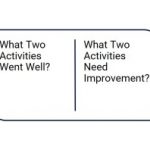
A Simple Q&A Can Reap Improved Performance in Any Activity in Maintenance.
A failure has just occurred on a critical asset in your facility. The result was 2 hours of lost production, but it could have been worse. The last time that the equipment failure occurred it took 5 hours to repair. Why was the failure repaired in less than half the time than the previous occurrence? How can we ensure that we learn from this failure and the team’s performance to improve the plant performance?
I remember reading about a simple philosophy quite a few years ago (although I can’t remember who stated it, so I apologize that I cannot provide a reference), about a simple analysis that can be applied to any maintenance activity to improve performance. This analysis is call the 2 Up / 2 Down analysis.
The 2 Up / 2 Down analysis is quite simple and involves asking two questions.
What Did We Do Well and Need to Sustain?
Many people focus on their weaknesses, but why focus all your energy on weakness? Much more can be accomplished by focusing on the strengths. By taking the time to focus on what you and / or your team has done well, you can drive significant improvements.
After an event has taken place, gather the team and start asking what went well. During a significant failure, this may be difficult, but continue to push for what went well. After everyone has provided their input, determine the 2 activities that were completed and need to be sustained during a similar event. Dive into why they went well and what needs to be done to sustain them.
To sustain activities, checklists can be implemented, staging of materials, tools can take place, or the upskilling of staff.
A side benefit of this activity is that the team is taking a bit of time to reflect on their strengths and successes. It is easy to get caught up in the rat race and focus on what went wrong, but by talking about the benefits and success, the team moral and outlook will start to improve.
What Did We Do Poorly and Need to Improve?
Everyone likes to focus on their weaknesses, but that should only consume part of our time. The second step is identifying what activities did not go well during the event. With the activities identified, have an open conversation with the team to identify why these activities did not go well.
This is not a blame session, but a constructive discussion to identify what happened and what needs to be improved. For Shutdowns, it could be how to reduce the total shutdown time, or during failures, how the MTTR could be reduced.
Identify the Top 2 issues that need to be improved and brainstorm what can be done to improve it. Use the team to develop the action plan and implement the actions. These actions could include equipment standardization, checklist implementation, pre-kitted parts, etc.
Sometimes there is a debate about whether to do the positive actions firsts or the negative actions. I prefer to do the positive actions first as it energizes the team and gets the creative juices flowing. It helps with engagement and brainstorming when looking at the negatives.
Putting The Answers into Action
The entire exercise and analysis would be for nothing if the results are not used. That’s why it is vital to the success and improvement of the organization to use the analysis and implement the actions. All actions coming out of the analysis should be put into an action log and tracked to completion.
This 2 Up / 2 Down analysis can be used on all different maintenance activities (or any activities for that matter), so make sure to implement it. Use the analysis for failure responses, shutdowns, maintenance windows, anything and watch you plant and department performance improve.
Do you use the 2 Up / 2 Down analysis, or something similar? What have you implemented with the analysis to sustain it and ensure the actions are completed? What results have you seen since implementing a system such as this?
Remember, to find success, you must first solve the problem, then achieve the implementation of the solution, and finally sustain winning results.
I’m James Kovacevic
Eruditio, LLC
Where Education Meets Application
References & Related Materials:
Facilitation Skills Training
Leave a Reply