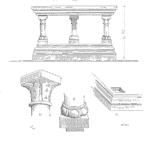
With any product development, there is a risk the features (benefit) come along with inherent dangers (risk). For example, a desktop computer includes the need for electrical power. Done improperly a person exposed to wall current and voltage could be seriously harmed. While unlikely the risk exists.
One of the reasons we rarely think about the risk involved with plugging in our computer is the design meets or exceeds basic safety standards. The ability of the cord’s insulation to isolate our hand from the voltage is sufficient.
Sure two bare wires would work to power our computer, and the chance that someone or something would short those wires is much higher.
There are three steps nationally recognized testing laboratories (NRTL) use to evaluate the system safety conformance.
1. Component review
The NRTL first evaluates the components within a product. If they are labeled and conform to the necessary safety standards, then component level testing is most likely waived.
If the fuses, motors, batteries and similar components are not UL (or other safety standard) approved, then they should undergo component level safety testing.
2. Product review
The NRTL reviews the component application, plus reviews the overall system for compliance with safety standards.
Even with appropriately safety rated components is used in the design inappropriately the components may not provide adequate protection or safety features.
The evaluation of the system includes the consideration of normal operation and single-fault conditions. This checks that the intended function of the product does not include unacceptable safety risks.
3. Construction review
Once the components and system are basically safe, the third step is to insure the assembled units shipped to customers are as safe as the system evaluated.
The NRTL creates a safety construction file which highlights the critical to safety assembly steps, plus details on the basic construction of the product. Then on a quarterly basis may review the actual assembly process to verify the construction maintains consistency with the approved ‘safe’ product.
The manufacturer must alert the NRTL of proposed changes for safety-related considerations before implementation.
While this basic approach is similar to inspecting in quality, which is less effective than designing in quality, it does provide a means to check and monitor basic safety compliance.
Each market and country may have different requirements, standards, and safety-related processes. The basic approach of designing a safe product is really the best approach rather than attempting to just meet the minimum safety standards.
Leave a Reply