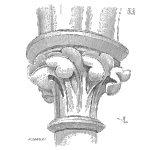
Do you have one in your organization? Is it used regularly?
If not, your organization’s products are likely not as reliable as they should be. You are shipping products that are not as robust nor reliable as your customers deserve.
Derating and Safety Factors, defined earlier, provide a means to select components or create design features that have sufficient margin to accommodate variation in use and strength over time.
So why are these tools routinely ignored or given only fleeting attention?
Well, they are boring, they tend to add cost and weight to a product, and the calculations take data and time to accomplish.
Reliability is just one of many objectives for a development team and often is not the single most important objective. Thus the constraints of cost, time to market, or functional capability tend to consume the resources available.
Create System of Use for the Manual
One way to incorporate the use of design guidelines is to create reinforcing processes around the use and benefits of using the manual’s guidelines.
Initially, the process requires a few cases studies to show following the guidelines saves
- total costs despite increased cost of components,
- time to market by avoiding last minute redesign work,
- and, product functionality by creating robust capability of each unit.
The idea is to celebrate those teams correctly deploying and using the manual. And building a set of ‘see it works here’ stories to share within the organization.
This build incentivizes to invest in meeting the design guidelines as the benefits become clearer.
A second system to reinforce the first is reviews and questions. We as design teams do what is measured. If we are only measured on time to market, despite understanding cost and reliability are important, we focus on time to market.
As with KPIs what we measure collectively and which measures dominant the focus matter.
Ensure the system of reviews, the questions asked and the measures tracked include the longer term results that include reliability performance.
Short term, too. At a design review simply do not focus only on the cost of the assembled components, include questions about reliability, durability, and lifecycle costs.
Derating and safety design guidelines are specific topics for review and discussion.
Did we, as a design team, meet every element of the guidelines?
Which elements of the design do not meet the guidelines and what is the impact? In short, is this the right decision?
Support with Appropriate Infrastructure
Regularly telling the story that using the guidelines is good for the customers and for the business is one step. Another is the tactical reinforcement of the expectation and review of the actual calculations and decision-making process.
Another element is the support of the ease of use of the guidelines.
Provide training and education support for anyone involved with the implementation of the guidelines.
Provide tools to determine tradeoffs between cost, time to market, customer satisfaction, etc. when meeting or not meeting the guidelines.
Provide visibility for the teams that achieve reliability objectives without heroic last minute or reactive measures.
Creating a set of guidelines for derating and safety margins is the easy part. Getting the manual off the shelf and into the design is not.
Senior management support certainly helps, yet alone is not sufficient. You need to create the reinforcing processes that encourage, check and reward implementation of the guidelines.
Further reading
Product Reliability Design Guidelines: The Design for Reliability Manual
Uprating is often possible because of the way electronic parts are designed and manufactured. The methods of uprating take into consideration the issues related to part testing and specification margins to assess the ability of the parts to operate over their target temperature range.
The uprating assessment of a part determines the electrical functional capability of parts in their target application conditions. This determines whether a part “can work” in a given environment.
However, to determine if a part “won’t fail” in the application environment, the reliability of the part needs to be determined for the application. The methods of determination of reliability can
vary and may include assessment of manufacturers’ qualification test results, additional tests performed by the equipment manufacturers and virtual qualification. (Ref: CALCE Rating and Uprating of Electronic Parts, Chapter 3)
Hi Hilaire, sure parts can be uprated, yet it generally comes at the expense of shorter lifetimes for the components. Just because it can work doesn’t mean it will work over the duration of interest. I do agree that understanding the tradeoff is key and means understsnding how the stresses applied impact the durability of a part.
Cheers,
Fred