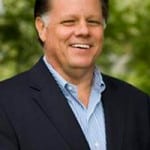
When I started to develop the RCM Blitz™ methodology over twenty years ago, the one thing I knew that would help to ensure successful Reliability-Centered Maintenance analysis was to develop a way that would guarantee every implemented analysis would provide a return on investment. The answer to this was simple enough, if you’re looking to improve safety and reduce health, safety and environmental incidents we should focus on critical assets that are struggling to maintain their inherent designed reliability. The best way to identify the best candidates is by measuring the OEE (Overall Equipment Effectiveness) of your top critical assets.
While this sounds simple enough, I truly wasn’t prepared to discover that most of the locations I would visit in the coming years would struggle with obtaining what I consider a simple measure.
The excuses were common;
“We don’t record the variables that make up that measure.”
“We have never been able to agree on what the different parts of OEE mean.”
“We tried to measure OEE a couple of times and found it didn’t work for us.”
“OEE is a meaningless measure of a continuous process.”
“OEE doesn’t work for our industry (Oil and Gas, Utilities, Mining, Food Production, etc.)”
Truth be known, I’ve heard every excuse in the book and they are all flat out wrong! OEE works, regardless of what business you’re in, you just need the discipline to learn how OEE should be measured and used. If OEE isn’t working for your company, chances are you’re doing something wrong and it’s likely one these 5 things.
The 5 OEE Wrongs
- You’re Measuring OEE Just to Know The Number – This would be the most common mistake. Seiichi Nakajima defined OEE in very simple terms (OEE=Availability x Performance x Quality) and this is where most companies stop. They look at their production numbers, perform the calculation and stop. On its own this number is truly meaningless. What do the numbers 76, or 92 mean when I comes to OEE? If you don’t understand the objective of why you need to measure OEE the two numbers mean absolutely nothing. What process or machine was being measured? What was the time frame of this measure? What product was being produced? More important, what caused the losses for each number?
- You’re Measuring OEE at the Wrong Level – Almost as common as number 1 is the complete waste of time companies spend measuring OEE for their entire plant, or building. The true objective of OEE is to identify and reduce your losses. Trying to do so at a plant or building level will never provide the clarity needed to do this. Stop wasting your time!
- You Arbitrarily Set Goals to Improve OEE – While it might seem natural to want to improve the OEE numbers on your critical assets, setting a goal and putting it up on a bulletin board or score card of some sort isn’t going to make it happen. There should be only 1 goal when it comes to OEE, identify and eliminate losses.
- You Manipulate OEE to Fit Your Needs – I’ve seen it all when I comes to OEE manipulation. From stretching quality standards, to adjusting the time someone started a production line because it took two hours to get a case erector to make the first good case, manipulating the data hides the one thing you should be focused on, the losses associated with each part of the measure.
- Creating Your Own OEE Calculation to Fit Your Needs – While some might raise their eyebrows at this, a simple Google search of OEE Formulas will show you just how common it is. Every customer I know of that developed their own OEE calculation did so because they wanted their numbers to look better. The worst thing anyone ever did for this solid reliability measure was make the statement that 85% was world class OEE. That statement is pure nonsense! As an example, If I were measuring OEE for an electric turbine, 85% would be horrible. If I were measuring OEE on batch process making a pharmaceutical product 75% might be fantastic.
The 5 Right Things To Do When Measuring OEE
- Focus On Identifying and Eliminating Losses – Start at the top and communicate to everyone in your workplace that the objective of measuring Overall Equipment Effectiveness is to identify and eliminate losses. Your goals in doing so should all be centered around this objective. It should be made 100 percent clear that while we need to measure our machine rate, each time it is not making rate we need to document the cause. While we need to always make good quality product, we need to document the reasons we make off spec product. And, while its highly important that our equipment is available to make product, we need to document the reasons it wasn’t available. With this documentation we can Pareto each category we can now identify the best Reliability Tools to work on eliminating these losses. Reliability Centered Maintenance (RCM Blitz™) for eliminating equipment and process based losses, Root Cause Analysis to address random failure events and quality tools to identify and eliminate quality losses.
- Measure And Review Often – I recommend that Operations Team Leaders should be responsible for performing the data collection as well as identifying the causes in each loss category. The data should be made available to all stakeholders immediately and provides for an excellent discussion at shift change. Making the data, the calculation and list of causes for each loss category will not only ensure the data is accurate, it will drive people to better understand and begin working on loss/defect elimination.
- Understand the Power of Stability – Every process or piece of equipment we measure has its upper limit when it comes to OEE. That limit is known as the inherent designed reliability is determined in the equipment design phase. The only way to determine this OEE number is to continuously identify and eliminate losses until the machine or process stabilizes. The beauty of reaching this goal is we can now accurately plan and schedule production. Understanding this, tools like Just in Time will now actually begin to work in your favor. You will be able to accurately order in-process inventory and deliver finished product to customers day in and day out!
- Celebrate Defect Identification and Elimination – Identifying and eliminating defects doesn’t come without work. We need to recognize those who are working to collect data, communicate causes and work with the right tools to eliminate the losses. Set these positive reinforcement goals around proactive leading indicators such as causes identified, and loss elimination events performed. (RCM, RCA, SPC) I have always told my clients that OEE isn’t just a measure, it’s a reliability tool that will lead us to continuous improvement. It’s also a tremendous opportunity to identify the real leaders in your organization. Those who can identify problems and lead others to resolve them are the people you should be promoting in your business.
- Achieving Your Goals? Add More Assets – I opened this article pointing out that OEE should be measured on critical assets that are struggling to maintain their inherent designed reliability. Its important to understand that as we eliminate losses and achieve the inherent reliability of these assets the criticality will shift and other assets that may have not made the list will now become your focus. I like to tell people that reliability is always a moving target and improvements we never thought were possible in the past will become a reality if we recognize this.
The key things to remember, collecting OEE data is much easier than you think, focus on understanding your losses and using the right tools to reduce those losses. This measure is a tool that once you understand its power, you’ll wish you had been measuring reliability all along.
Leave a Reply