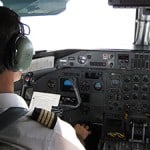
Using Procedure Based Maintenance to Improve the Performance of Your Operation
Imagine an operation in which there are no lost time accidents, OEE is increasing and there is a plan to address the skills shortage. These sites do exist and chances are they using procedure based maintenance. Procedure Based Maintenance is simply having all maintenance activities documented in a procedure. These procedures are then followed step by step when conducting breakdown, corrective and preventative maintenance.
Benefits of Procedure Based Maintenance
Procedure Based Maintenance reduces the variation that occurs where there are multiple craftsman conducting the work. It takes the learnings from all of the craftsman and incorporates them into the procedure. The end result is the safest, most efficient and reliable way to complete the task. Once Procedure Based Maintenance is put in place, the operation will see noticeable improvements in 5 key areas.
- Safety will improve as tasks are well planned out, with the risks identified. This allows the development of effective risk reduction activities. In addition the procedures can be used in the event of a failure, which can eliminate the risks associated with unplanned work.
- Improved Reliability as tasks are completed in a consistent manner with proper technical specifications. This reduces premature failures, and in the event of one, it can be analyzed to determine the root cause as the procedure and activities are defined and consistent.
- Reduction in Start-up failures as the procedure will ensure all bolts are tightened properly, the area is inspected and all foreign objects removed.
- Reduction in MTTR as a procedure is available which will reduce the time to repair as all of the required information is readily available.
- Knowledge Management is a major benefit of Procedure Based Maintenance as the experience and knowledge of the experienced craftsman can be captured in the procedure and transferred to the junior craftsman.
Get Started with Procedure Based Maintenance
Procedure Based Maintenance is used by many industries that require high uptime. Nuclear Power, Nuclear Navy, and Aviation to name a few. But just because these industries use it, doesn’t mean you can’t. Here is what you need to get started in Procedure Base Maintenance.
- Start by document the steps to complete the PM tasks. Walk through each task and document each step of the procedure, including any specific technical specifications. Once the procedure has been developed, be sure to review it and make sure the it represents the best practice in completing the task. This may take multiple revisions or reviews.
- Using the procedure above, create a checklist that can be used when completing the procedure. Checklists are used in all major industries as a way to ensure nothing is missed. There may be push back around using a checklist, as the craft may say they are skilled, but doctors and pilots use them to ensure nothing is missed.
- Define a training and certification program for the new procedures. This will ensure that the craftsman are trained in the task and Procedure based maintenance before being allowed to perform these critical tasks.
- Once the craftsman have been trained, be sure to reinforce the use of the procedures. Conduct audits to ensure they are followed, and that only trained personnel are using them. Try to reward those that embrace Procedure Based Maintenance as well.
- As more maintenance tasks are converted to procedures, develop and utilize a single template. This will ensure consistency across the organization, making Procedure Based Maintenance easier to implement and sustain
One of the questions I often get is “Who develops these procedures?” The task of writing these procedures best falls to the experienced craftsman who know the equipment and the task. By capturing the knowledge and insights of the experienced craftsman, the organization can begin to build a knowledge management system and bridge the gap of the skills shortage.
One caution with using a craftsman. Be sure to train them first on how to write procedures. The procedures need to be specific and actionable without any unnecessary information. I have seen this and the approach where the craftsman writes the procedure and then it is edited by a technical writer. Both approaches have their pros and cons, so be sure to choose the right approach for you.
How many operations do you know of that utilize procedure based maintenance? What will you do to implement Procedure Based Maintenance?
Remember, to find success, you must first solve the problem, then achieve the implementation of the solution, and finally sustain winning results.
I’m James Kovacevic
HP RELIABILITY
Solve, Achieve, Sustain
On one hand I fully agree that procedures are important.
On the other hand, procedures increase the risk of blindly following the maintenance steps, thereby missing important clues regarding other failure modes.
What do you think?
Hi Amir,
I believe that procedures are required, take for example pilots, military or other high performing occupations. In these occupations, there is just too much information to retain for an individual, however, these occupations have the intelligence and know-how to react to changes and outside stimulus.
This is no different than maintenance and reliability professionals. The procedure provides them the details to make repeatable reading and prevent maintenance induced failures, but they must use their knowledge and experience to deal with the exceptions such as other failure modes.
James