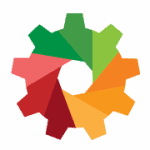
Maintenance of different equipment within a facility remains a core enabler of improved productivity and efficiency of plant processes. Poor maintenance practices lead to machine downtime, increased operational costs, and increased maintenance workloads.
Reducing maintenance workload can’t be done overnight, but it is a goal worth pursuing. Less maintenance work performed (without an increase in reactive maintenance work) means less resources spent – fewer spare parts used, less overtime work, and improved employee satisfaction that can actually increase the average quality of performed maintenance work.
Let’s check a few ways in which maintenance teams and plant managers can effectively cut down maintenance workloads.
Adoption of suitable CMMS combined with predictive maintenance
Different maintenance strategies operate on different maintenance workloads. For example, it is obvious that when you schedule maintenance work using condition monitoring technology and predictive algorithms, the amount of work performed will be close to optimal, eliminating chances where you might be doing excessive maintenance. You can then combine PdM with CMMS to automate part of your WO process by letting CMMS automatically schedule tasks when sensors show certain levels of deterioration (or based on other triggers).
Additionally, CMMS solutions with an inventory module can also help maintain a lean inventory list, allowing teams to efficiently manage spares and tools necessary for either proactive or reactive maintenance needs. Availability of adequate spare parts and tools ensures that maintenance operations are carried out at the designated time, preventing a situation where a task has to be repeated or postponed in the middle of its execution.
Lastly, running maintenance tickets through CMMS ensures that no work is forgotten or duplicated, which again reduces the total amount of time that will be spent on unproductive maintenance work.
Maintenance Planning, Scheduling and Work Allocation
Planning and scheduling matches qualified teams to specific maintenance tasks, assigning unique work tickets to list of maintenance tasks, and preventing clashes in work assignment. Planning assists teams to map out appropriate communication channels while undertaking maintenance.
Workloads can be reduced by allocating more maintenance personnel to demanding maintenance tasks. Some work intensive tasks require additional personnel on site. For example, there might be a maintenance task that takes an hour to perform alone, but only 20 minutes if it is done by two technicians. Doing some simple math shows you how having two technicians on that task actually saves you 20 minutes.
Prioritization of tasks forms a critical part of maintenance scheduling, allowing teams to work on highly critical tasks. A well-structured priority list will ensure tougher tasks are carried out ahead of simpler maintenance tasks. Failure to plan or manage work priority can overwhelm maintenance teams and cause a huge pile up of tasks, which can lead straight to reduced performance. Luckily, planning and managing work can be optimized using CMMS system or a simple maintenance ticketing system.
Effective Root Cause and Failure Mode Analysis
Unplanned machine failures cause avoidable downtime and a spike in maintenance workload. Preventive some of those failures in the future require some investigative work.
The huge workloads can be reduced by maintenance teams trying to establish the root cause of the problem. For instance, maintenance teams may be called upon to repair a huge gas leak within a production plant. Replacement of gas pipes may not entirely solve the problem, especially if it actually arose from a faulty pressure gauge. Proper root cause analysis will enable the teams to pinpoint the main cause of the issue and avoid a recurrence.
Proper identification of the failure root causes, as well as FMEA analysis, will advise the most appropriate course of action. It will help maintenance supervisors to adjust their maintenance schedules by eliminating unnecessary maintenance tasks and focusing only on work that has the highest chance to prevent future failures.
Continuous technician and machine operator training
Skilled maintenance technician that is confident in their work, when compared with someone who is unsure and inexperienced, is bound to finish a given task in a shorter time without compromising on the quality of the performed work. Proper training creates familiarity with maintenance requirements (and assets), which reduces workloads as technicians are capable of handling complex tasks correctly and quickly at first instance. Doing the work correctly the first time means nobody has to waste time cleaning up the mess left by their colleague. This reduces the repetition of work, which translates to reduced maintenance workload.
Similarly, it is important for machine operators to know their assets. They need to understand the safety requirements, operating guidelines, and working limits of equipment. Equipping operators with basic maintenance knowledge ensures that errors are reported in advance and rectified appropriately, thus reducing workloads. Ambitious departments can even try to implement autonomous maintenance, where routine maintenance tasks are given to operators to free up maintenance techs for more complex tasks.
Conclusion
Adopting these approaches can lead to a compounding effect and significantly assist maintenance teams to better distribute and manage workloads at any given time. This directly translates to cost savings, improved plant efficiency, and increased productivity.
Leave a Reply