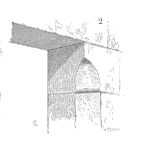
Embarking on a product development project contains many aspirations, including that the product should work as expected.
The device functions and does so over time. Enough time for the customer to deem the device reliable.
That is one way to approach setting a reliability goal for a project. Estimate what will delight the customer. Set a target for how long without failure your new design function.
The goal provides a focus for the team.
Where do reliability goals come from?
In some cases, they are little more than wishful thinking and quickly ignored.
Goals connected to customer expectations, business objectives and technically feasible add credibility to the goal and provide a touchstone for every decision through the product development process.
1. Customer Expectations
While shopping at an electronics store I overheard another shopper ask the clerk to pick out the computer that would not have any problems for at least 3 years. The clerk responded with a comparison of warranty terms and conditions to which the customer repeated his question.
Joining the conversation I reminded the clerk that the warranty is only good if there is a problem, and I too would like a machine that just worked. I like my fellow shopper did not want to call the friendly customer support people, at all.
When asked, customers do not want to buy items that will fail.
Likewise, design engineers do not want to create products that fail. Nor do manufacturers set out to create faulty products. The intent is generally clear. If the item is a phone or bearing the reliability of the item is expected. It’s just not well defined from the customer’s input.
In some cases, the customer specifies reliability clearly in the requirements. They may ask for a military radio that is 98% reliable over 5 years, along with functional and environmental requirements. (More often the military requirements are in MTBF, which generally adds to the confusion — which is a topic for another day)
Most customers also understand that products do fail on occasion.
Warranty elements of the purchase agreement provide protection. When asked a customer generally indicates they want a high probability of an item working over a duration. Some may be more risk adverse than others, and some envision using the product for longer than others. Yet, for any specific product, there is a set of probability of success operations and durations that will satisfy the bulk of customers.
Gathering and understanding customer expectations does take time. It may come directly from customer requirements or input, or from survey’s and interviews, or from customer behavior observation studies. Marketing, sales and support teams may have valuable insights to customer reliability expectations.
Ideally, if you set the goal to create products that will not fail. Given some number of products will fail and disappoint customers, what is an acceptable chance of failure over what duration for the customer.
That is a critical element of setting a reliability goal.
2. Business Objectives
The business objectives of customer satisfaction, market share, and profit intertwine with reliability.
When customers deem a product reliable, that product generally enjoys high customer satisfaction and increased market share. The profit targets are not interrupted by unexpected increases in warranty expenses or loss of market share.
Key elements of information to translate profit to reliability are expected failure rate and cost per failure. Along with volume shipping information, we can calculate the expected number of failures and the associated cost.
We can compare these projects against the budget and determine if the item is reliable enough or not.
3. Technically Feasible
Every design is a set of tradeoffs among the many requirements and objectives for a product.
Reliable is just one of many factors. Given the cost, time to market, and functionality requirements we also have to consider manufacturability, serviceability, recyclability, etc.
The product has to be reliable enough, not as reliable as possible. Consumer products with an expected useful life of 2 years do may not have to address long term wear out mechanisms such as metal migration or polymer creep, yet should focus on eliminating any failure mechanisms that may occur early in the life of the product.
“Gold plating” a design increases cost by using the best technology available, yet it may provide little to no improvement over the duration customers expect to use the product.
It is where the technical limitations of the materials or design constrain product reliability that we tend to focus when setting goals. What is possible?
Summary
Setting a reliability goal may include a broad range of information from customer perceptions to material properties.
In the end, it is a guide. The goal provides the team a means to make decisions. Setting a meaningful goal based on customer, business, and technical input provides a solid framework to build a product that achieves the goal.
Related:
When is the Best Time to Establish Reliability Goals? (article)
Guiding Programs by Product Goals (article)
Key Elements for Your Project Specific Reliability Plan (article)
Leave a Reply