a vehicle without knowing its vintage. The lack of this time stamp can greatly impact a Reliability Analysis. This also applies for the replacement of old or obsolete equipment.
3 – Equipment classification (taxonomy)
An equipment taxonomy is a systematic classification of equipment into hierarchical groupings where levels are based on the complexity of equipment characterization. This classification helps group different assets as shown in the Diagram 1 example below. One of the applications of this taxonomy is a “Weibull Library” set-up. This classification is very helpful when doing a reliability study on a specific asset or group of assets. Making the search for records easier and efficient.
4 –Information on failures
This refers to what we call failure modes, causes and effects. Without going into the technical jargon, it is important to obtain as much information on how an asset failed and what caused it to fail. However, this information should be limited to the Reliability Analysis requirements. For example, a pump failed. It would be good to know what subcomponent caused it to fail. Such as a bearing failure or other possible failures as shown in Diagram 2. The failure cause should also be specified here. In this example, the bearing failed due to “normal wear and tear”. This cause can only be based on good judgment. We cannot expect a technician to perform a full investigation on the bearing failure mechanism when they are entering the records. A separate Root Cause Analysis can provide more information if required.
This breakdown into sub component failures (the bearing in our case) is important as it leads to a more rigorous Reliability Analysis. The deeper the Reliability Analysis, the more decisions we can make. For example, in the above example and collected information, we can make a variety of maintenance decisions. Such as pump reliability, bearing reliability, bearing stocking levels, optimum replacement intervals and other maintenance strategies for pumps.
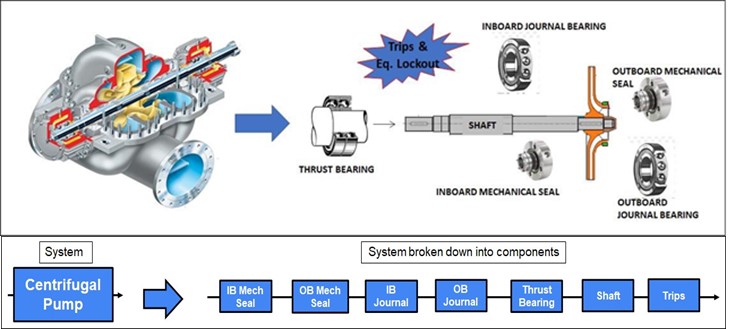
This section is also important for the development of FMEAs. The FMEA analyst will refer to historical records of failures for this exercise. Diagram 2 also highlights the possibility of building a RAM Model when subcomponent information is available.
5 – Repair types
Different remedial actions can happen following a failure. It is important to specify the remedy applied to bring the equipment back to a functional state. This has implications in terms of spending or repair duration. Listed below are examples of potential remedial actions.
- The repair requires and change of part or component. This requires longer “wrench time” and a spare part to be issued from stores leading to an expense in addition to labor costs or other cost (e.g. calling in a vendor).
- Sometimes repairs are minor and don’t require component replacements. This could be adjustments or lubrication amongst others.
- Overhauls are major and expensive repairs. The equipment is at an advanced state of deterioration yet not enough to justify a replacement. The equipment might have to be dissembled and shipped offsite to a specialized shop. This comes with substantial costs.
- Equipment replacements are also expensive exercises and should be recorded.
Any restoration actions in addition to the above mentioned should also be recorded.
6 – Preventive or Predictive maintenance records
In my experience, Preventive Maintenance tasks (PMs) and Conditioned Based Maintenance (CBM) tasks are generally well documented in the CMMS. And should be so as they come at a cost. However, additional tasks conducted during PMs are not well recorded. Sometimes, advanced deterioration is found during an inspection. This leads to an immediate repair. The equipment is already down for PM so there is no disruption to production. However, the repair record is omitted. This can cause errors in the Reliability Analysis. In other words, an omitted repair data point can cause the time to failure to be over estimated.
7 – Repair date stamps
A Reliability Analysis is often based on “time to failure”. However, one can use other ageing variables. Even ageing variables other than calendar time would require a date stamp as a reference. This date stamp has to do with when the equipment failed. It is important to have as precise as possible a record of this failure date. Sometimes, a repair work order comes months after the failure date. Especially if the equipment is not critical to the operation. There is a mix up between work order initiation and failure date. If this happens, it could cause errors in the time to failure calculation and subsequently the Reliability Analysis.
8 – Repair durations
Time to perform a repair is a key attribute in maintenance historical records. The CMMS should record all repair task durations. This repair time can vary substantially depending on the challenges encountered during the exercise. Those could be due to spare part delivery delays or the unavailability of technicians. Repair times can also be classified as follows:
- Diagnosis time
- Wrench time or repair time corresponding to labor hours
- Waiting for spare parts
- Waiting for vendor
- Waiting for technician
And any other relevant category such as start up or re-commissioning time.
Because repair durations vary, they become a random variable. The Reliability Analysis will define it as a statistical distribution. Logging repair time is crucial especially when it comes to labor hours. The latter has a direct cost implication.
9 – Free text entries
A free text section is important for maintenance records. Additional failure or repair information is always useful. This is helpful for various reasons:
- There could be additional valuable information that can only be entered as free text
- Sometimes there are errors in entries. For example, using prepopulated dropdowns, a gasket failure is logged instead of a bearing failure. Having a free text reference can help identify and correct the error.
- New failure modes can appear. When not prepopulated, they can be entered in the free text and flagged by CMMS auditors as new failure modes to be added.
- Lastly, free text can also be very helpful in Root Cause Analysis exercises when seeking specific information about a failure
Entering free text should only be optional. It is important not to overburden technicians with the requirement to systematically enter free text. If at all required, it should be brief, concise and useful.
10 – ISO 14224 Standard
In summary, proper historical records lead to rigorous reliability analysis and effective decision making. The ISO 14224 Standard is an excellent and well-established guide to set up a CMMS data collection and data management structure.
Thank you for this review of ISO 14224 revision. It didn’t know about it. It describes CMMS data that is “nice to have” for reliability analyses and applications. ISO 14224 provokes rebuttal. I will work on it for http://www.accendoreliability.com, but I don’t want to provoke you.
I will send drafts for your review. Does the cost of collecting the data required by ISO 14224 offset the information gained from lifetime data vs. available data? https://sites.google.com/site/fieldreliability/random-tandem-queues-and-reliability-estimation-without-life-data/
Usually I don’t have the data that ISO 14224 calls for and have to do the best I can with available data: revenue and cost data required by GAAP, BoMs, industry publications, user groups that collect data, etc., which provide installed base and failure counts.
Thanks for the feedback Larry as well as reading my article. I did not review ISO 14224 but rather suggested it to be a good basis for garnering the right CMMS Records that will eventually help with a Reliability analysis. I don’t want other reliability engineers to go through the same struggles as I went through.
“Does the cost of collecting the data required by ISO 14224 offset the information gained from lifetime data vs. available data?” – not sure I understand the question.
“Usually I don’t have the data that ISO 14224 calls for and have to do the best I can with available data”. We all have the same issue and this has been my dilemma for years. You get what you get and do your best with it.
I encourage other ideas as well as being challenge so long as we are respectful :-). It benefits everyone. Have a wonderful day!